The Case of the Failed Leading Edges
April 26, 2013
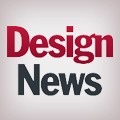
In one of my many liaison engineering sojourns in the aerospace industry, I got involved with a pile of wing leading edges, which hadn't passed structural testing. These were all in quarantine awaiting a possible decision by design.
The production supervisor went over the processing documentation with me and proved that everything was being done by the book. Meanwhile, there was a sporadic failure showing up in testing ... not by much, but enough to label the parts as nonconforming.
The testing lab received a sample part cut from the product. They made up tensile test pieces and loaded them to failure. It just so happened that the lab was preparing a specimen for testing while I was visiting, so, I followed the process. The technician started grinding the composite test piece. I asked why he was doing this, and he said he wanted to get the test piece to conform to the standard dimensions. I then asked if he always had to grind the parts. He said that occasionally they came in the correct size. In that case, there was no need.
I went back to the production supervisor and asked if any material from the rejected leading edges was still available. After searching around the quarantine cage I found that several of the rejected parts still had surplus material that could be used to make new test pieces. This time we made a tool for the waterjet cutter, which produced test pieces consistently within the specified sizes. I took them down to the lab and had them tested. This time the technician did not have to grind them to size and they passed, on average 22 percent higher than minimum. That particular leading edge was brought out of quarantine and back into production.
I explained to all concerned that grinding the composite created all sorts of nonconformance along the ground edges, lowering the effective cross section area -- just enough in several cases to cause the rejections. Test pieces were made up for the other leading edges and most of the quarantined parts ended up back in production.
Today, when you consider outsourced components, you have to be aware of what goes on in the background that the customer doesn't know.
This entry was submitted by John Mitchell and edited by Rob Spiegel.
John Mitchell was self-employed through Mitchell Research. He worked mostly in aerospace design/liaison engineering with excursions into product/quality engineering on batteries, forensic engineering analysis, and Hovercraft. He is now retired and working on vertical axis wind turbine systems and small electric vehicles.
Tell us your experience in solving a knotty engineering problem. Send stories to Rob Spiegel for Sherlock Ohms.
Related posts:
About the Author(s)
You May Also Like