Driving High-Brightness LEDs in High-Power Industrial Lighting Fixtures
April 21, 2014
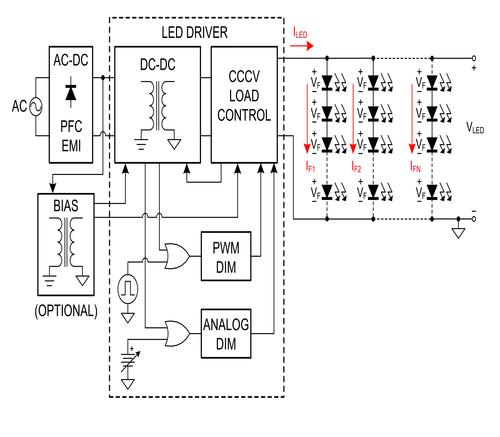
High-power industrial Light Emitting Diode (LED) fixtures use series-parallel strings of High Brightness (HB) LEDs to produce superior lighting fixtures compared to traditional, "ballast-based" systems. HB-LEDs are configured in series or series-parallel strings. They require constant-current, constant-voltage (CC-CV) power supplies, operating within the range of 50W to 200W. Industrial LED lighting systems operating from a universal, offline AC voltage must include the ability to maintain a high power factor over a wide range of input and output operating conditions. For example, meeting the Department of Energy (DOE) Energy Star Program for solid-state lighting explicitly requires a minimum power factor of 0.7 and 0.9, respectively, for residential and commercial fixtures greater than 5W. In addition, the European standard, EN61000-3-2, for Class C lighting equipment imposes stringent THD limits most easily met using active power factor correction (PFC).
The block diagram shown in figure 1 highlights the functional requirements for a typical industrial LED lighting system. Although not always the case, the PFC function is shown outside the LED driver block for this example. There are several widely accepted control methods used for achieving PFC, but for power conditioning in the range of 25W < POUT < 200 W, boundary conduction mode (BCM) PFC is an optimal consideration for meeting EN61000-3-2 and maintaining high efficiency. BCM PFC benefits from the use of a smaller, more efficient boost inductor. It exploits the use of zero-voltage switching (ZVS) and zero-current switching (ZCS) to maintain high efficiency. From a power-conditioning point of view, the goal of a PFC circuit used in LED lighting is no different from most other AC-DC power applications, such as computing.
The LED driver is comprised of the DC-DC converter; load control; LED-specific functions, such as dimming; and any necessary protection functions. The DC-DC converter provides safety isolation from the AC mains while converting the high-voltage PFC output to a DC current suitably matched to the requirements of the LED load. The LED load control is necessary for current sharing when several, series-parallel LED strings are used in high-power LED fixtures.
In some cases, the DC-DC and load control blocks, shown in figure 1, can be combined where the load control provides CC-CV feedback information to the DC-DC converter. Under normal operation, the LED driver should operate in CC regulation. However, there may be times when the driver should operate in CV mode.
For example, if the LED string voltage increases beyond some maximum rated value, the driver needs to respond quickly by changing from CC to CV mode to protect the DC-DC converter power-stage components. When the driver is operating in CV mode, the LED current should be limited or folded back, providing over-current protection to the LED load. In addition to power conversion and load control, a secondary function of the driver is to enable dimming capability.
There are many different configurations for operating dimmable LED light fixtures. Industrial LED lighting systems typically use an analog or PWM dimming interface in conjunction with occupancy sensors, daylight sensors, and other controls to optimize the most efficient light use. Analog dimming uses a 1V-10V (or 0V-10V) DC control voltage to adjust LED brightness linearly by controlling the LED DC current. A 1V-10V control voltage adjusts the LED dimming range from 100% (10V) to 10% (1V). Because the light output can only dim down to 10%, a separate switch is required for on/off control.
Similarly, a 0V-10 V control voltage should result in 100% LED brightness at 10V. Any voltage less than 1V produces "minimum" brightness. Minimum brightness is the lowest current level that the driver can manage. Some drivers' minimum output is off, while other drivers' minimum can be as high as 10%. Incompatible 0V-10V operation among different drivers is one of the disadvantages of analog dimming. Also, since the LED current level is directly affected, the LED light output can experience a visible color shift. Analog dimming is therefore not preferred in applications where accurate color temperature is critical.
PWM dimming adjusts LED brightness by varying the amount of time forward current is flowing through the LED. The LED is switched on and off at a frequency greater than 100 Hz. It is considered that 100 Hz is a high enough frequency that most people cannot detect the presence of LED flicker. The human eye "averages" the switching LED current and perceives a change in brightness proportional to the on-time of the LED. Many controllers used in LED drivers have dedicated PWM dimming inputs compatible with a wide range of PWM frequencies and amplitudes. Pulsing the current allows the LED to be on at full-rated current during the time that the PWM signal is high. The advantage this has over analog dimming is that the color temperature is accurately preserved, and no color shift is detected during dimming. Whether using analog or PWM dimming, the input signal can come from the DC-DC converter directly or remotely, as shown in figure 1, by the ORing function feeding each of the dimming blocks.
A high power factor, safety isolation, dimming compatibility, constant current accuracy, and LED load control are a few examples of requirements challenging today's power electronics design engineers. How do you begin to sort through the trade-offs of meeting such requirements while maintaining high efficiency? What are the considerations between different power topologies suitable for LED drivers in this power range? What are some of the other CC-CV LED current sharing methods used in the industry, and what is Fairchild doing to address these needs?
For the answers, be sure not to miss the 2014 Fairchild power seminar series, where we will delve deep into the details, unveiling a step-by-step design approach of a scalable, 100W, LED driver suitable for a high-power industrial lighting fixture. Magnetic component design, gate drive, PFC, and analog circuit design will also be presented in a way that promises to be relevant for power electronics engineers whose interests may not be focused specifically on LED driver applications.
Steve Mappus is a principal systems engineer working in Fairchild Semiconductor's Power Conversion group.
Related posts:
About the Author(s)
You May Also Like