Display Week takes place May 12 through 18.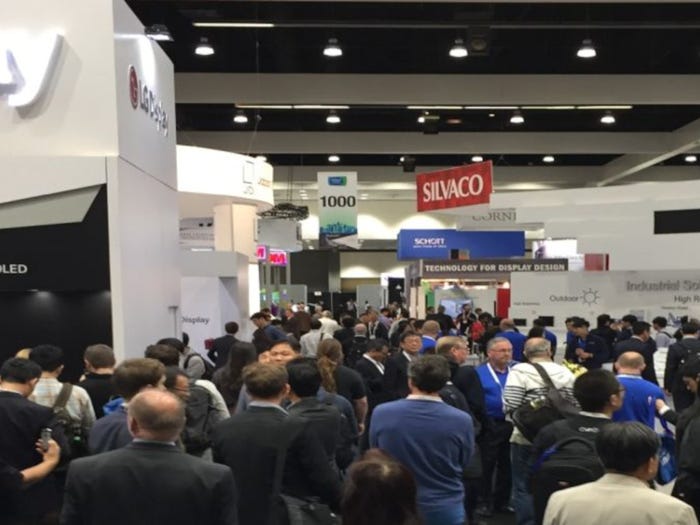
Electronics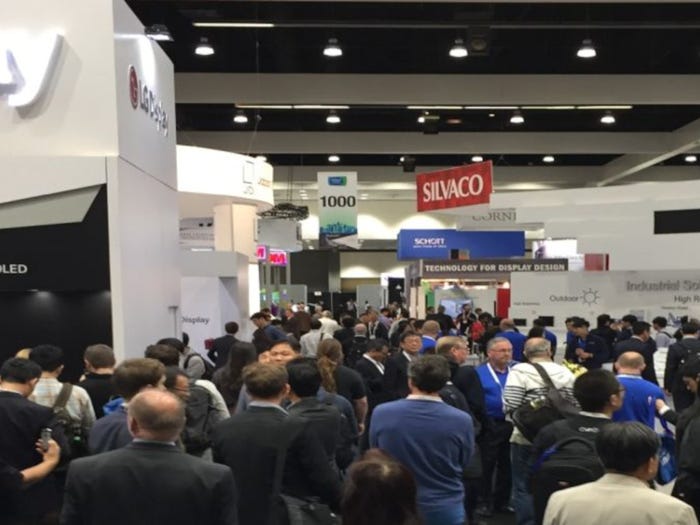
Display Week a Treat for Visual SensesDisplay Week a Treat for Visual Senses
Whether physical or virtual reality, display technology to dazzle in San Jose.
Sign up for the Design News Daily newsletter.