Electrically Conductive Pastes Are Gaining Traction
May 6, 2014
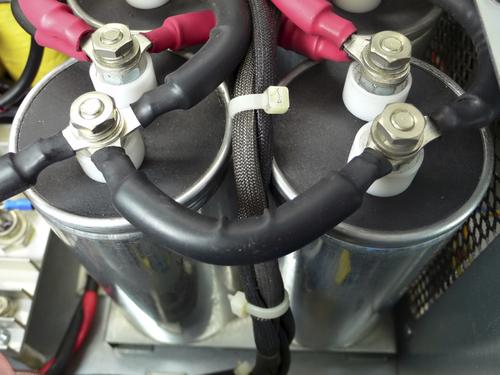
Open the hood of your car, and look at the battery (if you can find it -- it's difficult on some new models). You might see that nasty white or bluish powder around one of the terminals, caused by corrosion. You shut the hood and don't think much about it because things seem to work fine, and the car still starts. Occasionally, a meticulous car owner or mechanic will scrub the crud off with a wire brush and apply some petroleum jelly to the clean joint.
Such remedial measures help, but you have to think there's a better way to treat electrical connections like this. It turns out there is. The millions of connections that populate myriad types of equipment in the world stand to benefit from a substance known as electrically conductive paste. Improving connections results in reduced downtime and maintenance, and extends the life of connections and equipment. Safety and efficiency improve, as well.
We owe the creation of electrically conductive paste largely to John Ebbinghaus, a native of New Rochelle, NY, who graduated from Clarkson College of Technology (now Clarkson University) with a Bachelor of Mechanical Engineering (BME) degree. "I consider myself an electromechanical engineer because I've worked on a lot of electronics -- heat exchange, connections, and materials, and what have you?" he said.
In 1973, Ebbinghaus was working at Litton Guidance & Control Systems near Los Angeles when they assigned him a problem to solve. Litton made guidance systems for fighter, transport, and surveillance aircraft such as F-14, E-2C, and S-3 deployed from aircraft carriers. They also made test equipment for the guidance systems. They hooked these to the ship's power system in a maintenance room, and the connections rusted due to the salty air. This reduced the input voltage from 120V to 84V, increasing current and burning up connections. "It was destroying these guidance systems, which cost $300,000 a pop," he recalls. He came up with a paste with metal particles in it that solved the problem by penetrating the corrosion.
But when he submitted his idea to Litton's patent department, Ebbinghaus got turned down because the company didn't want to get into that kind of business. As he recalls, "They released it to me. It was spare change to them. Because I had a heavy workload, I didn't really pursue it." Over ensuing years, Ebbinghaus occasionally dabbled with his invention, working on the side to package and sell it, and developing half a dozen formulas between 1973 and 2010.
Most of that came after Ebbinghaus retired in 1989 and he found the time he needed to flesh out his concept. With his daughter, Lisa Rinaldo, he has started a company called Prohm-tect USA in Sioux Falls, S.D., to manufacture and sell electrically conductive pastes. With no patent protection obstacles to overcome, many competitors also produce it, including companies in the US and about 150 chemical companies in China. Most pastes are silicon-based.
Electrically conductive paste is designed to work on new and existing bolted, clamped, plug-in, and crimped electrical connections, and to protect those connections in corrosive environments. The pastes consist of minute micro-sharp conductive metal particles suspended in oil, providing multiple pathways for electrical current in a connection. They fall into two broad categories, one using silver particles and the other a special stainless-steel alloy. Several types of stainless-steel pastes are available with varying sizes and amounts of metal particles, suitable for different applications. The formulas come in a variety of sizes ranging from 1-cc syringes to 300-cc caulking tubes.
Both formulas of paste perform several functions in protecting electrical connections. They block out moisture, prevent corrosion from causing a reduction in conductivity, and improve the conductivity of the mated parts. Perhaps most importantly, the paste physically cuts through any corrosion, and the grease keeps the corrosives away from the connection. It protects the connection so the corrosives can't wick into the connection and eventually destroy it or lower the voltage to a point where it causes damage.
About the Author(s)
You May Also Like