Motors target constant-velocity use
June 19, 2000
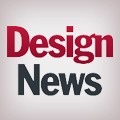
Cheshire, CT -Need constant velocity in your motion-control application? Consider an outside-spin motor. Designed with a spinning external rotor, Thomson Airpax Mechatronics' motors have three design features that reportedly help cut the cost in half compared to inside-rotor brushless dc designs. Greater magnet surface area allows lower-cost ceramic magnets, and permits a larger mechanical air gap that reduces matching tolerances. And outside spin motors are more economical to wind.
But while an outside spin motor's high inertia helps maintain constant velocity with small step changes in the load, it's a disadvantage when accelerating up to speed. While a typical inside spin motor may reach running speed in about 10-50 msec, outside spin designs may take 25-500 msec, explains Airpax' Product Marketing Manager Walt Kalwara. "So when optimizing acceleration in outside spin applications, inertia matching is critical."
Both new series of Airpax outside-spin brushless dc motors were designed for paper transport applications in office automation where, according to motion control consultant Gurdial Singh, EMI (electromagnetic interference) is driving the changeover from brushed to brushless motor technology. "Office automation OEMs almost have to make the switch from brush motors to brushless to meet the new CISPR 22 EMI regulations that dictate a 30 dBa level maximum," says Singh.
Designers of copiers and printers that have traditionally used brush-type motors are looking for a low-cost brushless solution to improve EMI. "That's why cost was king in designing these motors," says Kalwara. And one reason why both series integrate electronics such as a three-phase MOSFET PWM drive, and surface-mount components to eliminate the need for external controllers.
Both 58-mm and 98-mm lines achieve 100W-peak output power, and operating speeds between 100 and 3,000 rpm (without dynamic balancing), or up to 10,000 rpm (with dynamic balancing).
The combination of design features results in 20% lower overall power usage than other brushless dc motors and external controllers of equivalent size, and is 30% more efficient and 33% smaller than industry-standard packages, according to Kalwara. Other performance benefits include:
High-efficiency-proprietary drive electronics allow the motors to achieve 75% peak efficiency, which is 30% better than the industry standard.
Electronically quiet-low EMI levels of &30 dBa are typical and satisfy U.S. FCC and European (CISPR) standards.
Speed stability-Proprietary onboard circuitry plus a velocity tachometer minimizes speed variation and contributes to 20% lower distortion of running speed.
Quick deceleration-Motor's control circuitry provides dynamic braking when the motor is disabled, critical to applications where a quick stop must be maintained.
Cooler operating temperature.
"While designed with office automation in mind," says Kalwara, "the outside spin design is terrific for anything with constant velocity such as timing belts, mail sorting/handling, medical pumps, centrifuges, web process control, and industrial automation."
About the Author(s)
You May Also Like