Polymer bearings: lots of mileage left in 'em
October 5, 1998
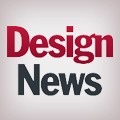
Port Washington, NY--"Nyliner(reg) polymer bearings are one of the few products that have not been replaced by a microchip," quips Doug Caldwell, product manager, molded products, Thomson Industries.
But it's no joke. This year alone, Thomson Industries has seen a 30% rise in demand for its venerable line of injection-molded bearings. The sales spurt is all the more impressive when you consider the product line has been around for nearly half a century and has been averaging double-digit growth in sales over the past 10 years.
Demand for Thomson's injection-molded polymer bearings has always been strong in the auto industry, with applications as diverse as brake and clutch assemblies, deck lid hinges, and truck suspensions. (Thomson engineers estimate that Nyliner(reg) bearings can be found on 80% of all domestic vehicles.) And they are widely used by OEM designers of all types of machinery to achieve smooth, low-friction motion.
The rise in popularity of polymer bearings has been partly at the expense of sintered bronze bearings, which perform well in brake, clutch, accelerator, and windshield wiper pivot applications. But sintered bronze is not always as cost-effective in these applications, where literally tens of millions of polymer bearings have displaced them.
Ease-of-use is another reason for the wide use of polymer bearings: they are made of wear-resistant materials with low coefficients of friction and require only a few drops of oil during their break-in period. Wafer-thin walls (as little as .023 inch thick) also mean they don't take up much space.
As for the recent surge in sales, Caldwell credits a growing preoccupation on the part of the automakers to eliminate every bump, squeak, and rattle--BSRs, as they say. At 3 to 8 cents per piece, Nyliner(reg) polymer bearings in any application act as a vibration and noise dampener. Automotive engineers are finding them to be an effective, simple solution in applications ranging from manual-transmission fork bearings to auto seat back pivots and instrument panels.
Over the years, Thomson engineers have also worked to continually extend the line's capabilities, adding new items (there are now 400 distinctly different products) and extending the operating range. No small feat, given that the bearings are essentially single, molded parts. "It's not high drama here," says Caldwell. "But the best products are usually the simplest."
About the Author(s)
You May Also Like