Eight Ways to Boost Product Reliability
November 23, 2009
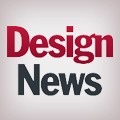
Creating reliable products isn't easy.
If you don't believe that, then consider North American automakers.In the past decade, GM and Chrysler have dedicated themselves to boosting quality.They've hired scores of full-time reliability engineers, many with Ph.D.s. Yetthey've continued to play catch-up with the Japanese.
The trouble is, reliability is a fast-moving, slippery target.In telecommunications design, for example, engineers have to allow for so-called"five nines" uptime, meaning that their equipment must work for all but fiveminutes per year. That even includes those minutes when maintenance workers arereplacing circuit boards. If the engineers don't accomplish that, their productis deemed a failure.
Or consider the dilemma of automotive designers: Their products must run in temperaturesranging from -70F in Barrow, AK to 130F in the Arizona desert. They have to work whiledriving over gravel roads or washboard concrete. Worse, they have to operatereliably, even when they are poorly maintained by owners who seem oblivious totheir requirements. If the engineers don't accomplish that, consumers complain.
The bottom line is that design engineers have to knowfailure modes. They have to conjure up potential ways for users to abuse theirproducts. They have to imagine ways for assemblers to misassemble their parts.
"You hear people say, 'This must be a Friday car,'" notesJake Fisher, senior automotive engineer for ConsumerReports. "Well, if you design it right, it shouldn't matter what day it'sbuilt on. You have to design it so it can only go together one way."
Here, we've collected recommendations from engineers whostudy reliability on a daily basis. We've also culled through some back issuesof Design News and cited somestrategies that have worked for engineering teams in the past. Following are afew of those strategies.
Don't be too anxious to redesign good products. Earlier this year, Ford Motor Co.'s Focus and Fusion vehicles outperformed products from Toyota and Honda in Consumer Reports' evaluations. How? Ford stuck with a model that was already competitive, then concentrated on its processes. The Focus, for example, came out in 2000 and its reliability was poor. Each year, though, it got better. "Ford's not redesigning them as fast as some of the other manufacturers are," Fisher says. "When it comes to reliability, slow and steady often wins the race.
Never assume anything is obvious. What appears to be obvious to a designer may not be so obvious on the factory floor. When designers assume too much, products often get misassembled. "It's hard for designers to imagine that everyone might not be thinking the same way they are," notes Paul Nickelsberg, president and CTO of Orchid Technologies, a consultant that specializes in electronic product design and development. "In actual fact, nothing is simple and obvious on the factory floor. The workers are not mind readers."
Concentrate on perfect systems, not perfect components. After years of studying Japanese car makers, the Center for Automotive Research reached an amazing conclusion a few years ago: If you assume you'll get better quality by demanding excruciatingly tight part tolerances, then you're destined for second-class performance. High reliability, they learned, is dependent on perfect systems, not perfect components. "It's counter-intuitive," says David Cole, the Center's chairman. "It doesn't appear to make rational sense, but if you can build with repeatable, imperfect parts, you can solve a lot of quality problems at the systems level."
Don't pack more functionality into one button just because you can. The beauty - and the curse - of software is that it endows products with many capabilities. But users are often flummoxed by the multitude of features available in a single button or knob. As a result, they sometimes end up complaining that such buttons and knobs don't work properly. "Today's automotive cockpits are sleek looking," Fisher says. "But they've replaced buttons with software, so the user has to go through a bunch of menus. Many consumers don't like that."
Know the appropriate standards. Especially in power systems design, standards are key. "In power electronics, there are standards that have to do with creepage, clearance, component ratings and de-ratings, and minimum distances between parts," Nickelsburg says. "If you follow those, it could lead to other issues you haven't thought of, and it could boost your reliability."
Understand interaction failure modes. Mismatch two perfectly good components and you may create an unreliable system. If, for example, a starter motor lacks the necessary torque to start an engine, it will soon wear out. Why? Because longer cranking wears it out. Similarly, a car's heavy glass window may reduce cabin noise, but it can also wear out the power window motor regulator. The bottom line is that many components work fine by themselves, but they can cause problems if no one considers how they go together.
Track performance of all vendors. It's not good enough to track the performance of your main suppliers, says Cole of the Center for Automotive Research. You should also track your suppliers' suppliers, as well. He recommends that manufacturers keep performance lists of all vendors, from tier-one on down.
Be aware of program timing. One of the biggest causes of poor reliability is missed schedules. Why? Because engineers who fall behind often find they don't have enough time to fix potential problems. Are the dies on time? Are the sub-systems getting validated? Are system assemblies passing internal tests? If you don't know the answers to those questions, reliability will suffer.
Eight Ways to Boost Product Reliability
About the Author(s)
You May Also Like