Engineering News 7409
June 23, 1997
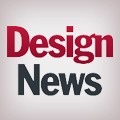
Electronics enhance security
Newton, MA--In 1995, just four days before Christmas, this editor returned home from work and discovered that unknown parties had kicked in his back door and burglarized his house. Local police later captured one of the thieves, a chap who turned out to have more than 140 arrests on his record.
It would be nice if persons like that burglar either reformed or underwent spontaneous combustion. Since the latter seems unlikely, protecting individuals, their property, and businesses from criminals has become big business in our country. Demonstrating that even the nastiest problem can be a business opportunity in disguise, Print-Scan International has developed a software-based system that can recognize fingerprints, Micro-chip Technology has developed a code-hopping remote keyless entry system that foils scanners and code-grabbers, and LoJack Corp. has found ways to extend the range and effectiveness of its system for recovering stolen cars.
Smart software. Thieves can, and do, steal keys, credit cards, and passwords; computer-literate crooks can decipher PIN codes and forgers can fake signatures. But a new software-based system may make these well-established means of thievery nearly impossible. Any application that demands the use of a key, signature, PIN code, or password can employ Print-Scan(R) fingerprint verification software.
After capturing an average of 15 to 18 data points, the system reduces fingerprints to an algorithm. These data allow users to confirm a person's identity at a later date by scanning the same finger and comparing its image to the stored algorithm. The PrintScan core software employs Coincident SequencingTM, a process recognized by law enforcement agencies worldwide as proof positive of a person's identity.
Fingerprints consist of patterns of ridged skin. The ends of these ridges and the forks (bifurcations) are called minutiae. "Once we've defined the minutiae," says Torben Huge-Jensen, president of Print-Scan International Inc., Martinsville, NJ, "we draw an imaginary line between each and every minutiae, and we count the ridges between each and every minutiae." The company claims its PrintScan software achieves a 0% false-accept rate and a 1 in 100,000 false-reject rate. Written in ANSI-C, PrintScan core software is claimed to be easily portable to many different hardware platforms and operating systems.
In civilian applications, eight minutiae in coincident sequence suffice to confirm a person's identity. In cases that involve criminal law, requirements vary from country to country. Typically, however, regulations will call for 12 to 17 matches.
Data are gathered for the software by a simple optical scanner. The data go to a frame grabber, which transforms them and feeds the information to a computer. After capturing the necessary minutiae, the software generates an algorithm that describes them.
PrintScan International's system doesn't require a great deal of computing power. Embedding the software requires about 500 kbytes. Operating speed depends upon the processor employed. "We prefer a 486 or better," says Jensen. "When we get a Pentium, then we are down to 0.4 milliseconds to do the comparison. We can do what we are doing today on a 386, but it requires 8 to 10 seconds."
At this time, a typical use for the software is inmate processing and identification in jails. But Jensen says the company has already started developing other security applications for the software. "We have embedded it into a small system that we call Secure Room, where 10 to 15 people go on the system, and only they will be able to get into a room." At the present time, PrintScan International has installed, or is negotiating to install, approximately 50 of its fingerprint verification systems.
Foiling code grabbers. Use of a remote-keyless-entry system can effectively give a crook equipped with a scanner or code grabber access to your property. Typically, the signal transmitted by your garage door opener (to pick one example) is set by a standard 8-pin DIP switch. This produces about 256 possible combinations. Using a scanner, a criminal can generate all 256 codes in about 30 seconds. Also, because the fixed-code system always transmits the same 40 bits, a code grabber can record the signal and then retransmit it.
To hinder the creeps who wander about trying to capture transmitted access codes, Microchip Technology Inc. has developed a family of code-hopping devices called KEELOQ(R). They use a long code word plus encryption and synchronization techniques. A complex nonlinear algorithm encodes the transmission sequence. Given that each 68-bit-long transmission uses a different code, capturing the code won't allow entry. And the coding process reportedly prohibits an intruder from calculating the key, even after capturing and analyzing a large number of transmissions.
A KEELOQ encoder/transponder, such as the model HCS410, has an EEPROM array loaded with a 28/32-bit serial number (unique for every encoder), an encryption key generated at the time of production, and a 16-bit synchronization value. Microchip produces the key using a key-generation algorithm. Inputs to the algorithm are the encoder's serial number and a 64-bit manufacturer's code. The synchronization value becomes the basis for changing the transmitted code for each transmission.
