3D & 4D Printing Will Grow in 2015: New Materials & Processes
January 16, 2015
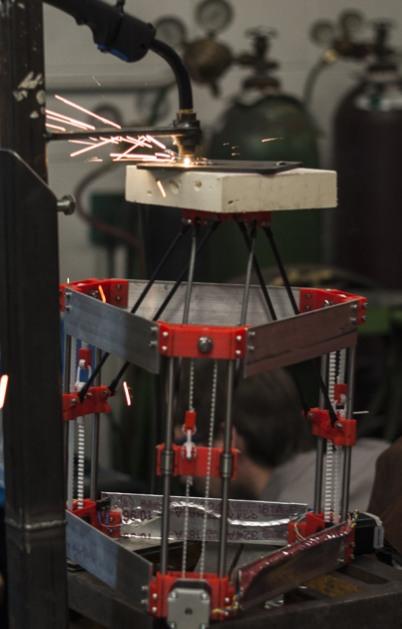
A growing though not-so-obvious role for 3D printing (3DP), 4D printing (4DP), and overall additive manufacturing (AM) is their use in fabricating new materials and enabling new or improved manufacturing and assembly processes. The often-cited design freedom that comes with AM techniques, plus some recent patent expirations, lets individual engineers, OEMs, university labs, and others reinvent the technology to suit their own needs. This democratization of processes, materials, hardware, and software is broadening what's available beyond traditional, proprietary 3DP provider-specific silos and expanding it into something resembling a real design ecosystem.
Enabling technology for new materials development
3D printing isn't just for making stuff. It's also enabling the development of new materials -- including metamaterials that don't exist in nature -- tailored to do specific manufacturing jobs. The metamaterials breakthrough achieved this year by Lawrence Livermore National Laboratory (LLNL) and MIT researchers has come after a few years of research. In partnership with researchers at MIT, Harvard, and the University of Illinois, LLNL is working with four different additive micro-manufacturing processes: projection micro-stereolithography, direct-ink writing, electrophoretic deposition, and microfluidic flow focusing.
Click the image below to start the slideshow.
Researchers are using all four to create new materials composed of microstructures with micrometer resolutions. New metamaterials being engineered with these methods will have different combinations of mechanical and thermal properties, such as strength, density, and thermal expansion, for different applications. The LLNL/MIT breakthrough engineered a new class of materials using projection micro-stereolithography with potential uses in aerospace. They are super-lightweight, high-stiffness, high-strength metamaterials with the same weight and density as aerogels, but with about 10,000 times the stiffness.
3D printing is also enabling new, stronger metal matrix composites (MMCs) that will be less expensive to produce. A new one-step 3D-printing process created by The NanoSteel Company produced a 99% dense, crack-free part with wear resistance it says is comparable to M2 tool steels made with conventional subtractive manufacturing. Using a new nanosteel powder, NanoSteel created the high-hardness, ferrous MMC parts by adapting its nanosteel powders to laser sintering, working with an unnamed process development partner. No post-processing, such as hot isostatic pressing or any further heat treatment was required, reducing production costs.
Several companies have used 3D printing to make carbon composite parts, with different levels of quality and success, from the MarkOne commercial carbon fiber 3D printer to the Windform material available only through its maker, Italian service bureau CRP Technology. Startup Arevo Labs goes beyond that by reinventing how the process works. Its technology is not a printer, but materials and software that can be used with several commercially available fused filament 3D printers in the process of being modified. The technology is aimed at aerospace, defense, and medical OEMs. Making carbon fiber composite parts with 3D printing has several advantages over traditional methods, such as controlling the carbon fiber's orientation more precisely than is possible with traditional methods such as injection molding or extrusion. Each layer can be constructed with any fiber orientation required. The company's extrusion technology is a printer head design and firmware that have been optimized for use with reinforced materials.
Enabling technology for new or better fabrication and assembly processes
3DP and 4DP processes are being used to improve fabrication and assembly of all types of products. Skylar Tibbits' team in MIT's Self-Assembly Lab, for example, has 4D printed self-assembling shapes made of programmable carbon composites and wood. In one project, using programmable carbon composites, the lab teamed with industry partners to design a morphing, non-mechanical car airfoil. In aerospace, components and structures made of these materials could change shape in response to changes in temperature, air pressure, or other factors. They could replace hinges, or even motors and hydraulic actuators, making planes simpler and lighter in weight. Another major project Tibbit's team has achieved is 4D printing programmable wood, creating custom wood grain that changes shape when it contacts moisture.
Dutch company LUXeXceL has invented a high-speed, precision, 3D-printing process for making small- and medium-sized batches of non-imaging, optical-quality components in a few days. Combined with an improved clear polymer material, the online service competes with injection molding for prototyping and manufacturing optics, while eliminating the need for expensive tooling. The new process is based on the company's Printopical technology, derived from modified wide-format industrial inkjet printing methods. It requires no post-processing steps, such as grinding or polishing. LUXeXceL has used Printopical technology in the past for making Fresnel lenses and eyeglasses.
In a truly mind-boggling feat, NASA's Jet Propulsion Laboratory (JPL) and Caltech 3D printed multiple metals in a single object, grading from one alloy to another. 3D printing different gradient metal alloys in one piece would give huge benefits to engineers designing custom parts of a spacecraft. They often need to create a multi-metal part that can't be made using traditional subtractive manufacturing techniques, or existing 3D printers. JPL researchers were inspired during NASA's Mars Science Laboratory mission by a desire to improve methods for making parts containing different combinations of metals. Aside from spacecraft, other applications for components made with this method may include commercial aerospace and automotive parts.
About the Author(s)
You May Also Like