Integrated Automation Advances Automotive Robots
June 30, 2010
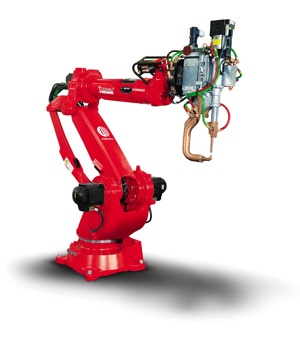
Fully automated assemblylines and integrated robotics are an essential part of modern automobileproduction. To ensure a high level of productivity, assembly, painting andwelding tasks are all handled by anthropomorphic robots which must meet thehighest demands for round-the-clock operation.
For automobile manufacturer Alfa Romeo, part of the Fiat group,robotics is a key component in the successful introduction of new cars such asthe MiTo, its latest compact car. Working with COMAURobotics, Alfa Romeo is using industrial robots for production of the MiTothat rely on dual core PCs, tightly integrated drives and high-speed EthernetPOWERLINK communications to fully synchronize drives and I/O every 400 Amusec.
"One of the highlights of the application is that we actuallydeveloped a PC that plugs directly into our drive rack," says RobertMuehlfellner, automation director for B&RIndustrial Automation. "The architecture allows for control of all thedrives in a single drive rack instead of separate motion and/or robotcontrollers."
This hardware approachsimplifies the system architecture by using one power supply and a commonbackplane where the user can plug in all the individual drive modules as wellas the PC that controls the entire robot right in the rack. All of theadditional components required are only just a handful of separate I/O nodes.
Driven by Processors
In the past, COMAU relied on customer-specific automationsolutions. But with the quest for continuous improvement and fast developmenttimes, specific solutions quickly appeared outdated, because any adjustments orimprovements reflected negatively in the total costs.
Because the most important aspect of a robot is its drivetechnology, COMAU decided in favor of standard components with interpolation ofthe axes processed centrally on a dual core processor PC. One advantage of thedual core architecture is its ability to intelligently share tasks, anddedicate one core to the run time system and the other core to support Windows.
"One core can be dedicated to visualization and the other toperform processing such as trajectory calculations for the robotics motionand/or other control systems functions," says Muehlfellner. The real-timeoperating system for the control system is VX Works-based, with Windows servingan active front end and running in the idle time of the RTOS which has fullcontrol over all the system resources and is given absolute priority. Bydedicating one core for use by Windows which runs in parallel with thereal-time operating system, if Windows has a performance issue, the real-timesystem continues running.
The industrial PC and Core 2 Duo processor offers sufficientcomputing power for path calculations that are communicated to the ACOPOSmultimodular drive system. Set values are sent cyclically using Ethernet POWERLINKto the servo drives every 400Amus and provides enough bandwidth to tunnel twocomplete robots with additional axes, I/O data, diagnostics data, safetyinformation, as well as fieldbus systems. POWERLINK also enables COMAU tointegrate combinations of Profibus, DeviceNet or CANopen master/slaves asneeded - an important capability so the robots can be connected to an existinginfrastructure in the production plants.
The complete control solution made it possible for COMAU toreduce its already optimized switching cabinet by an additional 30 percent, inpart by controlling the robot's six axes with just three dual-axis drivemodules. A feed-through model, one of three ACOPOSmulti cooling models, alsomakes it possible for the heat sink to be placed outside of the switchingcabinet. This reportedly saves even more space and prevents additional heat inthe switching cabinet.
Safe Braking
Another feature developed specifically for thisapplication was a redundant induction braking capability within the ACOPOSmultidrive to provide additional safety. When power is switched off, the robot armis suspended by motor brakes. Otherwise, gravity would pull the arm toward the ground without any brakingwhich could cause mechanical damages to both the robot and the surroundingarea.
To prevent that from happening,B&R and COMAU developed a Safe Brake Control function which provides anadditional, redundantly designed motor brake control. If the motor brake fails, the ACOPOSmulti drive system
detects it and prevents the arm from dropping rapidly by absorbing the energyin the drive system's power supply. The potential energy of the robot arm isconverted in a controlled manner to heat as it drops slowly toward the groundand prevents damage.
"Even if the robot is powered off and a brake fails, thepotential energy stored in the robot would be used to reactivate the entiredrive control system and provide control braking," says Muehlfellner. "Therobot would sag toward the ground, but it would be a slow and somewhatcontrolled motion versus crashing into the ground."
Integrated Automation Advances Automotive Robots_A
About the Author(s)
You May Also Like