Motion Control
Siemens SIMATIC Workstation 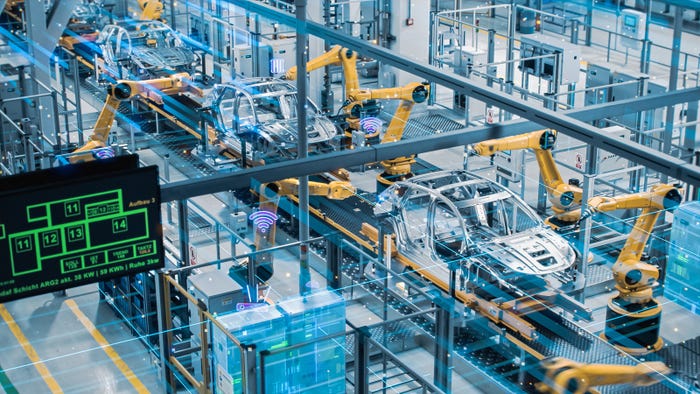
Automation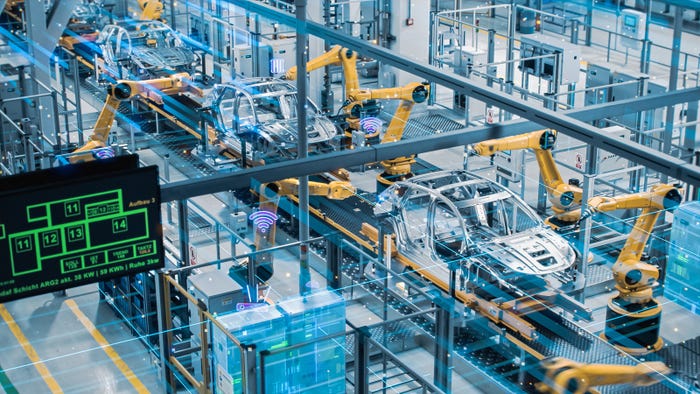
Siemens Unveils SIMATIC Workstation that Swaps Hardware for SoftwareSiemens Unveils SIMATIC Workstation that Swaps Hardware for Software
Siemens worked with co-creator Ford to add AI to automation while blending IT and OT and integrating HMI.
Sign up for the Design News Daily newsletter.