3D printed micro parts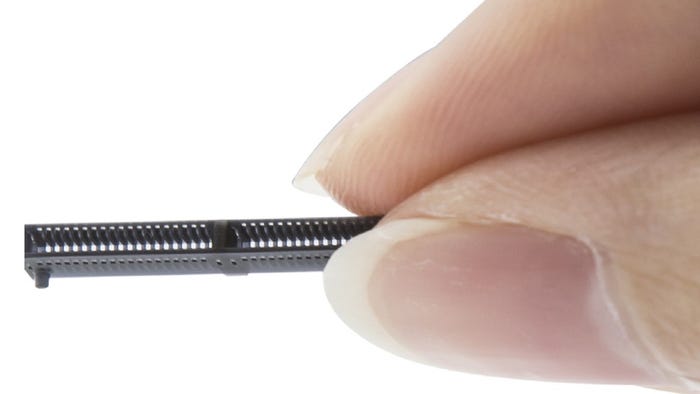
3D Printing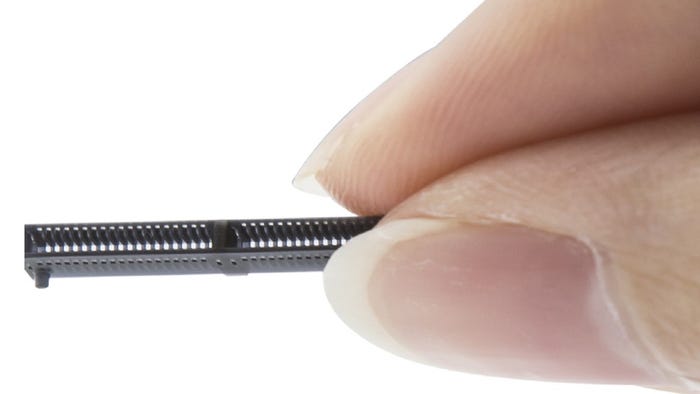
Industry Voices: Is Micro-3D Printing the Future for Tiny Parts?Industry Voices: Is Micro-3D Printing the Future for Tiny Parts?
Additive manufacturing is becoming an efficient and cost-effective alternative to traditional micro-manufacturing methods such as molding.
Sign up for the Design News Daily newsletter.