Because of the code-hopping encryption algorithm's complexity, a 1-bit change in the synchronization value produces a big change in the transmitted code. Every press of the transmit button causes the encoder to read the button and update the synchronization counter. Software then combines the synchronization value with the encryption key, and an output of 32 bits of encrypted information results. These data change with every button press. This "hopping" part of the code word, combined with button information and the serial number, form the transmitted code word.
According to Microchip, in more than 64K transmissions, a specific code is used only once. Based on 10 operations/day, this rate means that a code won't be repeated for 18 years.
Car rustlers. Automobile thieves infest most U.S. cities. One of the more effective means of recovering stolen vehicles--and sometimes catching the criminals--is the well known LoJack(R) System from LoJack Corp. The part of the system installed in a police car consists of an array of four quarter-wave antennae mounted on the roof in a 12-inch-square pattern, a receiver in the trunk, and a display unit on the vehicle's dashboard. A twisted pair delivers the digital signal from the receiver to the display. Each customer's car contains a transmitter that police activate if the vehicle is reported stolen.
Until recently, police officers tracked stolen cars by looking at a dashboard-mounted display as they drove. Doing so can be tricky in city traffic. But by using receiver input to generate an audible signal, a LoJack engineering team led by Project Manager Rod DeMille enabled the police to "hunt by ear."
"Most experienced trackers primarily use the signal strength, which is indicated by the tone. The closer the operator gets to the stolen vehicle, the higher in pitch the tone becomes," says DeMille. The system's display panel provides right/left information. A 486SL or equivalent chip provides processing power, and the necessary algorithms reside in firmware. Engineers also extended system range from the previous 1 to 2 miles to 2 to 3 miles.
Another LoJack innovation, now in the final stages of testing, is called the listening post. It's a stationary tracking unit that provides 24-hour coverage of a city area. The system, a modified version of the equipment used in police cruisers, includes a computer equipped with a modem. When a car with an activated LoJack transmitter travels through the listening-post area, the system sends a message back to a police command post that includes the car's identity, location, direction, and speed.
Getting the computer to decide when it should call the central station proved a bit challenging. "What we thought would be primarily a hardware effort is turning out to be more of a software effort," DeMille explains. "A police officer looking at a display and doing some tracking is one thing. When you try to teach a computer to do that, it gets a little tricky." The computer must understand, for example, at what percentage change in signal strength it should call the central station. Engineers don't want the system repeatedly reporting on a vehicle the police already know about.
When such listening posts become widely used, police could place an array of the systems around cities, or concentrate them in specific areas plagued by auto theft. Ideally, they would be located on tall buildings with a 360-degree view of the horizon. But, of course, ideally people wouldn't steal cars.
For additional information on PrintScan International's fingerprint identification and verification system, visit the firm's web site at www. printscan.com
Flatness wins out for manifold housing
Detroit--Ford Motor Co.'s latest switch to plastic involved the intake manifold runner control (IMRC) housing for its 4.6l, four-valve engine. Previously, the 420 x 89 x 29-mm part, called a deactivator, was cast from aluminum then machined to required tolerances.
Use of the new part, injection molded from Ryton(R) polyphenylene sulfide (PPS) supplied by Phillips Chemical Co., Bartlesville, OK, will enable Ford to project significant savings in cost and weight over its old aluminum counterpart, claim company officials.
The switch required imaginative engineering to mold the plastic IMRC with the same tolerances that machining gave the aluminum part. Tier One supplier Tomco Plastic Inc., Bryan, OH, developed a proprietary process to make a mold that gives the deactivator critical flatness right off the press.
The deactivator, a throttle device in the intake system, restricts air flow and increases air velocity to the combustion chamber at low engine speeds--generally below 3,000 rpm. This enhances the combustion process, improving fuel economy and low-end torque, while reducing emissions. At high engine speeds, the throttle opens for added air flow to maximize engine power.
To make the transition to PPS from aluminum, Tomco first created a product from an uncontoured mold. This rough tooling was then contoured to exact specifications using data generated from the pinpoint accuracy of a coordinate measurement machine (CMM). Tomco then applied its proprietary formulas for converting the CMM data to tool steel dimensions in the mold.
"If it wasn't for Tomco's ability to be innovative in its mold-building technique, the IMRC would still be made from aluminum," says Walt Fedison, a design engineer at Ford.
