3D-Printing Materials
New 3DP printers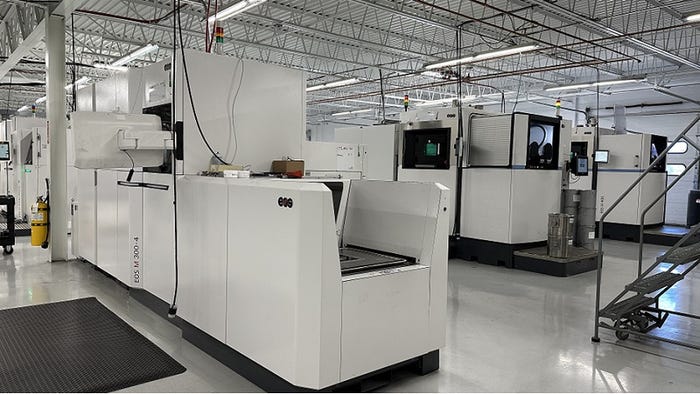
3D Printing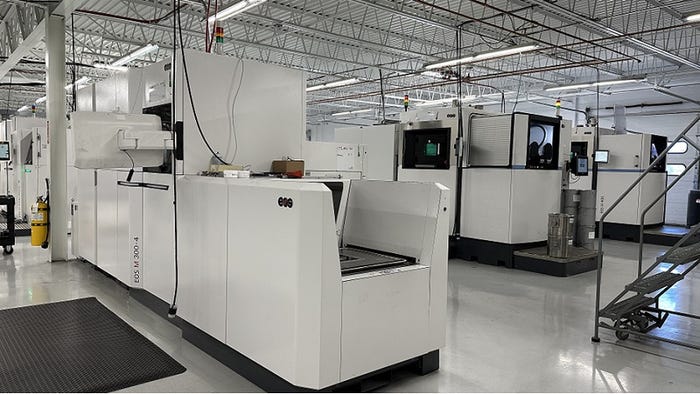
Materialise Introduces New 3D Printing Materials and More 3DP NewsMaterialise Introduces New 3D Printing Materials and More 3DP News
We’re also looking at a new IDTechEx 3DP market analysis report and new 3D printing software from HP.
Sign up for the Design News Daily newsletter.