Old Meets New in Bathroom Faucet
April 21, 2003
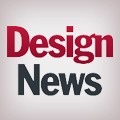
At first glance, the new Standard Collection faucet appears to be one of those new products that spurns the cold, high-tech world in favor of the warm and fuzzy look and feel of a bygone era.
Dripless Design: American Standard's Widespread Lavatory Faucet employes ceramic disk valves beneath each handle. |
The faucet, which resurrects the design of a 1920s predecessor known as the York Combination Lavatory Faucet, features soft contours, lever-type handles, and liberal use of feel-good materials, such as porcelain and cast brass.
Underneath that 1920s skin, however, there's a higher tech story. In bringing the old design forward, designers and engineers at American Standard (www.americanstandard.com, Piscataway, NJ), had to deal with a sinkful of technical issues as they updated the technology from the good ol' days of the 1920s.
To meet today's needs, engineers at American Standard had to adopt materials, finishes, and mechanical configurations that weren't available 80 years ago. The company's director of industrial design, Gary Uhl, did that by plucking research and development from the 1960s and then blending it with modern day methodologies and 1920s styling. A key issue was the matter of valve leakage, a chronic problem 80 years ago, which Uhl addressed by incorporating a technology co-developed by his father, engineer John Uhl, during a period from 1964-1967.
"The notion that we were just going to reproduce a product from the 1920s wasn't true," says Gary Uhl. "Our challenge was to find the things that people liked and bring them forward in a way that would meet modern-day needs."
He says the company conjured up the idea of a throwback design after listening to stories of enthusiasts who plumbed the depths of junkyards to find old sinks and fixtures.
"People kept talking about the great old stuff we used to make," Uhl notes. "We kept hearing about people who had fond memories of old plumbing, and how they'd go to almost any measures to revive it."
Back to the Future
The phenomenon, which is also commonplace among automotive enthusiasts, is an understandable one, Uhl says, especially among people who have fond memories of childhood. "The notion of a different time has appeal," he says. "The feeling in the world today is one of angst, and people want to get away from that."
American Standard executives responded to that customer desire by looking back at the company's catalogs from the 1920s, a time prior to the company's merger with American Radiator and prior to it being subsequently renamed American Standard. In the old catalogs, they found a collection of products-faucets, sinks, toilets, and accessories-that matched the look and feel they sought in a new line.
Unfortunately, the company's designers and engineers also learned why such products no longer existed. "The reality is that much of that plumbing should have been torn out of sinks," Uhl says. "There were good reasons why it was no longer being used. It didn't meet today's codes, didn't have today's safety or performance, and didn't have today's ergonomics."
Retro: The design for the new faucet was based on a product from the company's 1922 catalog. |
Indeed, for all the warmth and softness of the old design, there were problems. Nickel finishes used on the old hardware tended to rub off on wet hands. Porcelain cracked and left jagged, dangerous edges. Flow spouts were stubby and low, failing to meet today's performance demands. Brass parts of the time had high lead content and came up woefully short of today's code requirements.
Worst of all, in the user's minds, faucets of the time were prone to a maddening drip, drip, drip that caused strong-handed users to crank the handles down tighter, which eventually ruined the valve seats. The result: Replacement of faucet valves was commonplace.
"You simply couldn't sell a faucet like that today," Uhl says. "It wouldn't meet codes and it would require too much care and maintenance."
To deal with that, Uhl turned to the ceramic disk valve technology pioneered by his father during the 1960s. The technology, which uses overlapping ceramic disks to shut off or allow flow of water, had always been regarded as a technical success, but had been more notable for its lukewarm acceptance by 1960's U.S. consumers, most of whom were unwilling to pay the few extra dollars, or possibly were distrustful of the grandiose claim that it would never have to be replaced. Ironically, however, the design had been kept alive by European and Asian consumers, who were enthralled by the valve's no-leak, no-replacement performance.
"As it turned out, the ceramic disk valve was an incredible invention for the time because it never wears out and never has to be replaced," Uhl says. "But it was one of those situations where a huge breakthrough in technology just didn't take off in the market."