"We knew that the flow pattern in a traditional mold would not produce a part that would match the machined aluminum tolerances, regardless of the polymer," adds Bob Wisler, market development manager for Tomco. "The computerized mold contouring process goes beyond what current mold-flow analysis can achieve."
ANSYS adds support to Design News foundation
Canonsburg, PA--This spring, ANSYS Inc. announced its donation of $10,000 to the Design News Engineering Education Foundation. The gift marks the company's first participation in the program, which benefits engineering students at the university level.
As a result of the donation, Design News was able to give funds to the engineering schools at the University of Alabama, Florida Atlantic University, and the University of Detroit. These are the schools designated by the Design News Engineer of the Year Bernard Dagarin of Hughes, Special Achievement Award winner Graham Hawkes of Hawkes Ocean Technologies, and Quality Award winner Ken Dabrowsi of Ford.
ANSYS offers a variety of software products to help customers meet engineering challenges. Engineering analysts and design engineers use the company's software to accelerate product time to market, reduce production costs, improve engineering processes, and optimize product quality and safety.
ANSYS software is installed at nearly 2,000 colleges and universities with nearly 72,000 licenses worldwide. "Trends in the workplace today are driven by technology," says Peter J. Smith, ANSYS chairman, president, and CEO. "Successful companies recognize the benefits of implementing state-of-the-art tools that enable multidisciplinary teams to work collaboratively."
In addition to the Design News donation, ANSYS continues to support burgeoning engineers in other ways. Currently there are nine students from the University of Pittsburgh working within the ANSYS Student Cooperative program. Participants rotate their schedules by working one semester at ANSYS and one semester at school for the duration of their undergraduate curriculum. Moreover, the company works closely with local universities and healthcare research projects to help improve the quality of life.
Composites replace titanium for jet-engine case
West Palm Beach, FL--Pratt & Whitney has developed a large, complex composite part that should significantly reduce the weight and cost of military aircraft engines. The component, a fan inlet case (FIC), supports the shaft bearing to the engine case. It consists of an inner bearing hub, multiple airfoil-shape struts, and an outer support ring and mounting lugs, all molded as one piece.
The composite part will replace the titanium assembly currently used on the F119 engine, built by P&W for the Air Force's F-22 air superiority fighter. Compared with the titanium assembly, the composite case shaves 15 lbs of weight. Further, the molded, single-piece component costs considerably less than the titanium assembly, which consists of many machined details that are secondarily assembled. The full-scale FICs have been statically tested to worst-case load conditions.
The process that enables such a complex and critical part to be made with composites is called Advanced Resin Transfer Molding (AdvRTMTM) developed by Dow-United Technologies Composite Products Inc., Wallingford, CT. This process allows all external air-passage surfaces of the FIC to be molded to smooth, final dimensions without the need for secondary machining.
"There is no question that Dow-UT's process enables significant weight and cost savings," says Michael Gevers, team leader, composites design at P&W's Compression System Component Center. "The ability to reduce the overall part count and eliminate many labor-intensive assembly operations makes this composite part an important improvement over titanium."
Simulation opens door to faster auto design
Dearborn, MI--When Timothy W. Taylor, product development engineer at Ford Motor Co., set out to design a new power lift-gate system for a sport utility vehicle, he turned to a recent addition to Ford's design-tool arsenal: Working Model simulation software from Working Model Inc., San Mateo, CA.
An automatic door on a sport utility vehicle typically speeds up slightly as it opens, travels at a constant speed, then slows as it approaches the fully open position--all in a matter of seconds. Taylor knew he wanted this sport utility's door to open in six seconds. What he didn't know was how much force was needed for the system's struts to push the door open at that rate.
Most often at Ford, engineers create geometry in a 2-D drafting package on workstations. They then translate this information and import it into Working Model on a PC. But because the geometry of the lift-gate system was simple, Taylor started by creating it within Working Model.
He then constrained the strut model using the software's Constant Velocity Motor. During the simulation, he monitored two specific quantities of the strut: the extensional speed and the force. Both were obtained as a function of the extension, or length change, of the strut through the simulation. Taylor then used these quantities to establish the requirements for the strut.
"The forces in the struts are dependent on the time you select to open the door," says Taylor. "So once you are sure how fast you want the door to open, it's only a matter of running the simulation once."
