Apptronik's Apollo robot totes a parts bin.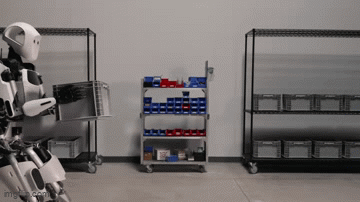
Automotive Engineering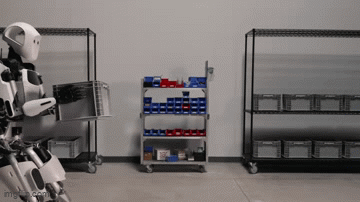
Mercedes Puts Apollo Robot to WorkMercedes Puts Apollo Robot to Work
Will Apptronik’s Apollo humanoid robot have to join the union?
Sign up for the Design News Daily newsletter.
Will Apptronik’s Apollo humanoid robot have to join the union?