TPE Seals Relax
September 22, 2003
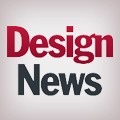
Rubber seals may seem simple, but they often face temperature and loading conditions that make it all too easy for the wrong material to fail prematurely. The classic way of picking the right material has been to look at compression set (CS). Yet this commonly cited elastomer property doesn't begin to tell the design engineer "100% of what he needs to know," argues Thierry Burton, Advanced Elastomer System's resident expert on seals. He and his colleagues at Advanced Elastomer, which makes Santoprene thermoplastic vulcanizates, have turned to a more complete testing regimen.
Instead of focusing only on compression set, which measures changes in the height of a standardized material specimen following a short period of compression, Burton advocates compression stress relaxation (CSR) methods. Using specialized lab equipment, these tests are designed to measure the decreasing counterforce exerted by a specimen that has been compressed to constant deformation under specified conditions of time and temperature.
Internal tests: AES supplements the data from standardized compression stress relaxation tests with its own internal methods. The first (see graph) compresses samples at carefully controlled speeds to account for the initial relaxation that standard tests ignore.The second subjects samples to thermal shocks, as opposed to the long aging of the standard tests. The results from this internal method (see table) give a quick indication of how well a TPV grade will seal -- the lower the force retntion, the lower the ability of a materila to seal at a specified temperature. |
Measuring this "force decay" tells design engineers things about prospective sealing materials that the CS data just won't reveal. As Burton explains, CS does a good job indicating a material's elastic recovery, which governs dynamic seals. "The higher the compression set, the lower the elastic recovery, and the poorer the sealing performance," he notes. But CS doesn't quantify the variations in sealing force over time. And this attribute governs the performance of seals under load. It's particularly important for static seals since they function under continuous strain and don't require the kind of elastic recovery performance needed by dynamic seals.
Several kinds of CSR tests have been used to evaluate TPV sealing materials over the years. Burton says the most common, and least useful for design engineers, is ISO 3384 A. It starts with specimens that have been preconditioned at an elevated ageing temperature before compression, and it measures the force relaxation at that elevated temperature. The test also disregards any relaxation that occurs before 30 minutes of compression time. Though potentially useful as a way to screen competing materials quickly, these test conditions really end up measuring the forces on hot, annealed samples. So they don't yield force data accurate enough to optimize seal designs, Burton says. A related test, ISO 3384B, paints a more accurate picture by doing away with the thermal preconditioning and allowing samples to cool to 23C prior to the force measurements. But it too ignores any relaxation prior to 30 minutes.
Yet another CSR test, ASTM F-913, works much like ISO 3384A, except that it starts its force measurements at 3 minutes rather than 30. This approach has its own problems, in Burton's view. "Steady-state conditions from the testing of Santoprene rubber are not met after 3 minutes compression," he says, noting that attempts to extrapolate from 3 to 30 minutes tend to exaggerate the force decay.
Age effects: Results from stress relaxation testing with heat cycling (ISO 3384B) shows that Santoprene TPV exhibits a linear relationship between the force retention and the logarithm of the residence time at 70C. Information about force decay can help design engineers predict how high initial sealing forces have to guarantee seal integrity over time. |
To make up for all these deficiencies, AES has supplemented the standard CSR tests with an internal test that estimates the initial force relaxation-that occurring before 30 minutes. This method involves measuring the loss of compression force in a sample button compressed not just to specified force and temperature but also speed.
Another AES internal test hits samples with thermal shocks in an effort to accelerate the ageing process. "These results lead to a rather quick evaluation on the sealing ability of any TPV grade," says Burton. "The lower the force retention, the lower the ability of a material to seal at a specified temperature."
So what should design engineers do with this CSR data? Since it puts forces in the context of thermal conditions and age, Burton says, engineers can readily use it to calculate the initial seal forces required to guarantee seal performance over time.
About the Author(s)
You May Also Like