Testing & Measurement
NASA uses planes to study solar eclipse.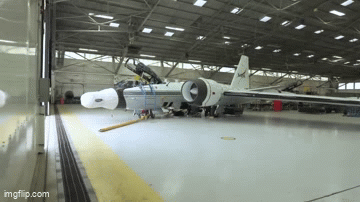
Aerospace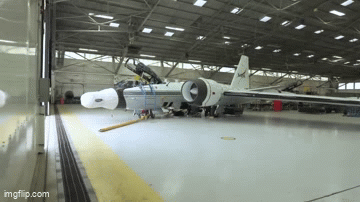
Catching the 2024 Solar Eclipse at 50,000 FeetCatching the 2024 Solar Eclipse at 50,000 Feet
A total solar eclipse occurring April 8th is getting NASA’s full attention, as the agency is deploying two manned jets to chase and study the eclipse in detail.
Sign up for the Design News Daily newsletter.