August 18, 2009
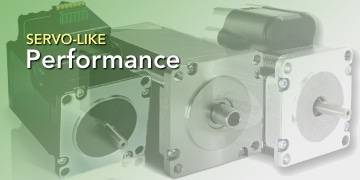
A key trend for stepper motor design is delivering improved "servo-like" motion performance, while maintaining a competitive price advantage over other offerings. Stepper motor suppliers are refining their product designs to deliver more torque at high speeds, better microstepping solutions and features such as optional encoder feedback that emphasize motion performance.
An area of innovation is software algorithms that address some of the historical weaknesses of stepper motor products. One example is loss of synchronization and torque if a large load exceeds the stepper's ability to resynchronize, once the load is reduced to a level within the motor's capability. By offering advanced algorithms and software such as Intelligent Motion Systems' AccuStep(TM) technology, step motors are elevating their basic performance capabilities and becoming a viable design alternative for more applications that require brushless motors.
ACCUSTEP PREVENTS LOSS OF SYNCHRONIZATION
The MDrive motor-driver with AccuStep(TM) technology from Intelligent Motion Systems prevents loss of synchronization due to transient or continued overload conditions, extreme accelerations, decelerations or excessive slew speed. By monitoring the location of the rotor relative to the stator in terms of motor steps, it makes sure the rotor and stator lead or lag stays within set limits. Eliminating loss of synchronization enables safe operation of the motor at its maximum torque curve, so sizing a motor with a 25-50 percent torque margin is no longer required.
The MDrive product is available in two versions, starting with an integrated motor, driver and encoder that operates in step, torque and speed modes. A second model offers a fully programmable motion controller integrated with the step motor, microstepping driver and internal encoder.
HIGHER VOLTAGE AND CURRENT RATINGS
The redesigned SilverPak 23D Plus product line from Lin Engineering delivers low cost and "servo-like" performance by providing higher current and voltage ratings than its predecessor. Increasing both the operating voltage range up to 75V and available phase current range from .3 to 5A peak creates motor winding options that result in better torque performance at higher speeds. Additional microstepping resolutions ranging from 2x up to 256x microstepping, along with four selectable damping modes, add application flexibility. Available in three body lengths (2.65, 3.16 and 4.03 inch), the motor is capable of up to 294 oz-inch of holding torque depending on the stack size of the motor. The unit also features optically isolated step, direction and disable/enable inputs, and under-voltage and over-temperature protection.
HOLLOW SHAFT DESIGN OFFERS COMPACT PERFORMANCE
Hollow-shafted versions of the Portescap h3 Series stepper motors allow wires or other media to be routed through the motor shaft, and reduce the space required for installation. The motors are available in NEMA 17, 23 and 34 frame sizes (short, one and two stack lengths available in each frame size) and with hollow shaft diameters of 4, 7 and 11 mm.
The h3 1.8-degree step motors feature a design that enables them to deliver up to 30 percent higher torque ratings than traditional hybrid step motors. Aluminum housings produce superior heat dissipation and lower power consumption. Neodymium iron boron magnets are used to optimize torque density, and a bearing retainer and o-ring design helps reduce motor noise. Larger bearings also enable the motor to effectively handle higher side and radial loads.
About the Author(s)
You May Also Like