Sensor adds zip to desktop scanner
August 14, 1995
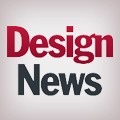
Cambridge, MA--In the thirty seconds it takes to read this, Polaroid's new scanner can digitize a color slide at 2,700 dot-per-inch resolution.
The SprintScan 35, which also handles 35- mm negatives and black-and-white film, lets graphic-arts professionals bring images into the computer five to fifteen times faster than other scanners, say independent researchers Rich and Associates, Olney, MD.
Key to its speed is a charge-coupled device (CCD) sensor chip that uses a linear array of many light-sensing elements to capture the image. Engineers adapted existing CCD technology to the scanner to speed the design cycle. Algorithms convert film negatives into the colors you'd see in a photograph, and custom ASICs automatically balance color and correct brightness.
Speed isn't the SprintScan's only claim to fame. From the outset, Polaroid wanted to create an inexpensive, user-friendly scanner. To reduce tooling and manufacturing costs, they teamed with Taiwan-based Microtek Corp. Their strategy: Rev up Microtek's low-cost base-model scanner with new optics and sophisticated imaging electronics from Polaroid.
"Our philosophy was to carry ease-of-use into the user interface with the software, and get the complex hardware to meet the demands of an unknown variety of films coming in," explains Stuart Boyd, scanner engineering manager of Polaroid's Electronic Imaging Systems. "We applied our image science to give the user the best result, and to hide this complexity."
Moving pictures. Like most desktop scanners, the Sprint-Scan uses a motorized carriage to guide the slide or film-strip past a stationary scan head. A lamp inside the scanner illuminates the slide, and the CCD light sensor on the other side captures the signal.
To achieve high resolution, Polaroid engineers had to devise a way to precisely move the slide past the CCD sensor. For Advanced Mechanical Engineer Colin Kernan, that meant using a lead screw and dc stepper motor from Teco Electric and Machine Co., Taiwan, to match the carriage movement to the timing of the charge as it moves across the 4,000-pixel CCD.
"The sensor is looking at a single line as the image is moving, and we had to pace that movement with each line of the CCD," says Kernan. "It takes a certain amount of time for the charge to move from pixel number one to pixel 4,000 on each line. And it takes a certain amount of time for the charge to work across from the first pixel on line one to the 4,000th pixel on line 64. I had to match that with the movement of the lead screw."
Because the sensor reads red and blue channels separately, any slip in timing results in color mis-registration, or a blurry "fringe." And because pixel size on the film at 2,700 dpi is less than 0.0004-inch square, specifying the tolerances on the lead screw for the 64-step motion proved difficult. "My tolerance was basically the distance I had to travel, about 0.023 inch, plus or minus 0.0003 inch. That called for a fairly accurate lead screw," recalls Kernan.
Engineers allowed less than 0.5 pixels of color mis-registration. But that margin only accounted for straight vertical motion--not factors such as vibration caused by the film's movement.
For example, at the highest resolution setting, the scan mode is also the slowest motor speed. Unfortunately, that speed coincides with the resonant frequency of the motor--resulting in vibrations or "ringing" as each step settles.
To damp motor vibration, engineers ruled out using a viscous fluid because at high-speed the inertial load increase and low torque would cause stalling problems. Substituting a larger motor wasn't an option, either, because engineers weren't sure of production volume and wanted the price efficiencies of sharing a motor with the Microtek design.
"Instead, we used an electronic damping system. Just before the motor stops at a step, you tell it go in reverse, then finish the forward step," explains Kernan. By building and analyzing a very accurate mathematical model of the whole system, vibration specialist Joseph Deck fine-tuned the system and programmed a chip to control the driver circuit.
Rapid image-capture. The CCD sensor at the heart of the scanner uses multiple rows of light-sensing arrays. An architecture called time-delayed integration (TDI), originally developed for military aerial reconnaissance, takes advantage of those arrays to increase sensitivity.
Image Sensor Device Engineering Manager Selim Bencuya explains, "as the image mechanically moves across the sensor plane, a particular place in the image is sampled once by the first line. Then--because the signal moves at the same speed as the slide--the sensor samples the same location in the image N times," where N is the number of rows of light-sensing arrays. The result: Fast image-capture in a fraction of the time of a conventional scanner.
