Omron's Lynx Can Navigate Around Human Workers, Obstacles
The Lynx robot from Omron Adept is capable of intelligently navigating workspaces, avoiding humans and obstacles.
February 23, 2017
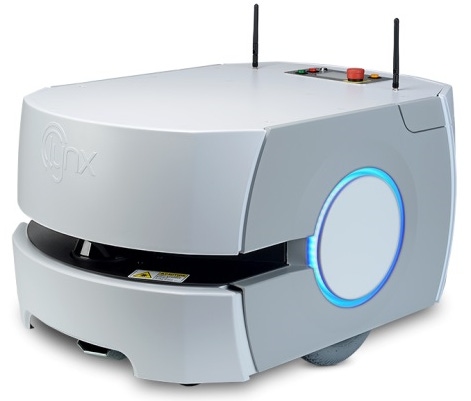
Collaborative robots can't just follow set paths and tracks if they're really going to negotiate busy workplaces and factories. Omron Adept believes the solution lies in what the company is calling mobile robotics – autonomous machines that can be deployed inside of dynamic environments (busy factory floors, hospitals, even homes) without the need for large-scale infrastructure modifications, like installing navigation beacons throughout a complex or placing magnets within the floors.
At a recent talk at the Pacific Design and Manufacturing trade show and conference, Terry Hannon, Chief Marketing Officer of Omron Adept Technologies, said there are a number of challenges around deploying autonomous robots – what Omron Adept calls Autonomous Intelligent Vehicles (AIVs). “Vehicles need to be safe, truly autonomous, intelligent, and collaborative,” Hannon said. “They must also be able to operate as a fleet, since our goal is to fully automate an environment. They have to be able to navigate highly dynamic environments. And, of course, they have to do all of this at cost.”
The Lynx can move 130 kg (about 287 lbs) and is capable of navigating around obstacles in dynamic enviroments in real time. (Image source: Omron Adept Technologies). |
On January 20 Omron Adept announced it was releasing Lynx, a self-navigating robot, to 33 countries simultaneously “as a step toward realizing harmony between humans and machines in the field of manufacturing.” The Lynx is designed for material transport (it can move up to roughly 287 lbs) in challenging environments where people and obstacles are constantly moving around (aka being a nuisance for a robot trying to get its job done).
But unlike a Roomba, for example, that goes through a lengthy process of building a map of a space – and has to shift and adjust that map (and its own path) whenever it bumps into an unexpected obstacle – the Lynx is uses proprietary artificial intelligence (AI) technology to navigate around obstacles and humans while also calculating the optimal route for material delivery. “You need to give the vehicle intelligence so it can maneuver around an environment like a human pushing a cart,” Hannon told the audience. Omron Adept says the Lynx series is ideally suited for a wide range of indoor environments including manufacturing facilities, food and pharmaceutical plants, as well as research facilities and warehouses.
Hannon said the Lynx creates this intelligence by utilizing data from a variety of sensors (a main laser as well as side, rear, and low lasers) to create a “suite of awareness and safety.” When programming the Lynx, users can walk it around “like a dog” while it laser scans an environment to create a map. “From there you can download the map to a computer and convert it into a tool you can create an application around,” he said.
But laser-only navigation has its limits. “Laser-only navigation requires a more stable environment,” Hannon said. “[The vehicle] needs to recognize at least 20 percent of its surroundings or it will get lost. Nearly all AIVs use lasers for navigation. In our experience this is half of the environments we go into – there's things like people, forklifts, and pallets." He said this can become a critical issue when you consider fast-paced work environments. "Think of a medical environment, like a hospital ER, for example. Time is not on your side so you need things delivered in time to the right place.”
Lynx overcomes these limitations with an additional camera system that observes ceiling lights. “We create a map of the ceiling lights and superimpose it onto the floor map. The vehicle uses the lights to triangulate its position,” Hannon said, adding that doing this allows the robot to detect different ceiling levels and move around in occluded environments. “The vehicle only needs to see one light.”
ESC Boston is back! Get ready for an expanded, expert-led program over two full days, May 3-4, 2017. Part of America's largest embedded systems industry conference series, ESC Boston gives you the chance to drill down into four tracks covering embedded hardware, embedded software, connected devices and the IoT, and advanced intelligence. Register Today!
Omron said that since they require no adjustments to a facility, its AIVs can be deployed at 15% of typical deployment costs. Hannon also pointed to a number of advantages of adding AIVs to the workplace including eliminating lost or misplaced inventory, accuracy, process predictability, and flexibility. “We can move fleets around,” Hannon said. “Even from facility to facility depending on demand. There is a new generation of truly autonomous vehicles already field proven. They're out there, driving down production costs, improving yield and tractability, supporting lean manufacturing, and eliminating errors.”
Chris Wiltz is the Managing Editor of Design News.
About the Author(s)
You May Also Like