NPE overflows with new nylons
September 18, 2000
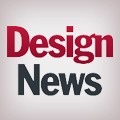
Chicago-The desirable attributes of better flowing nylons came to light at the recent National Plastics Expo (NPE), which saw the introduction of new high-flow grades from Rhodia Engineering Plastics (Lyon, France) and from DSM Engineering Plastics (Evansville, IN)
Why does flow matter so much? "Because flow delivers performance," insists Paul Bacon, an engineer who directs the worldwide electric-and-electrical market for Rhodia. Better flow properties increase design freedom-think thinner walls, larger parts, and fewer gates. Better flow can mean a resin-rich surface too, even with high glass loadings. And as long as flow doesn't come at the expense of mechanical properties, it may even let nylon compete on an equal footing with more expensive engineering materials-perhaps even in connector applications now dominated by liquid crystal polymer. Here's a closer look at the flow-boosting materials:
Rhodia's new TechnylStar line isn't your ordinary nylon. Though based on nylon 6, TechnylStar eschews conventional nylon's linear structure in favor of a "star-like molecular architecture," which in turn imbues TechnylStar with a greater fluidity than nylon 6 or 66, Bacon reports. Indeed, Rhodia's flow data from spiral tests shows that TecnylStar has nearly 100% greater flow length than similarly loaded nylon 6. At the same time, the new nylon seems to offer improved mechanical properties. "TechnylStar can give you performance never seen before in a nylon," Bacon says. For example, tensile modulus of a 60% glass-filled grade comes in at 21 GPa at room temperature. "It can match or exceed the performance of materials that sell for substantially more," Bacon says, pointing out specifically PAA, PPS, and PEI. Likewise, TechnylStar's elongation at break, thermal performance, and surface finish offer advantages over regular nylon and can compete with more expensive materials in a variety of applications. "We're not just limited to traditional nylon applications," says Bacon. "We believe TechnylStar will broaden the potential for nylon into new applications." One of those he singles out is connectors that use LCP for flow but don't require its resistance to heat.
Rhodia will initially offer five varieties of new materials. Two TechnylStar SX grades offers respective glass loadings of 50 and 60%, while a third SX grade combines 40% mineral and 25% glass reinforcement. TechnylStar S grades, intended for the most demanding high-flow applications, come in 30% glass and 25% mineral/20% glass versions. A flame-retardant grade capable of meeting UL 94 V-0 requirements is in the works.
DSM, meanwhile, has developed a new high-flow nylon 46 that can go head to head with LCP in a variety of memory connectors. Flow-wise, these new Stanyl grades can get within 10% of LCP, according to DSM vice president Roeland Polet. Previous high-flow Stanyl grades, by contrast, could do no better than 30 to 40%. And even with flow improvements, the materials have managed to maintain their mechanical performance. "There's no real sacrifice in properties," says Polet. In fact, Stanyl's tensile strength and toughness have resulted in weld line strengths up to three times greater than LCP in comparative tests that DSM conducted on 1.27-mm DIMM and 1.0 mm RIMM connectors. Positioned as a drop-in for LCP, the new Stanyl also has competitive processing, electrical, and dimensional-stability attributes. In particular, Polet notes that it can be used in existing LCP tools-Stanyl's higher shrink rates are offset by its moisture absorption for final dimensions that equal LCP. Bottom line: Part costs can be cut in half, Polet reports.
The first of the Stanyl grades is a 40% glass filled that meets UL 94 V-0 requirements (at 0.8 mm). Other Stanyl grades will follow with different reinforcement levels. And Polet reports that DSM will soon introduce nylon 6 grades based on the same high-flow technology that Stanyl uses.
About the Author(s)
You May Also Like