Rotational molding enables minivan wheelchair access
April 17, 2000
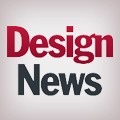
Winimac, IN -Converting a van for handicapped accessibility is no easy task. Most vans are made with floor humps that prevent easy access for wheelchairs. And automakers can't remove the floor humps without taking on an expensive redesign of the fuel system and tanks.
Yet when Braun Corp. recently rolled out a new line of handicapped accessible minivans, the floor humps were gone-without a lot of cost for buyers. The reason: Braun employed rotationally molded plastic gas tanks that eliminated the humps for minimal cost.
The new fuel tanks will be placed on about 1,500 wheelchair-accessible Plymouth Voyagers and Dodge Caravans converted by Braun.
The rotationally molded tanks were supplied by Meese Orbitron Dunne (Astubula, OH). The plastic tanks served as a replacement for the conventional metal tanks provided by the automaker, which were too big and created a large hump beneath the rear seat. Braun considered using a smaller metal tank as a means of lowering the floor, but decided against it because of the possibility of leaks and spills from the joints, seals, solders, and welds. Metal tanks were also too expensive.
Braun also considered employing blow-molded plastic, but ran into another problem: The tooling for blow-molding would cost upwards of $200,000, which couldn't be justified by the low volume of the application.
In rotational molding, powdered material is placed in a machine that uses gentle biaxial rotation to fully coat the inside of a mold. After rotation, the mold is placed in a convection oven (where the material fuses), and then moved to a cooling chamber, where the material solidifies. Tooling for rotational molds is far less costly than tooling for injection molding and blow molding, both of which use pressurized processes. In the Braun fuel tank application, the tooling cost between $10,000 and $20,000, engineers say.
The new fuel tank, made from cross-linked polyethylene, enabled Braun engineers to lower the floor of the minivan. Unlike the original metal tank, which held 27 gallons of fuel, the new tank is just 12 gallons. But, the use of plastic enabled Braun to eliminate multiple components and fasteners, which had been employed on the metal tank. The roto-molded tank also accelerated assembly time by 800%, the company says.
"There are other ways this could have been done, but none of them was as cost effective as roto-molding," notes Bob Dunne, general manager for Meese Orbitron Dunne. "This is a niche application. So if we had used any other method to make this tank, there wouldn't have been a vehicle."
About the Author(s)
You May Also Like