3D Printing, Fastening Methods, & That Big Red Robot
February 13, 2015
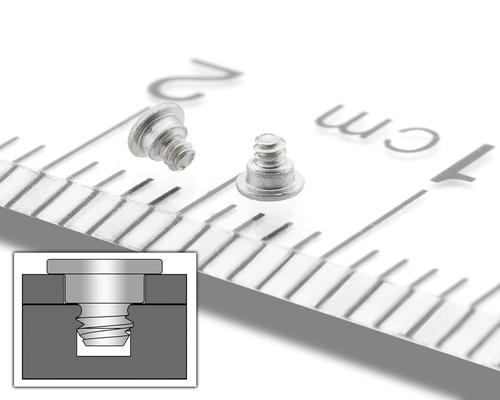
As we saw on the show floor this week at the Pacific Design & Manufacturing Show and co-located events in Anaheim, Calif., 3D printing (3DP) is contributing to distributed manufacturing and being reinvented by engineers for their own needs. Meanwhile, new fasteners are appearing for wearable consumer and medical devices and Baxter Robot has another software upgrade.
As we suggested recently, 3DP is enabling distributed manufacturing, the localized, rapid-turnaround design and production of products in smaller quantities than the centralized, high-volume processes that's become typical in industrial manufacturing. As end-production process technologies and materials have improved, some 3DP service bureaus are becoming focuses of distributed manufacturing, like micro factories. This was confirmed by a conversation with Emran Mursalin, product manager of urethanes at recently formed Stratasys Direct Manufacturing, one of the biggest commercial 3DP and AM service bureaus housing most available AM technologies and materials in facilities around the world. His Valencia, Calif. production facility, for example, turns out low-volume quantities of medical cast urethane products. Other focuses in other facilities include aerospace, automotive, and industrial products. Most of the US production sites house most of the major 3DP production technologies, such as FDM, SLS, and DMLS. We'll be telling you more about this super-service bureau later this year.
3DP Unlimited showed off its new 3DP1000, a large-format (39 inch x 39 inch x 19 inch) prosumer 3D printer using fused filament technology (also called FDM). Aside from the printer itself and its capabilities, the story behind how it was developed is an example of a theme we've reported on often: how engineers couldn't find what they needed at a cost they could afford, so they built their own. Two engineers at bearing company PBC Linear needed to make a large prototype but the only machines available cost half a million dollars, John Good, 3DP Unlimited's vice president of sales & marketing, told Design News. So they built one using some of PBC Linear's parts and also used it to demo what those parts can do. Some of the brackets on the 3DP1000 were printed on the machine, the controller software is open source, and much of the hardware, such as the extruders, is off-the-shelf. We'll be telling you more about how they did it soon.
Related articles on DesignNews.com
Proto Labs has some news about its CNC machining services, Firstcut. Firstcut product manager Judy Carmein told us they're adding turning capability for cylindrical, or rotationally symmetrical, parts starting next month in all steels and aluminums, and shortly after that in brass and copper. Turnaround will be the same as it is for milling. The company has also added same-day service for its Firstcut CNC milling capability.
I also talked to representatives of one of our Golden Mousetrap Award winners, igus inc.. igus isn't a 3DP company, they're a bearings company, making iglide plastic bearings that appear in millions of cars. But the company won the award in the 3D Printing and Rapid Prototyping category for its 3D-printable bearings material, Tribo-Filament, because it's such a nifty and useful product that's having an impact on engineers. It's now available on Amazon.com, igus' marketing manager, Michael Hardy, told us, in both versions, one of which is an FDA-approved material for food-grade items.
igus has also introduced a new material, Tribo-Tape, which comes in sheet form and can be cut and glued onto surfaces, or comes with an optional adhesive backing. The wear-resistant tape lets you add low-friction, self-lubricating surfaces anywhere it's needed in an application. The video below illustrates its properties by showing what it can do for your dancing skills when applied to your shoes. There's some other things they're doing that we'll tell you more about in an upcoming blog.
We heard a lot about wearables from the materials folks this week at the Anaheim shows, and we also heard about them from fastener maker PennEngineering. Jay McKenna, global business manager for the microPEM product line, told us there's been quite a lot of growth in wearables, including medical wearables, and demand for micro-fasteners for use in them. The company has introduced the microPEM TackScrew fastener line for compact electronics such as wearables and portables. These fasteners integrate Penn's self-clinching microPEM TackPin technology for permanently attaching sheets together with a new thread-like feature that allows the fastener to be removed when necessary, or even reinstalled once. "They're especially useful for prototypes, as well as finished wearables," said McKenna. "After removing them or reinstalling them once during development, they can then be replaced with the TackPin with no design changes."
One of our last stops was at the Rethink Robotics booth to see what's new with the Baxter Robot. The latest in the big red guy's bag of tricks is Robot Positioning System using Landmarks. As Rethink's Eric Foellmer, manager of product marketing and marketing communications, told us, this is a system to help smooth the transition of training Baxter in one job at one workspace, moving it to another job in a second workspace, and then moving it back to the first job where the locations of objects in the workspace may have changed. Cameras in the robot's end effectors take a picture of stickers at that workspace location with what look like QRC codes printed on them. These are the Landmarks that help the robot reorient itself to the changed conditions. They're stored in software and when Baxter comes back to that first job, it scans the Landmarks and adjusts itself accordingly. The following video explains this system:
Ann R. Thryft is senior technical editor, materials & assembly, for Design News. She's been writing about manufacturing- and electronics-related technologies for 25 years, covering manufacturing materials & processes, alternative energy, machine vision, and all kinds of communications.
About the Author(s)
You May Also Like