Simulation
Manufacturing jobs shortages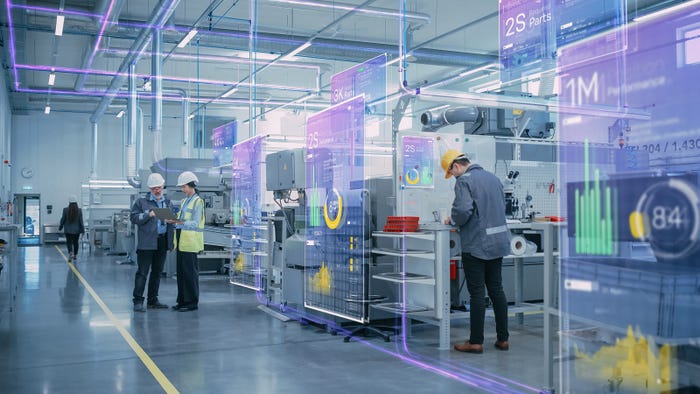
Automation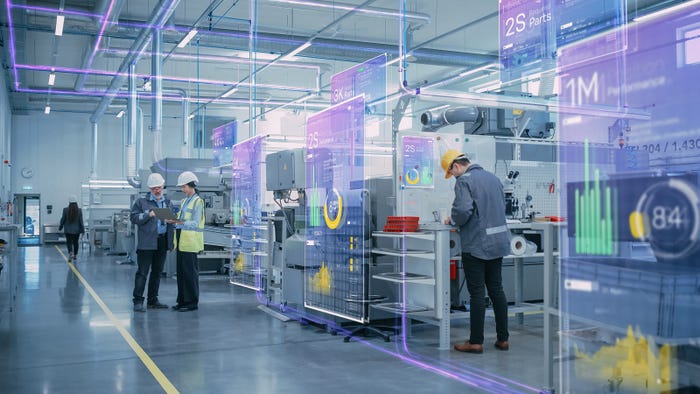
Manufacturers Will Need 3.8M New Workers by 2033Manufacturers Will Need 3.8M New Workers by 2033
Expanding US manufacturing will exacerbate the shortage of skilled plant workers over the coming decade.
Sign up for the Design News Daily newsletter.