Case of the Skewed Chips
March 6, 2012
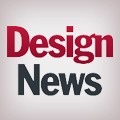
While I worked for Panasonic Factory Automation, I installed several MVIIc chip shooters. These machines placed about 10 surface mount chips per second. If the placement rate dropped below about 99.99 percent, it was time to stop and fix the problem. I had installed and verified the calibration of a machine in a new manufacturing area at Celestica, then a subsidiary of IBM. During the acceptance testing, the chips were slightly skewed, but within specifications. The machine didn't fail, but it wasn't as good as we expected it to be.
The calibration involved the theta 1, 2, and 3 axes. The procedure was to install the large camera jig to a head on the turret, manually index it to the theta 1, and engage the axis. Then we would carefully index the turret backward to the placement position and use the X-Y table and a dial indicator to measure the runout. To do theta 2 and 3, the turret was indexed backward to the axis, engaged, indexed forward, and measured. All three theta axes were less than the specified runout spread. I think it was 0.1mm across 1 inch, but the chips were still skewed.
I checked and rechecked the theta axes calibration. A senior technician also checked the calibration and found nothing wrong. The manufacturing area was not in production yet, so the problem was not urgent. The fall-back position was that the chips skewing were still within specifications, so we could get along with the skew, but it wasn't ideal.
The problem bothered me. I continued to wonder why the calibration was good while the placement was skewed. Eventually, I reviewed the placement sequence of operations step-by-step in my mind. The theta 1 engages the nozzle and rotates it to the pickup orientation. The machine indexes to pick up, picks a chip, and then indexes to theta 2, machine vision. Then it takes a picture of the chip on the nozzle. The machine then indexes to theta 3 and corrects angle variations detected at theta 2. The chip is then placed.
The machine then selects the nozzle for the next chip placement and indexes to theta 1. The nozzle brake at theta 1 contacts the nozzle to create drag to ensure engagement. But what was the theta 1 brake actually doing? The exact indexing angle of the theta 1 nozzle brake engagement and disengagement was not in the technical manual. I carefully indexed the turret manually a little at a time, walking from the front to the back, and observing the theta 1 nozzle brake. Lo and behold, the brake was contacting the nozzle during the turret indexing. I adjusted the theta 1 brake to clear the nozzle during indexing, and the skewing went away.
This entry was submitted by Glenn Aitchison and edited by Rob Spiegel.
Glenn Aitchison's first field service job was in 1987. Since then, he has worked with automotive robotics and other industrial automation and machinery. He has received his Certificates of Qualification as an industrial electrician and as an industrial mechanic (Millwright).
Tell us your experience in solving a knotty engineering problem. Send stories to Rob Spiegel for Sherlock Ohms.
Related posts:
About the Author(s)
You May Also Like