Take a nano powder 3/1/99
March 1, 1999
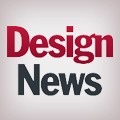
Fairfax, VA--Swords into powders? In 1993 the US Army was looking for a substitute for the potentially toxic depleted uranium in kinetic-energy penetrator projectiles used to knock out enemy tanks. Materials Modification Inc. (MMI) received an SBIR (Small Business Innovation Research) grant to investigate the use of powdered tungsten for such projectiles. In 1995 MMI Design Engineer M.S. Krupashankara began looking into microwaves as an alternative approach for efficiently making production quantities of nanometer-sized constituent materials (see table). This later work was aimed at forming lightweight armor plate to protect against projectiles!
Nanometer-size powders offer high surface area to volume--about 45 times more for 20-nm-diameter iron particles compared to typical powders of the metal at just less than 1 mum. For aerospace and automotive applications, for example, materials made from metal and ceramic nanopowders exhibit superplastic behavior, undergoing elongations from 100 to 1,000% prior to failure.
Start me up. While previous methods could make nanopowders of oxides and carbides readily, due to combining with atmospheric gases, production of pure metal powders was a problem--in some cases a violent ignition takes place on exposure to air. Prior techniques also had slow production rates of only up to 50 gm per day.
The microwave-based patent-pending NanogenTM approach developed by Krupashankara and fellow MMI materials engineer Raja Kalyanaraman "provides a dual advantage--heating the material directly and providing a high-temperature gas envelope to facilitate chemical and thermal processing," Krupashankara notes. The system focuses microwaves (6,000W at 2,450 MHz) down a waveguide. A quartz-walled reaction chamber allows the microwaves to enter and couple with the reactant-laden precursors injected into the chamber. Rapid dissociation, decomposition, and melting or vaporization of the reactants then occurs. Krupashankara says material permittivity (related to dielectric constant) and permeability (magnetic induction divided by field strength) are key properties governing coupling of microwaves to materials in the reaction chamber or plasmatron.
Coupling microwaves with materials requires tailoring to material electrical and magnetic properties. Precursor residence time in plasma and quench conditions govern the size of the Nanogen. |
The resulting plasma, at temperatures up to 1,500C, facilitates the formation of particles close to atomic size once the plasma enters a double-walled "reaction column" cooled by water. Controlling residence time of reactants in the plasma insures complete conversion. This time and the quench rate are tuned by varying parameters such as reactant partial pressures, gas flow, and temperature, which also impact on particle grain sizes and their distribution.
Downstream, a 3M filter bag that can withstand 700C separates the nanoparticles from the exhaust gas flow, where they fall into a container or bottle below. This direct bottling minimizes surface contamination. Depending on the material, slow introduction of air or a proprietary gas will quench the powder by forming a thin protective coating to eliminate any pyrophoric ignition. Or the powder containers can be sealed under argon or nitrogen for storage. Currently upwards of 1 kg of nanopowders per day can be produced.
"The real use for nanopowders is making various shaped parts," says Krupashankara. MMI has also developed a Plasma Pressure Compaction (P2C) technique "to make the biggest nanomaterial pieces in the world, 2 inches in diameter by 1 inch thick," according to T.S. Sudarshan, MMI technical director. Invented by MMI engineer Sang Yoo, the P2C method involves placing a nanopowder in a mold in a vacuum chamber. Pulsing electric currents through it removes contaminants during evacuation. Current and pressure then consolidate the part.
|
|
|
|
|
|
|
|
Information from Materials Modification Inc. |
The microwave-plasma Nanogen process (bottom) offers atmospheric-pressure processing for metallics, ceramics, and intermetallics, at higher rates (1 kg/day) than other methods, according to MMI. |
Other applications for high area/volume nanopowders
Filters for separating chemicals and purification
Coatings for strength and wear resistance
Catalysts to spur reactions
Sensors for biochemicals
Color agents for dyes and cosmetics
About the Author(s)
You May Also Like