HyperSizer v6 Keys in on Manufacturing Optimization
May 13, 2011
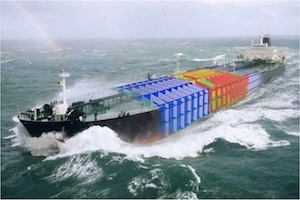
Riding the trend of composites becoming a go-to material fora variety of products - from aircraft to wind turbine blades - Collier Research Corp. released an upgradeof its HyperSizer structural sizing and analysis tool with new capabilities tooptimize manufacturing.
In keeping with the evolution of the software and the use ofcomposites across a variety of industries, HyperSizer v6, the latestcommercialized version of software developed and used at NASA, now incorporatesfeatures designed to address two of industry's biggest concerns, according toCraig Collier, president of Collier Research. That is the inaccuracy ofanalysis functions within current tools to validate test data and some of theinefficiencies surrounding manufacturing of composites.
"We're finding that industry has now embraced composites asmore mainstream," says Collier, who says, up to date, companies have been conservativein terms of their design and use of composites. Specifically, because of theexisting tools' limitations in predicting and analyzing failures, engineeringgroups have been limited in exploring optimized composite layups simultaneouslywith other design variables. This inevitably leads to design inefficiencies andadding unnecessary weight to composite-based designs, Collier explains.
To address those deficiencies, HyperSizer v6 now has anintegrated suite of failure analysis predictions that are validated to testdata, an enhancement that will allow engineering groups to be less conservativein their use of composites, Collier says. The software now also automates the process ofidentifying, defining and controlling ply-count compatibility, laminatesequencing, interleaving and ply-drop minimization-all steps that have historicallybeen done manually and been an onerous burden for engineers, limiting their abilityto zero in on optimal designs.
"It used to be done manually and it wasn't done well becauseit was such as tedious process," Collier says. "There are so many billions ofcombination and ways to do things, without automation, it was difficult toexplore all the possibilities."
Sandia National Laboratories,specifically its Wind Energy Technology Department, is using HyperSizer andpartnering with Collier Research, on large-scalewind turbine design. Tom Ashwill, technical leader in the lab, says theHyperSizer v6's automation enhancements should address the challenges designershave today in terms of knowing what shape to make a laminate zone, where tostop one zone and start another or how to determine an optimum thickness oflayups in different zones. It is also difficult to manually calculate how tohandle transitions between zones and where to position many individual plydrops and adds in a single blade, Ashwill says. Using blade-loading resultsfrom FEA, HyperSizer will map the laminate zones to more accurately representthe blade physics and calculate a ply stacking sequence for each zone-acapability, Ashwill says, that will greatly improve the composite design andmanufacture process.
In addition to these features, HyperSizer v6 alsoincorporates automated compression, shear and compression-shear post-bucklinganalyses--features designed to help engineers cut weight in aluminum skinairframes. These analyses, which havebeen difficult to perform with nonlinear FEA, are now extended to compositematerials in this new release.
About the Author(s)
You May Also Like