Motion Control
thumbnail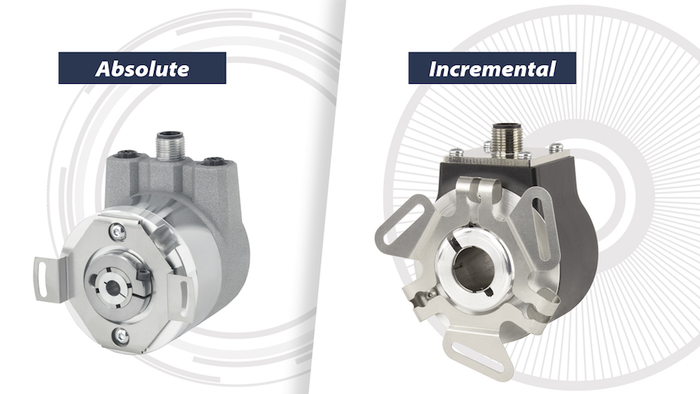
Sponsored Content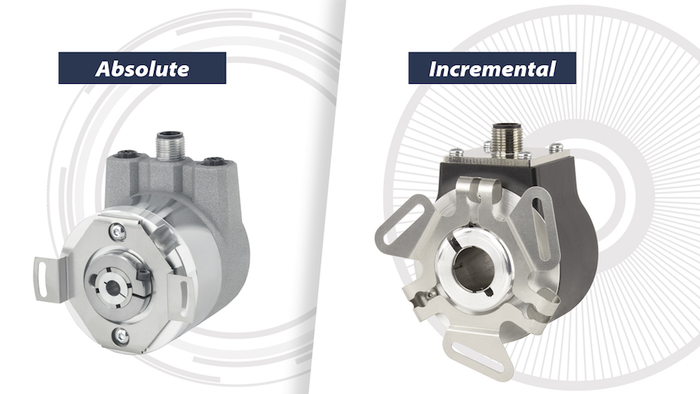
Absolute vs. Incremental Rotary Encoders: Which is Best?Absolute vs. Incremental Rotary Encoders: Which is Best?
Both types of rotary encoders provide motion sensing and feedback about a rotating shaft. Knowing their differences will help you choose the right type for your needs.
Sign up for the Design News Daily newsletter.