Metering Pumps Dispense at Low Volumes
January 19, 2010
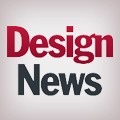
The FMI valveless ceramic piston pump is a positive displacement, rotating and reciprocating design that eliminates the random problems of check, poppet and solenoid valves that typically wear, leak or hang up. The design offers infinite variability, reversibility, positive displacement and viscosity independence, as well as precision and accuracy of better than 1 percent over 100 million cycles or more.
"The uniqueness of our piston pump design is that it takes a totally different approach," says Hank Pinkerton, president of FMI Pump. "Industries such as medical diagnostics and precision assembly demand long-term accuracy and precision to assure that dispense number one and one million are the same. They want speed, but accuracy and precision are by far the most critical requirements, and valved-type pumps cannot provide that level of reliability."
The key advantage is that the technology offers single-shot or repetitive dispensing for very low volumes (microliters) and +1 percent accuracy (0.5 percent CV or better). Flows can be as small as 500 nanoliters per dispense to as high as 1.2 m/single shot and with flow rates up to 30 gal/hour.
Valves are normally the most critical part of most precision pumps because they control accuracy and precision over time. But Pinkerton says all valves eventually wear and/or leak depending on fluids being pumped and back pressure. FMI achieves valveless pumping function by synchronous rotation and reciprocation of the ceramic piston in a precisely mated, ceramic cylinder liner. One complete piston revolution is required for each suction/discharge cycle, and the piston always bottoms for maximum fluid and bubble clearing.
At the beginning of each suction stroke, the piston rotates and reciprocates. As the piston is pulled back and opens to the inlet port, suction is created and fluid fills the pump chamber. As the piston reaches the highest point in the reciprocation cycle, the pump is at its maximum volume capacity. Continuing the rotation, the inlet port is sealed and crossover occurs. As the inlet port is sealed and the pump chamber is full, the outlet port opens. But only one port is open at any time and at no time are both ports interconnected.
During the discharge stroke, the piston is forced down and the piston flat opens to the outlet port. Discharge is created and fluid is pumped out. The piston bottoms for maximum fluid and bubble clearing. Continuing the rotation, the outlet port is sealed and crossover occurs. As the outlet port is sealed and the pump chamber is empty, the inlet port opens to start another suction stroke.
Incorporating the same valveless design, FMI developed and patented the Chloritrol(R) system to precisely inject sodium or calcium hypochlorite solution 24/7 into potable water to assure purity of the water supply.
The unique part of the system is its utilization of two separate pumps coupled to a single drive motor. One pump continuously pulls a gas/liquid mixture past a liquid separation column and returns the mixture to its supply vessel. A second pump (pressure-injection pump) draws degassed liquid, flooding the input, and provides gas-free chlorine to the injection point. Pinkerton says the design is self-priming against 100 psi pressure without the priming procedures necessary with other pump designs. No recalibration is ever needed, which Pinkerton says is impossible with valved piston and diaphragm pump systems that lose prime because compression/expansion of the gas slug causes valve float and air lock.
For more information and to see how the FMI valveless ceramic piston pump works, go tohttp://www.fmipump.com.
About the Author(s)
You May Also Like