Pirelli's P Zero E contains 55 percent bio-based and recycled material.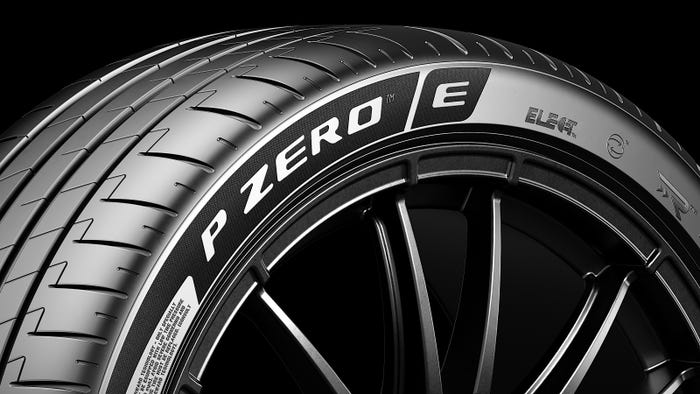
Automotive Engineering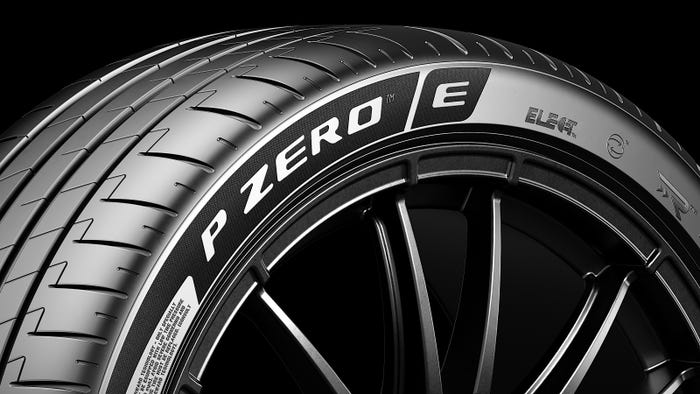
Pirelli Tires Aren't Just Round, They're Circular!Pirelli Targets Circularity for Tire Materials
The wheels on the bus may go ‘round and ‘round, but Pirelli is focused on a different kind of circularity for its tires.
Sign up for the Design News Daily newsletter.