Family Affair
American Standard, however, had never been short-sighted about the senior Uhl's development and engineering efforts. The company had built ceramic disk valve cartridges in Kentucky in the 1970s and shipped them to a sister company in Europe, Ideal Standard, which sold them in that market.
Moreover, no one knew the value of the technology better than Uhl, who had grown up with it. Uhl, who has four brothers who are engineers, was immersed in American Standard's culture during his youth. On Saturday mornings during the 1960s, while other kids watched cartoons, Uhl often accompanied his father at the firm's seven-story research and development facility in Louisville, KY, and watched as engineers tested faucets equipped with ceramic disk valves.
"As a kid, I used to see rows and rows of those faucets set up in the lab, going through maybe half a million cycles each," he recalls.
As it turned out, much of the research work done during the '60s formed the basis for the company's current valve designs. The valve, which drew its inspiration from the stopcocks on wine casks, requires only a quarter-turn of the handle to be fully opened or fully closed.
The current version uses two ceramic disks, each measuring about a half-inch in diameter. When the user handle is turned one way, holes in the disks align with one another, allowing water to flow through. Turned the other way, the disks block the flow of water.
The key to the design is the hardness of the ceramic. To harden them, American Standard employs a powder metal using a proprietary blend consisting of 94% aluminum oxide and 6% additives. Disks are pressed in a mold, onto which anywhere from 6 to 55 tons of force is applied. The company makes up to 2,000 disks per hour in this fashion, then moves them to a kiln, where the fragile products can be hardened. By firing the kiln to a top temperature of 2,700F, American Standard engineers can then "bake" the ceramic disks in a three-step process that involves 12 hours of preheating, three hours of high-temperature firing, and nine additional hours of cooling. When the disks leave the furnace, they are said to be of "near-diamond" hardness (about 1,200 Vickers).
American Standard then polishes the disks with a diamond paste, ultimately achieving flatness with a surface quality of 0.02 microns. Thickness is measured optically, using a laser measuring device. Much of the technology was developed in-house by American Standard, which had its own ceramics group. Other parts of it were gleaned through consulting efforts with Coorstek, a manufacturer of technical ceramics for a variety of high-tech applications.
By making the disks so exceptionally hard, the senior Uhl says he was able to endow the valve with long life and no-leak performance. Any potential softness in the material, he says, would have led to scratches if the disks were subjected to sand or other hard debris in the water.
"We had to make sure that if the valve was used in Texas or Florida, where sand sometimes gets in the pipelines, it still wouldn't leak," recalls John Uhl, the now-retired manager of product engineering for American Standard. "So we repeatedly simulated it in the lab, and we learned that if a grain of sand got trapped in there, these ceramic disks would chop it off."
Flatness: A Big Advantage
Uhl claims that the disks are so flat that, during operation, they exhibit a performance phenomenon similar to magnetism: The smooth surfaces of the two disks are held together by atmospheric pressure, thus preventing flow of water through the valve.
The technology is considered so reliable that it's also being used by a separate division of American Standard for hydraulic valves in the antilock braking systems of large trucks.
Most important, however, the ceramic disk valve recently took its place in American Standard's "Standard Collection" of products, all of which are based on the original 1920s design. The company's engineering team, including engineers Jose Leyva, Tony D'Amato, Marin Marinov, Mike Carideo, and Walter Pitsch, worked with Gary Uhl and product director Michele Hudec to incorporate the technology in the new faucet. Known as the Widespread Lavatory Faucet, the new product joins an old-fashioned pedestal sink and elongated toilet, two other products in the line that blend the 1920s design with new technologies.
To enable the new faucet to meet today's performance specifications and codes, engineers also used a plasma-vapor-deposited nickel finish that doesn't rub off, and employed code-compliant brass and porcelain materials in the parts.
With this new line of products, "We had to go back to the 1920s to give people want they want," notes Gary Uhl. "So it has the soft feel that they're looking for, but at the same time, it has the performance that they need."
About the Author(s)
You May Also Like