Using Working Model, he finished the entire study in days. Figuring out the forces necessary by hand would have taken months, he says. Someone would first make rough hand calculations, which alone could take days. Building a prototype could then take several months. And once testing begins, the prototype would most likely need to be "tweaked" to achieve the responses desired.
"That's a terribly time consuming process, and it is very expensive," notes Taylor. "And, the prototypes may not even be able to achieve what you're trying to do because you gave too rough an estimate from your hand calculations.
"With Working Model, setting up very specific design parameters for the struts saves tremendous time and money," he says. "We'll still build a prototype to investigate, but we suspect the first prototype will be very close to what we want so we won't have to build extras."
The bottom line, says Taylor: The company can now bring products to market faster, and that means cheaper products for consumers in the long run. "Because the testing and building is now done analytically, we just verify the design with a prototype," he explains. "Plus, by doing this up-front engineering work, we think we'll end up with a product that's closer to what we want, so customers will be more satisfied."
Friction material eliminates clutch dismantling
Minneapolis, MN--Unlike most other disc-plate clutches, the ADAMTM clutch has special servicing features designed to save time and effort, says its maker, Tol-O-Matic Inc.
The ADAM clutch incorporates a two-piece, non-asbestos friction material that can be easily replaced without dismounting or disassembling the clutch. The material is in two semi-circular pads held to the friction plate by flathead screws. The screws are accessible through two access holes in the finned plate. To change the friction pads, the technician rotates the pilot plate to align the screws with the access holes in the finned plate. Once the screws holding the friction pads are withdrawn, the pads can be easily removed. Placing new friction pads on the pilot plate and replacing the screws finishes the job.
"The design eliminates the disassembly of product and machine, virtually eliminating the downtime normally associated with the pad replacement process," says Todd Zarbok, sales support manager at Tol-O-Matic. "It turns a two hour repair job into a fifteen-minute preventive-maintenance procedure."
The clutch also lets you compensate for friction material wear. Using an adjustment nut on the air cylinder end of the 400, 600, and 800 models, the user can adjust the finned plate, returning the disc-plate gap to its original setting of 1/32 inch (0.749 mm).
The clutch's parallel disc-plate design provides fast starts (but soft where needed), and the finned, cast-iron plate on the 400, 600, and 800 Series quickly dissipates heat generated by high cyclic applications such as conveyors and packaging equipment.
V-22: getting skinny
Waltham, MA--A new, lightweight power-management system for the V-22 Osprey recently completed its first test flight on the aircraft, according to its manufacturer, Kollmorgen Artus, a division of Kollmorgen Corp. The system reduces voltage fluctuations produced by the V-22's generators and eliminates occasional power interruptions.
The V-22 uses Kollmorgen's new ac/dc regulated power-management system to convert the 115V/400-Hz ac power from the aircraft's generators to regulated 28V dc power. The system also limits voltage fluctuations to a range of plus or minus 0.1V. "This power-management system decreases the range of voltage fluctuation by 99% and provides uninterruptable power," asserts Robert Perrin, managing director of Kollmorgen Artus, Arville, France.
Engineers typically deal with voltage fluctuations onboard an aircraft by using larger wiring and special systems that compensate for voltage fluctuations exceeding 10V. Current power-management systems can provide dc power in a range as large as 21 to 32V. The Kollmorgen system allows the use of lighter, smaller wiring, and eliminates the need for separate power-conditioning equipment. Such changes reportedly reduce vehicle cost, cut its weight by approximately 200 lbs, make the aircraft more fuel efficient (because of the weight reduction), and reduce aircraft power-up time before takeoff.
Kollmorgen's power-management system was integrated with the V-22 during the engineering and manufacturing development stage and will be used on the production model of the aircraft. Technology developed for the project is directly applicable to civilian aircraft, according to Kollmorgen officials.
Electronics, U-joints extend glass-former's life
Windsor, CT--In 1928, as the Roaring Twenties rolled downhill toward the Great Depression, Emhart Glass Co.'s predecessor firm designed and patented its H-28 Glass Forming Machine. Continuously updated, the H-28 has produced billions of pieces of fine glassware.
During a recent renovation of the machine, Emhart installed its patented Computer-Based Electronic Cam Position System to permit cam adjustments on-the-fly as the machine operates. Step-motor drive systems used for cam repositioning incorporate 16 universal joints from Curtis Universal Joint Co., Springfield, MA, that provide five years of operating life in the hot, steam-laden atmosphere produced by the H-28.
