Federal Stimulus Boosts Carbon Composite Hopes
October 6, 2010
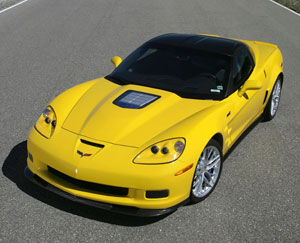
Oak Ridge National Labs (ORNL)in Tennessee is finishing construction of a pilot plant that will be able toproduce up to 25 tons per year of carbon fiber from low-cost lignin and other feedstocks.
Successful startup of the technology could pave the way formuch wider use of carbon-fiber composites in cars, wind turbines and otherindustrial applications.
"Through its investment in the Carbon Fiber TechnologyFacility (CFTF), the federal government is facilitating the commercializationof a full-scale manufacturing process for carbon fiber that is cheap enough tobe purchased by auto and wind turbine companies," says Fred Baker, a scientistin the Materials Science and Technology Div.'s (MSTD) Carbon MaterialsTechnology group.
The U.S. Dept. of Energy last year provided ORNL with $34.7million in American Recovery and Reinvestment Act funding to build the CarbonFiber Technology Facility.
The funding will allow ORNL to consolidate its carbon-fibercomposite research from three scattered buildings.
The ORNL estimates that every 10 percent reduction invehicle weight increases by 5 to 8 percent the miles a vehicle can travel forthe same input of energy. The weight of an engine could be reduced up to 60percent if carbon composites were used extensively in the vehicle.
Widespread use of carbon composites is a game changer forlarge aircraft such as the Boeing Dreamliner787 and the AirbusXWB 350. The enormous benefit of carbon composites in aircraft justifiesthe price of $10 to $20 per pound. Experts feel that widespread use in carswill require prices of carbon fiber to drop to around $5 to $7 per pound.
Use of carbon fibers is limited to high-end cars withpremium prices. One example is the Corvette ZR1, which features carbon-fiberdual-port front fenders, a carbon-fiber raised hood with window and a full-width,body-color carbon-fiber rear spoiler.
PAN and Lignin
The new facility at Oak Ridge will house a conventionalconversion line for producing carbon fiber from low-cost precursors, includingpolyacrylonitrile (PAN), a polymer derived from petroleum, and lignin, which isderived from wood and switchgrass.
The facility will also have a melt spin line that willproduce precursor fibers from raw materials such as lignin from paper mills andfrom biorefineries that separate lignin from cellulose. A biorefinery atVonore, TN will use technologies developed by the Bioenergy Sciences Center atORNL and the University of Tennessee to economically break down cellulose intosugars and ferment them to make cellulosic ethanol fuel.
Feedstocks include switchgrass and wood from hybrid poplartrees.
Melt spinning is a commonly used process to make nylon,polyester and other fibers used in various textile products.
"Melt spinning is cheaper than wet spinning because 100percent of the feedstock materials is converted to fiber as they pass throughthe spinneret," says Cliff Eberle, an engineer in the Polymer Matrix CompositesGroup of ORNL's Materials Science and Technology Div. "In solution spinningused for the PAN process, only about 20 percent of the material passing throughthe spinneret is PAN, with the rest being solvent. Furthermore, recovering thesolvent and complying with environmental regulations make the PAN processcostly."
Baker says that melt spinning can produce a low-cost carbonfiber from lignin. The precursor generally accounts for half the production cost.A highlight of Baker's work was the demonstration that high-purity lignin canbe isolated from the "black liquor" of the paper-making process without anexpensive purification step. The cellulosic ethanol fuel process is a route toeven higher purity lignin.
ORNL is managed by UT-Battelle for the Dept. of Energy.
Photo: The CorvetteZR1 makes extensive use of carbon composites to reduce weight and boostperformance.
Source: General Motors
About the Author(s)
You May Also Like