Automotive Engineering
More Topics
Toyota's Princeton, Indiana plant.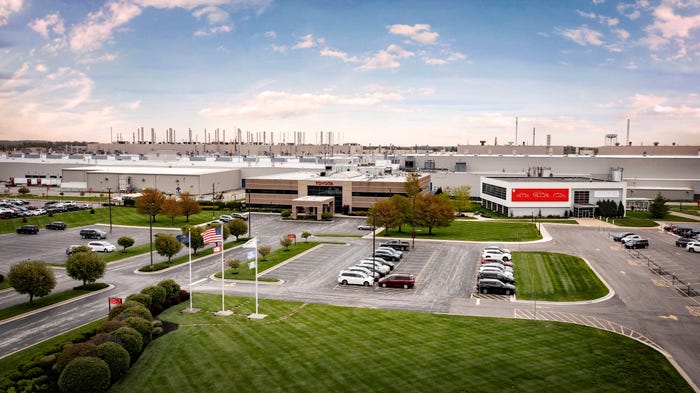
Automotive Engineering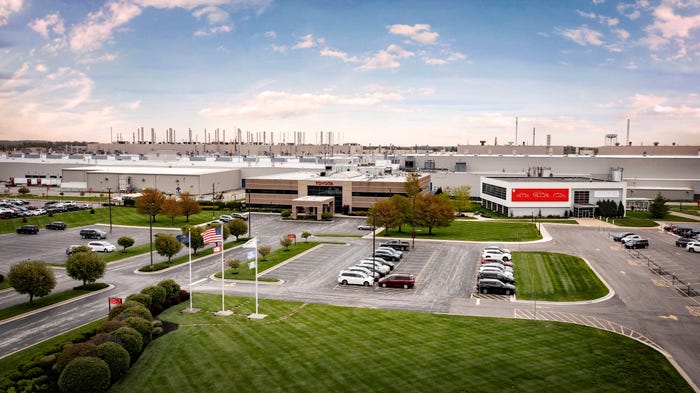
Toyota Announces Indiana Production for New 3-Row Electric SUVToyota Announces Indiana Production for New 3-Row Electric SUV
Toyota will add 340 jobs at its Princeton, Ind. plant for a new electric SUV.
Sign up for the Design News Daily newsletter.