Designed in a carousel configuration, the H-28 consists of a central drum with 12 to 18 glass-forming sections that revolve around it. Cams on the central drum trigger mechanical and pneumatic components to guide the glass-forming process. To accommodate changes in glass viscosity, forming speeds, and other variables, workers adjust cam positions.
Manual cam adjustment required machine shutdown and disassembly to pull one or more forming sections, reach a specific cam, adjust it, reinstall the section, and reconnect linkages, hoses, etc. If the adjustment turned out a bit off-target, the operator repeated the entire procedure.
In the new setup, a controller at an operator's console commands step-motor drive systems that adjust the position of horizontal cam sliders. Step motors deliver power to speed reducers and bevel-gear sets to move the sliders and advance or retard cam actuation. The steppers deliver power through Curtis U-joints, which must operate seven days a week.
Senior Project Engineer Mike Ciriello of Emhart Glass and his colleagues selected the Curtis U-joints on a single-source basis "because of the unique feature they have, this patented spring clip." Called the Tell-Tale Lock Ring, the clip fits into a recess on the U-joint. When driven into place, the clip snaps into the recess and locks up the U-joint's components. After U-joint assembly, the ring's tip is visible, and allows the operator to confirm that the locking ring is in place. Designed for easy disassembly and reassembly, Curtis U-joints come in a range of metals from Monel to naval brass to stainless steels.
Seal design plugs turbine leak
Warsaw, MO--In 1962, during the planning stage of the Harry S. Truman Dam and Reservoir, the design was modified to include a six-unit, 180-MW hydroelectric power plant. An initial analysis of the site detected massive bedrock at the tentative powerhouse location. A slant-axis design, with turbines installed at a 24-degree angle, was selected over a traditional vertical design, in part to eliminate added excavation. However, the design experienced problems that were just recently solved.
With pumpback capability, each powerhouse unit acts as a reversible pump turbine, providing considerable cost savings over traditional plants. Water from the upper reservoir flows through the turbine to the lower reservoir during peak-energy-use hours to generate power. During off-peak hours, the plant can purchase power from the utility at a reduced cost and reverse the cycle.
But the benefits of the slant-axis design were overshadowed by numerous operational and maintenance challenges. Most failures of the turbine components in the plant were attributed to fatigue. Then, on December 1, 1985, the plant experienced loss of blade control in one unit due to a failed eye bolt, an integral internal linkage control mechanism. The next day another unit had the same failure.
The Kansas City District of the U.S. Army Corps of Engineers decided to undertake the engineering, design, and field work for turbine repair. Deliverable items, such as machine work, were contracted to the private sector.
A long-term problem that needed solving focused on excessive oil leakage at the seal interface between the oil-head assembly and the runner hub. The leakage created an increase in turbine oil maintenance, hampering manpower availability to perform other activities.
The original seal design consisted of a three-ring-square packing. A multisectional carbon seal was installed in an attempt to eliminate the leakage, but failed to do the job. The hub holds 900 gallons of oil under a normal operating pressure of 25 psi.
In April 1994, the Corps solicited seal manufacturers for design proposals to solve the problem. Requirements for the solution: rotary service at 24 degrees from horizontal; 100- to 221-rpm, 500-fpm surface speed; pressure from 27 to 50 psi; a temperature range of 30 to 120F; and radial runout from 0.002 to 0.040 inch.
"When the manufacturers provided their design recommendations, we evaluated the proposals on their own," Corps engineer Michael Scott explains. A proposal submitted by Advanced Products Co., North Haven, CT, won out.
The Advanced Products seal is a cartridge assembly composed of five machined assemblies and two 18-inch Advanced Products Enerseals(R). In the cartridge design, the seals install axially and run on the oil-pipe extension on a chromed steel surface. Oil pressure is applied to the cavity between the seals so the first seal floats. Hub oil pressure is applied to the cavity through a fail-safe orifice that limits the oil leakage rate, if the external side seal should fail.
The FLO Mark IV Flanged Axial Dynamic Enerseals have a filled Teflon(R) jacket made resilient by a high-grade internal spring that ensures positive sealing. The jacket is enhanced with low-friction and strength-enhancing additives, making it suitable for pressures to 3,000 psi, 21 MPa.
