More Seismic Shifts in the 3D Printing Industry
August 30, 2013
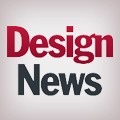
As we've discussed many times before, there are several major changes going on in 3D printing and additive manufacturing (AM). There's so much that I'll be covering multiple seismic shifts in this occasional blog. Today we look at materials.
Last time we talked about the changing relationships between OEMs and 3D printer makers, including joint development and research partnerships and investment. There's also been some consolidation among 3D printer makers, such as 3D Systems' landmark acquisition of Phenix Systems, which brings together under one roof the medium to high end of the industry that works only in plastics with the high end that works in metals.
One of the biggest factors affecting design engineers' use of 3D printing is the type of materials that can be used in a given printer, as well as the cost of those materials. Anthony Vicari, Lux Research associate and lead author of a study we reported on a few months ago, told us then that 3D printer materials are currently being sold at very high margins. Because each machine has its own customized materials set consisting of several different substances, these can be difficult to unbundle. But within each class of metals or plastics, there are potentially many more structural materials that could be used with any given printer.
Consequently, Vicari said he expected to see an open materials market with third-party suppliers selling many more types of materials than are available today. He expects this to happen by 2025, but that's up to 12 years away. I suspect it may happen much sooner. For one thing, new materials and new 3D printing methods are already being invented by university researchers and others working outside the realm of 3D printer makers.
For example, Made in Space, the company working with NASA to build the first 3D printer for use by astronauts, has said it's working on the development of new materials to work in space. At Harvard, a scientist has invented both a new printing method and new inks for the 3D-printing of tiny batteries. North Carolina State University researchers have achieved a mind-boggling feat, 3D-printing tiny structures made from liquid metal at room temperatures, which remain in a liquid state although stable. They're also bendable.
In addition to entirely new 3D-printed materials, new methods for combining them is also proceeding. At MIT, some interesting research in multi-materials 3D printing is being conducted in more than one lab. Markus Buehler's team has 3D-printed bone-like composite materials on the Objet Connex500 multi-material printer. To test their computational model, which aided them in designing three different composite structures, engineers made samples from existing Objet polymers, combining soft and rigid materials on the fly. Another team, which we will be covering soon in depth, is also working with the Object multi-material printer. This time, the aim is to improve the process that starts with specification and ends up with a multi-material 3D-printed object that contains multiple surface textures and colors.
Vicari said that big OEMs that make cars and airplanes, among other things, will want much greater control over materials and manufacturing processes as they bring 3D printing inside to apply it to their own design problems. But individual designers also want a lot more control, as we've seen in the comments section of many Design News stories on 3D-printing.
Markus Buehler's team said this very well in their article in Advanced Functional Materials: "… as 3D printers evolve, we as designers will seize more control over the manufacturing process allowing composites to be synthesized at even finer length scales, with more details and increased control of constituent material properties, opening the doors for the rapid manufacturing of structurally advanced complex multi-hierarchy biomimetic materials with applications in a large range of engineering disciplines."
Stay tuned for the next installment.
Related posts:
About the Author(s)
You May Also Like