Don't Leave Fluid Power Component Selection to Chance
May 8, 2014
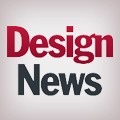
People sometimes come to us after trying to build hydraulic systems by cobbling together spare parts from the back room. They wonder why the system doesn't perform well. We tell them there's a science to constructing optimally performing systems, and they need to plan for their own success.
For example, system designers should use servo-quality valves or proportional valves with linear, zero-overlap spools. They shouldn't use flexible hose between the valve and the cylinder. This is very important, as it could result in difficult tuning and poor control because it lowers the actuator's natural frequency (a lower natural frequency means that the system is "sloppy" and can't move as fast as systems with high natural frequency). Instead, machine builders should mount valves directly on the end or on top of the cylinders, keeping the trapped volume of oil between the valve and the piston as small as possible.
Using valves with zero-overlapped spools allows the system to smoothly transition between opposite control directions. In contrast, when an overlapped (closed-center) spool shifts from one side to another to change direction of the motion, the system will come to a stop with a thud, leading to difficult tuning and poor control around the critical zero point and potentially increased maintenance costs due to shock and vibration. Automated tuning techniques don't work well with valves with dead bands.
Designers should also avoid valves with separate amplifiers unless they are able to set up the amplifier properly. Many valves have onboard electronics and are set up by the factory. There are two reasons for this. The first is that valves with integrated electronics are already set up or tuned for the valve, whereas the standalone electronics, acquired separately, are not. Secondly, the standalone amplifiers can generate a lot of electrical noise that can be induced on feedback signals, making system operation unreliable.
Do not use counter-balance valves. They counteract the motion controller when they're part of the closed loop. If a safety valve is needed to keep a vertical load from falling, machine builders should use a blocking valve between the main control valve and the cylinder. The blocking valve should be closed when the load is to be stopped and opened when the motion is to resume.
— Peter Nachtwey is president of Delta Computer Systems Inc.
Peter Nachtwey has more than 30 years of experience developing hydraulic, pneumatic, electronic and vision systems for industrial applications. He graduated from Oregon State University in 1975 with a BSEE and served in the US Navy until 1980. He became president of Delta Computer Systems, Inc. in 1992. In addition to leading Delta's engineering and R&D programs, he has presented technical papers for IFPE, NFPA, FPDA and various technical conferences.
Related posts:
About the Author(s)
You May Also Like