FEA software helps astronauts train
September 7, 1998
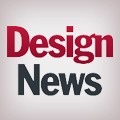
Pittsburgh--Around the turn of the century, a crew of three will begin living on the International Space Station (ISS). When complete, seven astronauts and scientists will inhabit the station at any one time. To prepare for maneuvers in space, potential crew members are training in a module at the Neutral Buoyancy Laboratory (Clear Lake, TX). Astronauts use the lab, essentially a large pool, to practice outside space-station drills and help with logistical planning.
While the training module replicates the dimensional and functional parameters of the ISS, there are differences due to its aquatic environment. Design engineers used stainless steel for the training components instead of the aluminum alloys used for the space station. The module also had to withstand the stress of support systems both in and out of the pool, such as the lifting system and buoyancy.
Mark Gray and Kim Wong, engineers at Bergaila Engineering Services (Houston) helped design the 7-A airlock where trainees emerge from the water. They built a 37,000-plate/shell element model of the airlock based on the ISS design. Using the finite element model-building tool, Superdraw III, from Algor Inc., Gray and Wong analyzed the best placement of lift points for hoisting the airlock in and out of the water.
From the Superdraw III results, they found that the original lift points needed to be changed to reduce the high stress levels and associated deflection. They also discovered that many of the bolted connections in the space station could be welded for the stainless-steel training module. Mechanical fastening methods, such as bolting, are favored for space station flight hardware because the aluminum alloys weaken when welded. However, welding is a better option for submerged stainless steel.
"The latest version of Superdraw III made the process of building models faster and easier," says Gray. The most recent release of Superdraw III offers dynamic rotation, zoom, and pan tools for display; a shaded rendering feature; and a set of keystroke tutorials.
Training is expected to begin the end of summer.
Meanwhile, inside the space station. Ross Bozeman, engineering manager at Bergaila Engineering Services, used Algor's software to design and analyze a potential flight hardware component for the ISS. The aluminum re-supply storage platform (RSP) had to weigh less than 150 lb and support up to 500 lb of equipment. Plus, the structure's natural frequencies had to fall within a defined window.
Bozeman designed a combined beam and plate/shell model of the RSP in Superdraw III according to NASA's specifications. "The updates to Superdraw III over the past year strike me as very intuitive, especially for new users," he says.
For each design, Bozeman conducted a series of 20 linear stress and vibration analyses. He automated the process using batch files. Dozens of design variations were analyzed to determine the best three or four designs.
He also conducted linear dynamic response analyses on other existing flight hardware components. The results of the analyses help engineers determine the net effects of launch- and crew-induced vibrations.
Bozeman appreciates Algor's graphic capabilities. "The graphical representation of results in Algor has always been superior," he says .
About the Author(s)
You May Also Like