Dallas Cowboys Unveil 600 Ton Video Board Hoist
December 23, 2009
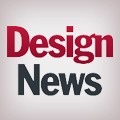
Automation and motion control are playing a pivotal role in raising andlowering the massive video board at the Dallas Cowboys' new stadium. The hoist systemuses 24 cable drums, 80 7.5 HP motors, 40 ABB ACS800 drives and two master/followernetworks to safely lift and position the 600-ton board.
Brad Cobo, ABB's Dallasdistrict regional application engineer for low voltage drives, says the drives onthe video board are split into two groups. Thirty-two hoist drives lift theboard, and eight stay cable drives keep the board from swaying back and forthwhen the end zone doors and retractable roof are opened and create significantair movement in the stadium.
ABB worked on the project with Uni-Systems,the OEM supplier of both the video board hoist and retractable roof withsignificant experience with other stadium roofs in the U.S. including the Arizona Cardinals Stadium, Minute Maid Park in Houston andothers.
The hoist is split into two groups of 16 drives to independently lifteither end of the board and automatically keep the board level. Within eachgroup of drives, one drive serves as the speed master and the other 15 drives operateas torque followers. Cobo says using a master-follower fiber optic networkallows the system to share the load equally between all of the drives. "Thefiber optic cable passes a torque reference from the master to the followerdrives to make sure that each hoist drum lifts its share of the load," he says.
The stay cable drives all operate in torque control mode to create andhold a specified amount of tension on the stay cables as the board moves up anddown. The Siemens PLC in the system uses Profibus networking to provide each ofthe drives the same torque reference.
Cobo says the biggest challenge with the project proved to be the PLCprogramming done by Alex Krueger of Uni-Systems, and making sure that everydrive is ready before the final command is given to release the brakes. Strictsequencing controls in the software guarantee that each drive is ready beforereleasing the brakes. To properly operate the hoist drives, the software sets alow speed reference of just a few hertz which causes the drives to buildtorque.
Because actual torque values are being communicated back to the PLC, theprogram can confirm that the hoist drives are generating torque beforereleasing the brakes and increasing the speed reference. At this point,everything is moving and the system continuously monitors all speeds and torquesto see if anything is out of range. If any one part of the system shouldmalfunction or do something unexpected, it automatically shuts down and setsthe brakes.
"The sequencing algorithms make the system safe and proved to be the mostdifficult part of the project," says Cobo.
One of the reasons Uni-Systems selected ABB for this project is thedirect torque control feature of the ACS800 drives. Direct torque control (DTC)enables a high level of motor performance without using encoder feedback,similar to the way a vector drive maintains a motor model or mathematicalsimulation of motor operation. The motor model in the ACS800 drives that updatesat 40,000/sec allows the system to compensate very quickly for changes in loadtorque.
Additional drives control the stadium's retractable roof that consistsof two panels, one on each side, that weigh about 1.68 million lb each andtravel 215 ft on what is essentially railroad tracks. Cobo says the roof canopen and close in just under 12 minutes. Each panel uses 64 7.5HP motors togenerate about 800,000 lb of pulling force and move the panels up the 24 degreeincline.
The motors are powered by ABB ACS800-U11 line regen drives, and a totalof 32 motors driven by eight separate drives on each side of the panel. The lineregen drives allow regenerative braking energy to be fed back to the utilityinstead of being wasted as heat through traditional dynamic braking resistors.The cost of the energy being regenerated is actually small, compared to thesavings from not having to purchase and install brake resistors.
The drives are connected together using Profibus and a fiber-optic networkarchitecture to form a master/follower system similar to the hoist. The masterdrive receives a speed setpoint from the PLC, and the other seven drives get atorque setpoint from the master.
Cobo says this approach allows all of the drives run at the same torqueand share the load equally. To open or close the roof, the PLC sends the speedsignal and start command to each master. Progress is monitored and, if eitherside of the panel gets ahead of the other by more than 0.25 inch, the leadingside is commanded to slow down. Direct torquecontrol allows the system to operate open loop, eliminating additional wiringand the cost of encoders on the motors.
Dallas Cowboya euro (TM)s Unveil 600 Ton Video Board Hoist A

Dallas Cowboya euro (TM)s Unveil 600 Ton Video Board Hoist B
About the Author(s)
You May Also Like