Volt Battery May Be Poised for Success
September 21, 2010
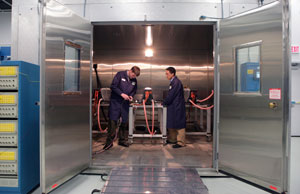
Despite a compressed, three-year window to develop and testthe lithium-ion battery pack for Chevy's new Volt electric vehicle, experts saythere's a good chance the technology will prove to be durable and dependablewhen it hits the streets later this year.
"We don'tknow definitively what the failure mechanisms will be for this battery," saysDavid Swan, CEO and founder of DHS Engineeringand a well-known expert in electric vehicle testing. "But chances are thatGeneral Motors will be right. They can't afford to fail."
Indeed,GM's reputation is on the line with the Volt. Said to be the biggest program inthe company's 102-year history, the Volt serves as an opportunity for GM tomake up for the media-generated black eye it received after the infamousshelving of its earlier electric vehicle, the EV1. It also gives the company achance to take the lead in the hottest new area of the automotive industry.
That's whyGM stepped boldly forth in July of this year, announcing that it will offer aneight-year, 100,000-mile warranty for the Volt's lithium-ion battery pack.
"We offeredthat warranty because our confidence (in the battery) has increasedsignificantly," says Rob Peterson, a spokesman for GM. "What our engineersaccomplished over a short period of time - when you take into account thebatteries, suppliers, electronic controls, manufacturing and dealer training -is really impressive."
Navigating ParallelPaths
For engineers, the Volt program has also been a genuinestomach churner. When General Motors announced the program schedule for itsChevy Volt electric vehicle early in 2007, the timing appeared to be next toimpossible. In a scant three-and-a-half years, the technical staff faced theprospect of studying a new material, building prototypes, working withsuppliers, understanding failure modes and then squeezing years of simulatedlife into a few months of battery testing - all while the car itself was stillbeing constructed.
"In the past, innovation and invention wasdone before the technology was assigned to a vehicle," Peterson says. "This wasdifferent. Here, we decided to do the innovation and invention on a parallelpath with the vehicle development."
From an engineering perspective,the short development time raised questions, particularly where the battery wasconcerned. Some wondered if two years of testing on the Volt battery wouldprovide an accurate snapshot of its capabilities under real-world conditions.Others asked if General Motors' engineering team could feel confident that theyhad correctly identified the most likely failure mechanisms for the battery.
"The danger with a new technologyis that maybe you're testing it the old way - the way that mattered for previousgenerations of products," says Steven Eppinger, a professor of managementscience and innovation at Massachusetts Institute of Technology. "But you'renot always aware of the failure modes for the new technology. It might fail ina different way. That's always the danger of innovation."
Surprisingly, experts say that thecompressed test period isn't a big issue. The vast majority of engineeredproducts are subjected to accelerated life tests. "In most products, the kindof (testing) cycle you want to put it through can be accelerated," Eppingersays. "If it's charging or discharging, heating or cooling, loading orunloading, it can be accelerated."
Indeed, accelerated tests for a 10-yearlife can be completed quickly, once the failure modes are determined. The key, expertssay, is to determine which tests are right. In batteries, charge/dischargecycles are often the key, and those can be done relatively quickly. "I can getthe amp-hours in and out, and I can easily simulate 10 years in less than ayear," Swan says. "If I know that the degradation mechanism is associated withtime and temperature, I can choose the right driving cycle and I can do thosetests at elevated temperatures. If nothing else, it will give me the warm,fuzzy feeling that I'm getting the number of years I want out of the battery."
Experts say that GM has made a mammotheffort to discover the failure mechanisms and test for them under all possibleconditions. The giant automaker has invested $8 million to double the size ofwhat already was "the largest and most technically advanced battery lab in theU.S." Located at the company's Warren, MI, campus, the lab spans 63,000 sq ftand houses a growing team of approximately 1,000 engineers. It's also equippedwith 176 test channels, 42 thermal chambers, shaker tables for structuralintegrity testing, a battery tear-down area and an integrated test automationsystem.
GM engineers have also tested outsidethe lab. "We've put over a million miles on the real-world vehicles," Petersonsays. "We've taken them to Pikes Peak, Death Valley, the mountains of California, the streetsof LA, and everything in between."
Through countless iterations, thecompany's engineers have also made important decisions regarding the battery'sdesign. As a result of intense scrutiny of the battery's cooling characteristics,GM engineers chose a 5 x 8-inch prismatic cell configuration, instead of thewound, cylindrical design employed in mobile electronics (and in the TeslaRoadster). They also departed from the cobalt oxide cell chemistries commonlyemployed in consumer devices, and then added a hot and cold liquid coolingsystem to the pack, which consists of 288 cells.
"They busted their butts trying toget this battery ready," Peterson says.
Learning from Failure
To be sure, all of those efforts aren't assurances. HondaMotor Co. recently experienced the unexpected when its CivicHybrid batteries started to deteriorate prematurely. The company was forcedto mail more than 100,000 letters to owners of 2006, 2007 and 2008 Civicswarning that their batteries "may deteriorate and eventually fail." Honda nowfaces the possibility of replacing thousands of the batteries, which are undereight- or 10-year warranties and may cost as much as $3,000 apiece, accordingto the Chicago Tribune.
Still,experts say such problems can't be attributed to lack of test time. "When the2001 Prius became available, there was no way the engineers had 10 years oreven five years of data on the battery," Swan says. "Yet they went into highproduction and, by and large, it's been a very successful battery."
The key isto understand the physics and failure modes of the battery and then test theproducts in every conceivable way, says Eppinger. "That's what you really wantto do," he says. "You want to experience all the failures in the lab, so theproduct is robust in the field."
About the Author(s)
You May Also Like