The Case of the Compromised Compensator
November 20, 2006
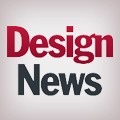
An attorney called to tell me of a truck-car collision that killed a young mother, but miraculously spared her baby who was secured in a baby seat. The tractor-trailer driver was relatively unhurt. My client, who represented the truck leasing company, said that mother and baby had been abandoned by the baby's father almost a year prior to the accident. The baby's father now callously came forward to claim paternity and to file a suit against the truck leasing company, the truck builder and manufacturers of brakes, steering and other components.
The Scene of the Crime
At a central-states dealer facility where the relatively new tractor and the trailer were sequestered, I met my client/attorney and a brake expert I retained to help in my investigation. Driver and witness statements said the truck was on a four-lane thoroughfare approaching an intersection as a traffic light changed to red. While quickly and strongly applying tractor and trailer brakes, the rig suddenly veered into the left lane and ran up and over the young mother's car that had stopped for the red light. The violence of the crash destroyed the car, but also crushed the tractor's metal and plastic front end, snapped half-inch thick leaf springs and caused other major damage.
The Investigation
Sifting through the broken parts, I found the steering box shaft - on which the steering arm was retained - had snapped in two. I didn't see evidence of a fatigue failure, nor did I see any flaws that might have triggered a break. The break appeared to be an overload break. With everyone's consent, the steering gear manufacturer removed the broken shaft for metallurgical analysis to determine if the snapped shaft was the cause or an effect of the crash. I then checked other steering and suspension components, all of which appeared to be OK. Shifting attention to the braking system, we used an air compressor to pressurize the trailer and tractor brake systems.
The trailer brakes worked correctly so we moved on to the tractor. We checked the dashboard valves, foot-operated valve and air lines that snaked through the tractor. All appeared to function correctly. The brakes on the tandem rear axle checked out OK, so we moved on to the front axle brakes. Now, some trucks have an air-over-hydraulic brake booster that uses an air diaphragm to apply force to a hydraulic master cylinder. However, in this case, both trailer and tractor used straight air-operated drum brakes. Each brake utilized a diaphragm-type actuator with a connecting rod that applied force to a "slack adjuster" lever to rotate an S-shaped cam that forced the two brake shoes apart against the inside surface of each brake drum. There, friction converted the rotating energy to heat to stop the vehicle.
The Smoking Gun
The slack adjuster compensates for friction lining wear. As brake shoes wear, the adjusters maintain constant brake shoe-to-drum clearance so that brake diaphragm stroke is not wasted in just moving the brake shoes out to the drum. As with the rig's other brakes, we measured the stroke of the brake connecting rod. The stroke of the right front brake was much more than that of the other brakes. We again aired up the right front brake and observed a gap between the brake shoes and the inside of the brake drum. When we pulled the brake drum we were not surprised to see powder rust on the untouched friction surface inside the drum. Close examination revealed a mashed thread on a link in the slack adjuster. This allowed the pressurized diaphragm to extend fully with no contact between brake shoes and brake drum.
About the Author(s)
You May Also Like