Molded circuits shrink electronics
November 6, 2000
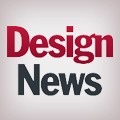
Whoever said, "don't sweat the little stuff" clearly had nothing to do with electronics design, where the tiniest components often cause the biggest engineering headaches. "Miniaturization goes hand in hand with all sorts of packaging and assembly difficulties," explains Bruce Dewart, engineering manager for electronics manufacturer UFE Inc. (Stillwater, MN). To avoid these shortcomings of smallness, telecommunications devices and consumer electronics increasingly employ molded interconnect devices (MIDs), which integrate electrical and mechanical functions in a single injection-molded part.
MIDs have been around for more than a decade, but in the past they had a tough time competing with printed circuit boards-which can cost 50 times less than MIDs on a square-foot basis. With miniaturization, though, "MIDs can deliver a lower systems cost by facilitating parts consolidation," Dewart maintains, noting that one part with integrated functions often costs less than the collection of parts they replace. What's more, fewer parts can cut assembly costs too. "Instead of fancy assembly robots, we let the molding machine assemble the part," says George Shevchuk, a researcher at Bell Laboratories who helps Lucent Technologies (Murray Hill, NJ) create micromolded electronic components. Finally, MIDs go right to the heart of miniaturization because they free up real estate for packaging-not just through parts consolidation but also through their ability to conform to available spaces.
Lucent's new molded circuit (inset) forms a PIN sled that sits at the boundary of the transceiver's electronic and optic components. |
For one of the best examples of what a molded circuit can do, look inside Lucent's latest fiber-optic transceiver-a telecommunications device that converts digital optical signals to electronic ones and vice versa. The device contains a new "PIN sled," an MID whose milliamp, two-layer flexible circuitry has been insert molded into a plastic part that serves as a mounting package for both the transceiver's photodiode receiver and a mating optical connector. "The part resides at the boundary between optics and electronics," Shevchuk notes. Manufactured by UFE, this molded circuit not only embodies design features common to all good MID applications (see sidebar) but also represents several technical firsts-in terms of its size, geometry, and a new flexible circuit material. "It is definitely on the cutting edge of MID technology," Dewart says.
Size-wise. Measuring just 0.080x0.180x0.307 inch, this MID features a trace width, or spacing between conductors, of just 0.007 inch. "It's the smallest one we've ever done and one of the smallest in the world," says Karl Maurer, a UFE materials engineer who worked on the project. It's so small, in fact, that Maurer describes its size as little more than "one plastic pellet per part."
Size isn't the only thing that sets this MID apart. Unlike conventional MIDs, where molded plastic forms a rigid backing for all of the circuitry, the Lucent molded circuit features a "circuit tail" that extends 0.407 inch past the edge of the plastic part and helped Lucent solve some packaging problems in its 0.5x2x0.25-inch transceiver. Maurer explains that this tail spans a barrier created by a set of electrical leads inside the transceiver. "The tail jumps over the leads to make the device more compact," he says. Without the tail, Lucent would have needed a space-consuming flat cable to bridge the leads. "This design is really a component integration of the cable into the part," Maurer points out.
Component integration aided the assembly process too-and not just because it resulted in fewer parts to handle. Shevchuk observes that integration "bypasses the stack-up of alignment tolerances" that could otherwise affect micro-sized assemblies. Moreover, this MID has integrated features added for the sake of automated assembly. The MID circuitry, for instance, ends in a series of "fingers" that connect the photodiode receiver through an automated soldering process.
UFE uses a multi-step process to transform plastic film into a 3D electronic circuit that plays a mechanical role, too. |
Tough to mold.
While leaving some of the MID circuitry free of plastic might seem straightforward, this design did present some tooling challenges. Explaining that the mold steel shuts off on the circuit itself, Maurer describes the tooling tolerances as "very exact" to ensure that the circuitry would neither be crushed or lead to flash. Maurer notes that the shut-off clearances are in the neighborhood of plus or minus 0.001 inch-or about half the usual tolerances in MID tools.
Molding this tiny part, which weighs only about 60 mg, also required a careful material selection. Maurer helped Lucent pick a glass- and mineral-filled Ticona PPS to some extent because it flows well. "I knew I could fill the part with it," he says. But more than that, the material had to be strong and dimensionally stable to hold up to relatively high forces and temperatures of the automated assembly process that Lucent came up with for these transceivers. Maurer notes that the assembly includes a wire bonding process that subjects the MID's 0.020-inch walls to forces up to two lbs at temperatures of 400F. And Shevchuk adds that all the automated assembly requires precise component location, so the consistently low shrink of the PPS was also important. "Thermal stability of the molded part was critical," he says.
Whatever the difficulties making this tiny part, this is one MID that has paid off. Maurer estimates that it takes up only about half the real estate of conventional circuitry and an equivalent mounting package. And he reports that this MID's circuit tail and overall compatibility with automated assembly methods cut costs nearly in half compared to conventional circuitry. "It's unusual in electronics to reduce the size and cost at the same time," Maurer says. "This molded circuit does both."
Technical firsts
Lucent's PIN-sled MID embodies several technical advances, says UFE's Bruce Dewart. Here's a glance at the technical "firsts" for UFE and Lucent:
It's smaller than ever. With trace width of 0.007 inch and dimensions of 0.307x0.181x0.080 inch, this circuit is the smallest to date using UFE's molded circuit technology and one of smallest using any MID process.
It has a 'tail.' The device's circuitry extends past the plastic part edge, eliminating the need for a flexible cable.
It has a new material. The device represents both companies' first use of a new PI/PET flexible circuit material.
About the Author(s)
You May Also Like