Mechatronics Improves and Speeds Up fMRI Scans
September 2, 2008
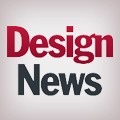
The inside of an MRI cavity is precisious real estate, why would you want to share this potentially closterphobic space with a robot?
In a recent release of the IEEE/ASME Transactions on Mechatronics, one article particularly caught my attention. Functional MRI scans (fMRI) are a type of brain activity scan where an image of brain activity, based on blood flow, is captured every couple seconds. The patient is often told to do a specific task, but these tasks are limited within this space. This single degree of freedom robot, more similar to an actuator, can provide resistance, measure a patient’s force, or guide a patient’s hand in a certain way. This all happens while inside of a machine where a single hair pin could be deadly. A typical fMRI machine produces a magnetic field of 3 Tesla and sometimes as high as 6 Tesla. The earth’s magnetic field is on average 0.00004 Tesla, or 75,000 times weaker than a fMRI magnet.
Shown above, the entire actuator must be made of materials that do not interfere with the magnetic field of the fMRI machine, must be guaranteed to work properly while inside the machine and must not make the 55cm to 70cm aperature of the MRI any more cramped than necessary. The senors, actuators, and device structure are simple to implement out of traditional parts, but these must not cause interference with the magnetic field. This rules out all electronic sensors and ferromagnetic transmission wires, as the metal would be dangerous in the magnetic field, but also an electronic sensor would be innacurate in such a strong magnetic field. The paper compares the options between hydrodynamic and pneumatic actuators.
These actuators use fluid lines instead of electrical lines to ‘transmit’ force to an electronic sensor at a large distance from the MRI machine. The best part of a fluid line is how it is actually a wonderful physical analog of electrical system: voltage as pressure, and current as volume flow rate. This simply means that if the tubing does not expand, and the fluid is not compressible (water is not very compressible), that a hydrolic line, esentially a polymer pipe, is perfect for this application. The fluid and the pipe are magnetically inert, ‘power’ in the form of water pressure can be created at a distance from the MRI unit and sent to the actuator. The end effector, or handle the patient moves (pictured previously), is relatively easy to create out of MRI safe and non-interferring materials.
This system is a very simple mechanical and electrical system, but it is a vast improvement over an operator telling the patient to move their fingers. Now there is a quantifiable measurement of force linked with the brain activity. I find simple solutions that are novel, realiable, and useful are some of the best mechatronic applications. In order to see these solutions, often you have to have experience looking from all angles at a problem. Engineers who are educated at the union of different fields who will make progress to solve some of our most complex problems.
Original article at IEEE (IEEE membership and subscription required)
About the Author(s)
You May Also Like