Small aircraft take flight with CAD
August 17, 1998
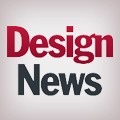
Redmond, OR--Aluminum planes, move over. Make way for lighter, composite-material aircraft, particularly the first production Lancair airplane, the Columbia 300.
Known for his Lancair kitplanes, Lance Neibauer, owner of Neico Aviation, decided the time was right for a fresh small aircraft design. He founded Pacific Aviation Composites to design, build, and market a production version of the kitplane, Lancair ES--a four-seat, fixed-gear aircraft especially for the recreational pilot.
Only requirement: engineers must design the plane with the same appearance as the rest of the Lancair line, a streamlined, dolphin-like shape with all curves and no corners.
Greg Cole, chief engineer of research and development, initiated a three-fold program: simplify the aircraft, manufacturing process, the engineering and design phase. As everything always begins at the "drawing board," the company looked for a versatile CAD software program with the ability to run well on a network of 15 PC-based stations. They chose CADKEY from Baystate Technologies (Marlborough, MA).
John Sutherland, network administrator and project engineer says, "CADKEY is easy enough to use to throw at someone who is fairly green. It has a short learning curve, and that is a truly big asset in our project, as we are crunched for time."
Cole used CADKEY's 2D wireframe feature to create the wide sweeping curves and airfoils of the aircraft.
The epoxy pre-impregnated carbon fiber and fiberglass material proposed for the body of the plane allowed Cole to work with aerodynamic shapes rarely considered in light airplanes. The flexible composite can seamlessly be formed to almost any shape and still withstand high stress.
Conventional planes are made from aluminum, with one wing requiring up to 15 sheets. The Columbia 300 requires only one seamless layer of composite material. The new aircraft wings feature dual, redundant spars, a single bottom piece to go from wingtip to wingtip, and two top wing pieces for each side. The ability to shape and taper the composite material's thickness as well as being able to add stiffening technology like honeycombing and fiberglass cloth, produce a wing that is stronger, lighter, and simpler to manufacture and maintain. The lack of seams and the microscopic smoothness of composite material also mean the aircraft takes advantage of laminar flow, reducing drag.
"Because of the composite material's construction, how stress is received and absorbed can be controlled and redirected. The hardest challenge facing designers of the composite-material aircraft was dispensing static electricity and with standing lightning strikes, a requirement of the FAA (Federal Aviation Administration). For this a wire mesh runs through the plane's shell so static electricity will bleed off the trailing edges.
When Sutherland received Cole's drawings, he converted the 2D drawing to 3D models and began dividing the wings into large pieces. He played with different ideas to make the wings fit together. Using CADKEY as a back-of-the-envelope, he says, "I used it as a brainstorming tool and came up with new ideas. Then I refined the idea, transferred it, and took it to final design without having to duplicate any information."
After part design, the drafting engineers drew the completed model and its component details in 3D, and let the software convert the models to 2D drawings. This information was submitted to the Federal Aviation Administration for review.
The Columbia 300 flies at 220 mph in cruising flight. It will sell for $205,000 with a standard instrument-flight package. Twenty Columbia 300s are expected to fly by the end of 1998, and more than 100 by the end of 1999.
About the Author(s)
You May Also Like