Energy-Aware Industrial Devices
January 24, 2013
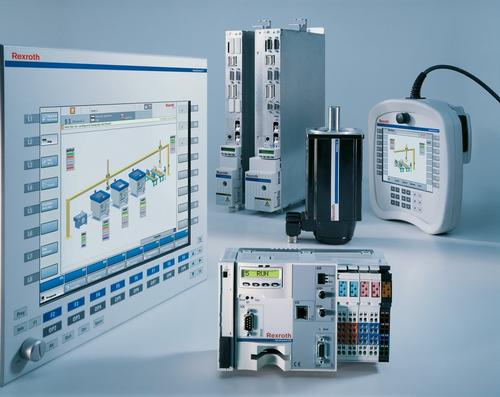
With energy-aware industrial devices coming into the marketplace, manufacturers and OEMs will have an important tool to help reduce energy costs as much as 20-30 percent using intelligent, Ethernet-based networking.
Using open-interface standards such as PROFIenergy, Sercos Energy, and the CIP Energy Object, these new energy-saving strategies could become part of a new normal for manufacturers and machinery builders implementing automation application solutions.
The initial target applications are monitoring and saving energy by placing systems into standby mode during production pauses. And even though the base technology has been ready for a couple of years, application deployment has taken time. But now, with the first wave of open-interface, energy-aware devices coming to market, the pace is increasing as companies explore how to integrate energy priorities into the real-time control loops of automation machinery.
Saving 20-30 percent of energy just by entering standby mode during production pauses offers the potential to save hundreds of thousands of dollars in large automotive plants. In some parts of the world, companies are penalized for having a large carbon footprint, so implementing energy protocols becomes a huge deal if carbon credits are a factor for manufacturers.
Scott Hibbard, vice president of factory automation technology at Bosch Rexroth, told me it had already been putting energy functions into products even before the release of Sercos Energy. But now the process has turned to converting to the open-interface standard for drives, CNCs, and motion controls.
The standardized version for controllers is expected to be in prototype units early this year for customers to try out on their machines. The new controls will use the Sercos Energy information in conjunction with function blocks in PLC programs as part of Rexroth's 4EE energy efficiency program for manufacturing equipment.
Using an IEC-61131 energy efficiency function block to pull in data from Sercos Energy-capable devices, information is presented to the programmer, who can create functions that monitor energy use and/or tune down devices. By performing calculations, the programmer can determine whether to idle a piece of equipment for a specific period to save energy.
About the Author(s)
You May Also Like