Capturing image data is only half the scanner's job, however. To manage image enhancements and help control costs, Polaroid engineers designed custom ASICs. "Our horsepower comes from ASICs, which are low-cost on a piece-part basis," explains Bencuya. They further re-duced the imager cost by partnering with IBM and others for CCD manufacturing.
Early in the design, image-science engineers worked with the CCD hardware team to balance the sensor's color filters. Later, much of their work involved image processing. Processing negatives--with their inverted colors and characteristic orange mask--proved a Herculean task.
To transform the inverted colors and the orange mask from a negative and map them to a properly rendered picture on the monitor, engineers in the image-science lab created 3-D lookup tables. Those tables were then loaded to Polaroid's "Escapade" image-processing ASIC chip.
"It took a lot of work to generate a method for loading the Escapade chip with lookup-table values," recalls Principal Engineer Andy Juenger. "We had to go through a calibration procedure that involved exposing the film and measuring its properties, then using that data to generate the coefficients for the color transform."
To accommodate a variety of film types, engineers calibrated lookup tables for each type of film. "The user picks their film from a list, and that has associated with it these coefficients," explains Juenger. "The Escapade chip uses the coefficients to do the color transform and sharpening, and sends that output to the monitor."
To automatically correct for improper exposure, flawed film processing, or developing errors, engineers created two proprietary algorithms. One corrects image brightness by automatically compensating for colors that are too dark or too light. That algorithm makes under- and over-exposed negatives look good on the monitor. The other algorithm adjusts color balance. For example, it corrects the green or yellow tinge of outdoor film shot under fluorescent light.
Simultaneous software development. While the hardware and image-science groups struggled to perfect images, engineers on the software team were busy creating the software that the end-user and scanner would use to communicate with the host PC. "We developed the application software at the same time we were developing the test software, and at the same time we were developing the SCSI-2 interface," says Senior Engineer Mike Dichiappari. The scanner comes with a Photoshop plug-in utility, and the interface closely resembles the standard Macintosh format.
Software engineers took advantage of the ASICs to deliver instant updating of the image in its internal frame buffer when the user changes image-processing parameters. The user can increase sharpening, for example, then read the image back from the scanner in less than a second.
Engineers incorporated the driver into end-user software and the diagnostic software. Next, they built diagnostic applications with LabVIEW(R) software from National Instruments. "We created a virtual instrument out of the scanner, and once we'd done that, we could develop tests to analyze the performance of the scanner," explains Boyd. The results of those tests could be sent back from Taiwan, giving engineers a report on the assembly process. "LabVIEW was a key strategic tool. Now, we can use the same tools to analyze competitors on our own terms," says Boyd.
In many cases, engineering cross-training came in handy. "We have a design engineer who could function in a manufacturing mind-set," recalls Boyd. "One software engineer is a photographer, and a huge collection of her images were available for testing."
Polaroid engineers also credit the combined experience individual members brought to the project from related work. "The beauty of the design, and the reason we were able to go from first prototype to product in less than a year, is that we designed enough flexibility in the imaging architecture ahead of time, so that we could make small changes in off-the-shelf components and have it work," says Senior Engineer Zelten. "From there, it was just a matter of implementation. We had the functionality and structure."
In the final design, only the scanner's base, film carriage, filter wheel, and back-panel were re-used from the Microtek model. And Polaroid engineers have already set their sights on new projects. "We've established a performance level, now we can add some features," says Boyd. "The electronics are flexible and make a viable platform for future products."
'We made it nicer to use'
To allow Polaroid engineers to concentrate solely on the SprintScan's imaging technologies, they contracted IDEO, Lexington, MA, for the industrial design and enclosure engineering.
IDEO designers used SolidDesigner and ME30 software from Hewlett-Packard, as well as Pro/ENGINEER from Parametric Technology, to create a durable, functional enclosure. The enclosure is made of Cycoloy ABS resin from GE Plastics.
"By creating pinch scoops for easier access to the slide, we made it nicer to use," says Industrial Designer Scott Stropkay. Perhaps best of all, the enclosure has a snap-fit door that houses the light source and an extra bulb. The door lets users change the light bulb--a first for desktop scanners. Thanks to molded-in ribs that protect the lamp sockets, there's no risk of electrical shock to the user.
About the Author(s)
You May Also Like