Thermoforming Advances Medical Design
June 17, 2014
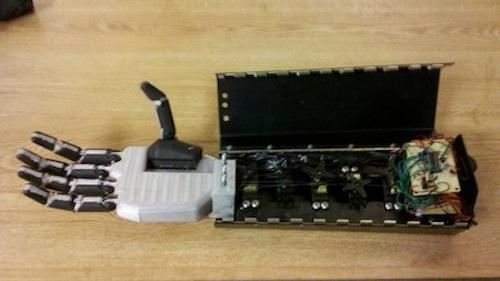
Although technology is the star in medical devices from MRI and blood analysis machines, to CT and PET scan equipment, it could not function without the custom covers, panels, housings, enclosures, and other parts that provide sensitive electronic components needed structure, protection, and aesthetics.
Custom medical device parts have long been made from thick-gauge thermoformed plastics for cost-effective quality and cosmetics, and recent advancements in thermoforming technique and technology have increased the advantages of doing so.
As a manufacturing process, thick-gauge thermoforming traditionally involves heating a 1/16-inch to 5/8-inch plastic sheet to a pliable forming temperature, shaping it in a mold, and then finishing it into a usable part. The result is an extremely durable, anti-abrasion, lightweight, thermoplastic part with crisp features and fine surface detail.
With recent advances, however, medical device designers and manufacturers now have a range of new options, starting with a thick-gauge thermoforming capability of some vendors to create parts up to 9-ft x 13-ft, large enough for even the largest MRI covers.
Beyond this are new choices ranging from built-in, anti-microbial agents to a twin-sheet thermoforming process that simultaneously thermoforms two sheets of plastic and bonds them together. Additional options include screen-printing, hot stamping of logos, and even assembly, fabrication, and fulfillment.
Oversize medical parts
MRI, PET, CT, and other medical equipment designed to image an entire human body, or significant parts of it, can be massive. Even X-ray, radiology, mammography, incubator, and diagnostic blood analysis equipment can be large and bulky.
For larger parts, the traditional approach has been to use molded fiberglass. However, fiberglass has size, wall thickness, and radii limitations, and is typically heavier. This is not the case for oversized thick-gauge thermoformed parts, which are lighter and stronger at half the cost.
Thermoformed plastic is the logical upgrade from fiberglass when large medical parts, panels, housings, or enclosures are needed that must be durable and lightweight, yet aesthetic and affordable. Yet creating parts large enough to encompass the entire human body is unique to all but a few thermoformers because it requires a large capital investment that only a few can make. These systems are capable of thermoforming parts up to 9 ft x 13 ft with a 60-inch draw, which Kintz achieves using a very large four-station rotary thermoforming machine.
Built-in anti-microbial protection
In healthcare, it is particularly important to maintain a hygienic environment to restrict the spread of disease or contaminants. But that can be difficult in a clinical setting, with a variety of patients and personnel using medical devices, even with routine equipment cleaning.
One helpful new option for medical device manufacturers is to add an anti-microbial agent during the manufacturing process that fights microbes such as bacteria, fungi, mold, and mildew for the life of the product. When the anti-microbial agent is spread throughout the thermoformed material, its protection is effective both on its surface and in its substrate, and will not wash or wear off.
Twin-sheet thermoforming
For medical device parts, panels, or enclosures that will be seen from both sides; need added strength; or will house insulation, mechanical, or electronic components, an advanced vacuum-forming technology called twin-sheet thermoforming is ideal. The process simultaneously thermoforms two sheets of plastic, then bonds them together to create a double-walled structure that is durable, lightweight, and economical.
About the Author(s)
You May Also Like