Out of a jam
July 22, 2002
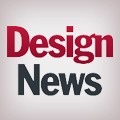
A jam in a packaging or assembly system can mean the quick resetting of a machine or hours of downtime to fix significant damage and remove shredded materials. One simple way to improve system efficiency and effectively manage jams and overloads is to incorporate an overload clutch and a sensor.
Overload clutches detect a torque overload (most commonly from a jam) and shut down equipment, such as fillers or packaging machines, so product is not wasted and the machine doesn't get severely damaged. By using a sensor to notify a busy operator, the jam can be quickly cleared and the machine returned to profit-making production quickly.
An overload clutch's function is quite simple: When torque exceeds the preset level, the overload clutch opens or slips, thus interrupting the transmission of torque in the machine. Overload clutches are available in a wide range of configurations. The most common is the spring pressure method where a spring is compressed between plates. The plates commonly press against friction material, a pawl/rotor combination, or a ball-detent mechanism. If torque exceeds the spring setting, the unit slips, the pawl lifts, or the balls move out of their 'pockets,' respectively. In some designs, these units use pneumatic pressure instead of spring pressure.
An alternative to mechanical overload clutches is simple magnetic force generated by either a set of permanent magnets or by coil magnetized by dc power. The magnetism is used to set the torque capacity of the clutch. A key difference between a magnetic unit and a spring/pneumatic unit is that when a magnetic unit slips, it continues to transmit torque up to its setting level, which tends to generate heat and means that torque transmission continues as soon as the jam is cleared. This can be a safety issue if the operator's hands aren't clear. In contrast, the pawl/rotor or ball detent type units, torque drops to near zero.
|
Choosing an overload clutch. Selection criteria are generally based on the amount of torque the unit must drive and the mounting configuration. In defining the torque, it is important to consider situations where torque spikes may occur and include these spikes in the calculations through a service factor. For example, a cut-off knife may cause a torque spike as it cuts through the material, so these should be accounted for in sizing to avoid nuisance trips.
For magnetic units, it is also necessary to determine how much heat will be generated when the unit is slipping. This is because magnetic units generate heat from transmitting torque at the set level.
Overload clutches are common in industrial applications where jams are possible, such as in packaging or assembly machinery. One example is a bottle filling application. If a bottle enters the star wheel incorrectly, it may jam in the process. This jam causes the torque to exceed the set parameters, so the overload clutch slips and interrupts the process. Stopping the machine prevents the bottle from being compressed further into the machine or shredding it in a way that causes damage to other machine components.
Adding a sensor. Some jams or overload situations are brief, so an overload clutch that automatically resets can re-engage the process without any operator involvement. However, as machines in-crease in size, length and complexity, it is more effective to include sensors with overload clutches. In this situation, a sensor activates when the overload clutch slips.
Adding a sensor to the process through a buzzer or light signal can notify a machine operator about a jam. This is extremely common in applications where the machine is rather long and complex or where the jam may occur in an area that is not easily visible to the operator.
A sensor can also improve the safety of a machine. When wired in a closed circuit, or Normally Closed (NC) mode, the sensor will open when activated and can be used to shut down a motor or disengage a clutch.
Sensor output at each overload incident also can be fed to a data collection device, which provides engineers with the data needed to prevent problems in future designs. The sensor ensures the motors are shut down or removes power to the overload electric clutch once the jam occurs. The operator can then clear the jam, reset the machine and restart it safely. A system without a sensor/switch included can be less safe, because the operator may be inclined to clear the jam while the system is running. Once the jam is cleared, a system without a sensor restarts immediately, perhaps before the operator is safely out of the way.
Built-in sensors. Some overload clutch manufacturers offer units with inclusive sensors or switches as a standard option. In these designs there are two common actuation methods. In one torque limiter design, as the clutch slips, a plate moves laterally, activating the sensor. Other types of torque limiters incorporate a pin that shifts when the torque limiter slips. In this design, the sensor detects the change in the pin's position.
When using a sensor to identify when a torque limiter has slipped, the location of the sensor is limited only to the designer's preference. The most common sensor for this type of application is a small inductive sensor. These small units have relatively short range and can be used to sense rotation of such metal items as the jaws of a jaw coupling, a key in a keyway, or the teeth of an open gear.
In each case, the sensor is used with a timer card. The timer card simply adds a time constant so that if the sensor does not produce a signal within a set time, the unit provides an output. Like overload clutches with integral sensing, this is usually an NC output.
Extra safeguards. Finally, some engineers designing machines build redundancy into their safety functions by including safety interlocks or magnetic sensors into machine access doors or guards. When an operator opens an access panel, these switches or sensors disable that section of the machine by removing its power.
Safety interlock switches add some operator safety without adding the cost and sophistication of a light curtain solution. A typical safety switch consists of a body and a key; the key is attached to an access door for a section of the machine. When the door is opened, the key is pulled out of the switch body, thus shutting down the motor for that section of the machine. The operator is then free to clear a jam or do routine parts loading safely. When the door is closed, the key is re-inserted into the body and the machine can be safely restarted.
Overload clutches combined with sensing devices are an effective way to improve efficiency and safety in mechanical systems. The initial investment in the extra components will be returned many times over from improved worker safety and reduced machinery downtime during a jam.
About the Author(s)
You May Also Like