Top 10 challenges for 2007
Columbus, OH--Scientists and engineers at Battelle have compiled a list of the 10 most important technical challenges industry will face during the next decade. The list completes a trilogy of Battelle forecasts for business opportunities in the next decade. Earlier forecasts focused on leading strategic technologies and innovative products.
Challenges on the list include:
Affordable home-based health care. Home health monitors and treatments and linkages to professional care centers present a huge challenge for the health-care industry.
Personalized consumer products. The Battelle team believes many mass-produced products will not be competitive in the next century. Markets will force companies to develop sensors, controls, and computers for highly flexible manufacture of customized products.
Convergence of technology in the home. Telecommunications, entertainment, networking, education, information access, and computing power will move into the home. Technologists must find ways to manage this new home environment.
Protecting the environment and natural resources. Engineers and scientists must find ways to expand and simplify recycling programs, and develop clean manufacturing processes. Energy production and conversion must become more productive.
Human interfaces. As more complex technology appears in the home and workplace, interfaces must become intuitively obvious, safe, and fun to use.
Nutritional health. Technologies now under development will yield natural foods packed with more nutrients. Other foods will offer higher yields, longer shelf life, and natural resistance to pests. Packaging techniques will increase the shelf life of foods.
Mobile energy. In 10 years, according to Battelle's team, many cars will use alternative-fuel systems. Distributed systems for generating electricity will appear.
Micro-security. Battelle believes that technology's security challenge will shift from national security to personal and community security. Technology-based systems will protect us from crime and terrorism.
Renewed infrastructure. New materials and construction methods will be needed to renew the infrastructure in a time of limited public funding. New infrastructure needs include new traffic control and management systems, and clean, practical mass transit.
Global business competition. Technology has become a global commodity. Never has the world seen as much international trade and competition. "Controlling technology will be the competitive edge of the future," says Stephen Millet, manager of Battelle's Breakthrough Center and leader of Battelle's technology forecasting.
New mold design recaptures lost time
Shelton, CT--When General Microwave Inc., Long Island, NY, faced an unexpected delay in the development of its newest personal radiation-hazard meter, it turned to Compression Inc. to turn back the clock. Compression did the next best thing, producing the necessary tooling and 100 sets of injection-molded parts in less than 10 working days.
The size of a large pager, the meter is to be worn by individuals working near hazardous microwave radiation. The device beeps when the wearer encounters dangerous levels of microwaves. A potential life-saving device, the meter attracted immediate interest from a telecommunications company in the U.K. However, General Microwave had to meet the company's need for 100 units in a few months--or lose the new business.
Compression was originally hired to refine the design of the meter, produce a prototype using the SLS(R) Selective Laser Sintering process, and prepare the design for manufacture. For the mold-making and manufacturing, General Microwave hired a local shop. Just a few weeks into the job, problems developed. The mold maker was behind schedule and confused by the complexity of the meter's design.
With time running out, Russell Gulotta, senior vice president of manufacturing at General Microwave, realized the importance of meeting the deadline. Yet money was still an important issue. Because General Microwave had already spent an unrecoverable $10,000 with the original mold maker, getting the project finished within a reasonable budget remained a priority.
Compression came up with a solution that would simplify the project and keep costs down, while also maintaining the integrity of the seven-piece design. The strategy was to create a family mold for five of the smaller parts and two individual molds for the two larger components. The estimated turnaround time: eight days for three molds and two days for the first 100 sets of injection-molded production parts.
The 3-D solid-model databases for all seven parts were sent via modem to Compression engineers. They executed the mold splits for each of the three molds using Pro/ENGINEER. Compression then used this data to machine the QC7 aluminum cores and cavities using a mixture of high-speed machining centers, electrical-discharge machining centers (EDMs), and conventional tooling equipment.
The cores and cavities were complete in seven days, and ejector pins and water lines were added. Molding 100 sets in black ABS began three days later, and the parts were delivered to General Microwave a total of 10 days from the time it released the data. "The first 100 sets were right on time, and they looked great," says Gulotta.
Reviewing his alternatives, Gulotta is glad he turned to Compression. "It's doubtful that any other mold shop would have been able to do the job since the best turnaround time we received from the original 25 mold-makers we considered was 12 weeks," he says.
About the Author(s)
You May Also Like