Buckling structure gives prosthetic foot natural feel
June 12, 1995
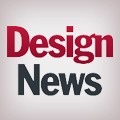
Seattle, WA--If engineers formed a list of commandments, thou shalt not create a structure that buckles would undoubtedly make the top ten. Bill Bryant, an engineer at Model + Instrument Development (MIND), knows this unwritten rule well.
Yet as he studied human gait and applied his findings to the design of a new prosthetic foot, buckling was what he wanted. "A foot should be stiff when flatfooted, for stability," he explains. "But to be comfortable, it should get softer as you roll onto the toes and take no additional load to roll the toe over."
The foot also had to be inexpensive and lightweight, yet strong enough to handle moderately active users weighing as much as 225 lbs. Compared to the company's high-end Seattle Lightfoot, the new Seattle Natural Foot had to cost just one-quarter as much. Charged with meeting these conflicting requirements, Bryant created a new class of injection-molded thermoplastic keel-structures, structures that employ a concept he calls Controlled Elastic Buckling.
Engineering books define buckling as a sudden, large, uncontrolled deformation of a structure due to a slight increase in loading. Controlled Elastic Buckling possesses each of these properties as well, but in moderation. Instead of "sudden, large, and uncontrolled," the Natural-Foot keel buckles in a predictable, moderate, and constrained fashion.
To achieve these qualities, Bryant formed the keel from a series of five curved ribs. As the foot bends, the ribs buckle against each other with the lower ribs progressively supporting the upper ones. Two perpendicular webs-added after empirical testing-interconnect the lowest ribs to provide increased stiffness at the limit of bending. "The secret is supporting (the keel) when it gets to the finished bent shape," he says of the design. "We allow it to buckle, then we don't let it go any further."
After several early attempts failed catastrophically-buckled in the classic sense-Bryant decided to reverse the design process. Instead of creating a keel design and bending it, he began with a keel already bent into the desired six-inch radius and then computed rib cord-lengths that would yield that bend.
Finite-element models created with Structural Research and Analysis' COSMOS/M confirmed the final design. Building the FEA models, however, stretched the capabilities of the software and the knowledge of several experts. "Everyone considers buckling a failure mode," says Bryant. The analysis proved extremely nonlinear. It also contained complex contact problems at the points where the ribs touch each other when bent. By working with Gary Ketner, an outside consultant, he ultimately produced a model that converged. The results correlated within 10% of actual measurements and, most importantly, predicted the fatigue failure location.
In a lab across the street from Bryant's office, engineers spent weeks testing sixteen different injection-moldable polymers in search of one that could handle the high fatigue load. Popular plastics such as nylon survived less than 100 cycles. The winner, pure DuPont Delrin(TM), lasted for millions. "There is nothing in high-load fatigue that even comes close to Delrin," says Bryant. Its low cost also kept the foot's price down.
Delrin, however, presented its own challenge: almost nothing sticks to it. Microcellular urethane foam from BASF injected into spray-metal tooling forms the foot's outer shape. To get the foam to bond to the Delrin, technicians must plasma-etch and prime the keels before molding. The foam also had trouble flowing between the keel-ribs, so cut sheets of urethane now fill these gaps. While these manufacturing headaches initially proved disappointing, engineers found that, by carefully selecting the durometer of the foam sheets, they can fine-tune the force-versus-displacement characteristics of different foot sizes.
The keel's extremely nonlinear character allowed MIND to create just two sizes to cover the full range of feet. The difference in deflection between a 150-lb person and a 200-lb person is small. Ultimate strength is cited as more than 1,300 lbs.
Nothing matches the foot in both price and performance, the company claims. It should prove especially popular in third world countries where cost is extremely important and amputees with a makeshift prosthesis carry quite a stigma.
Bryant envisions many other applications for his controlled-buckling concept and expects other designers will too. "I'm happy that this gives me another engineering tool to work with," he says.
Additional details...Contact Bill Bryant, Model + Instrument Development, 861 Poplar Place South, Seattle, WA 98144.
About the Author(s)
You May Also Like