Motion Control
data-signal hybrid connectors 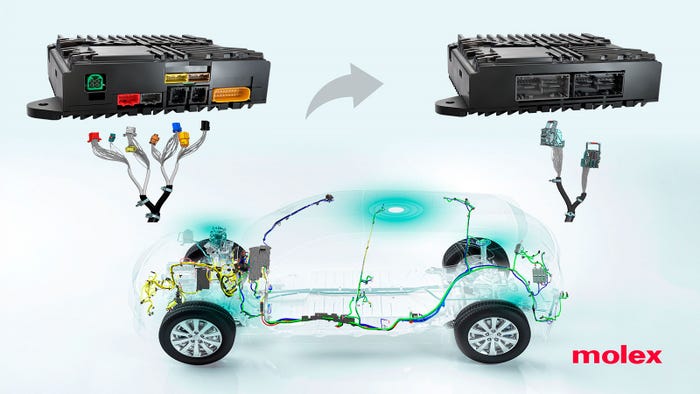
Industry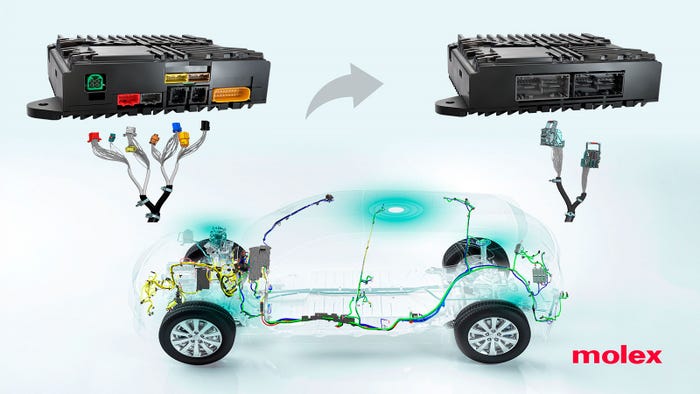
Green Energy Buffering Is Cleaning up in Supplier NewsGreen Energy Buffering Is Cleaning up in Supplier News
We’re also looking at data-signal hybrid connectors, pressure control valves, and high-speed actuators.
Sign up for the Design News Daily newsletter.