Technology has steel shining like new
December 2, 1997
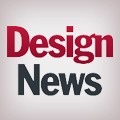
Steel has been the backbone of machine and structure for almost two centuries. This fact tends to give the material a classic disposition: after all, the steel cap of that art deco exclamation point, the Chrysler Building in New York City, came from the foundries of Germany's Krupp. Designations such as "the Rust Belt" to describe sections of the Northeast and Midwest add to this view. Steel's antiquated air is all the more pronounced when stacked up against composites, ceramics, and other "modern" materials. Even aluminum is new again by comparison.
Nevertheless, sometimes there's nothing else for it: Steel remains the material of choice for heavy industry, toolmakers, and many component manufacturers; hardly quaint sectors of the economy. The powder metallurgy (PM) industry is maturing and growing into new applications, largely on the strength of steel and steel-based alloys. Furthermore, steel suppliers are very active devising new formulations of their products to improve strength, machinability, wear, and corrosion resistance.
"In the last 10 years, the world's consumption of stainless steel has doubled," remarks James Baker, president of Sandvik Inc. (Fair Lawn, NJ). "We are using more steel than ever before in history. This fact has motivated us to continually develop and refine our steel products, tools, and processes."
Old is new again. Sandvik's historical presence dates back to the 19th century, where it began life as a provincial Swedish firm. At that time, steel was in a class by itself and Sandvik's only competitors were other steel firms, each of which tended to serve a particular geographic area. Today, manufacturers have a greater variety of materials to choose from, and steel companies have to scramble to stay current and competitive.
Some of these efforts are aimed at eliminating some of the barriers to using certain classes of steel. Stainless steel, in particular, is in demand for its high tensile strength and corrosion resistance. However, the metal has acquired a reputation for being difficult to work: a reputation Sandvik does not dispute.
"Historically, stainless steel has had to be machined very slowly and is hard on tool life," says John Israelsson, product manager for rotating tools at Sandvik Coromant, the company's tool-making arm. "This puts a damper on production rates and increases manufacturing costs."
Sandvik as an operation has half a dozen separate businesses, all of which operate semi-autonomously. Baker says his company used this structure to attack stainless steel machining from two sides. On the one hand, Sandvik Steel formulated its SANDMAC alloys to reduce some of the machining difficulties encountered with 304-and 316-grade stainless steel. On the other, Sandvik Coromant developed its M-Line tungsten-carbide inserts specifically optimized to machine SANDMAC stainless steel.
The SANDMAC 304 and 316 stainless steels use sulfide and oxide impurities that promote chip-breaking and have a lubricating effect at high cutting speeds. "Adding impurities to stainless steel is nothing new," says Philip Belejchak, marketing manager for Sandvik Steel. "The real trick in developing SANDMAC was being able to maintain the desirable properties of corrosion resistance and strength."
Sandvik Coromant's M-Line inserts have their composition, geometry, and coatings tailored to compliment the new stainless steels. The inserts have cobalt-enriched surfaces to strengthen their cutting edges. The positive-rake geometry promotes a soft cleaving-type cutting action that extends tooling life and improves surface finish. Titanium carbon-nitride and aluminum-oxide base coats and a titanium-nitride top coat protect the M-Line inserts from heat and prevent chips from sticking. The M-Line is available in rough, medium, and finishing geometries.
Another downside of stainless steel is that it does not wear very well. "That shortcoming has caused perplexing alloy selection problems when stainless steel parts are in metal-to-metal contact under heavy load, without benefit of coatings or lubrication," says John Magee, senior metallurgist for stainless and high-temperature alloys at Carpenter Technology Corp. (Reading, PA). "Options, of course, are limited when lubrication (a) cannot reach the mating parts (b) cannot be used because it could compromise product purity, or (c) would break down under high temperatures."
To meet the need for new stainless steels that would provide improved wear resistance, Carpenter developed two new high-silicon, high-manganese, nitrogen- strengthened, stainless alloys which possess superior resistance to metal-to-metal wear and galling, which is when metal components rub together at low speeds and high loads.
Gall-Tough stainless, the first alloy introduced, displays higher strength and high- temperature oxidation resistance than conventional 304-and 316-grade stainless steels, depending on the environment. The alloy is essentially a type 304 or type 316 upgrade with much improved galling and wear resistance. The new grade has high tensile strength, increases the life of parts in metal-to-metal contact, and resists excessive wear under heavy load without lubricants or coatings.
Focus on processes. Solutions that feature improved processes rather than new alloy formulations are being considered throughout the world. A new heat treatment process developed at the Belarus State Polytechnic Academy increases the performance, service characteristics, and life of high-speed steel components.
According to Alexander Shmatov of Belarus State Polytechnic, a new regime of hardening and tempering produces a hardened surface layer of a desired thickness with a high content of coarse and fine carbide particles, and a ductile core having uniform fine-grained structure characteristic. This actually modifies the structure of high-speed steel, producing a composite material.
"As compared with standard heat treatment regimes, the process offers an increase in impact strength by the factor of 1.5 to 2.5 and improves tensile strength by 10 to 20%," Shmatov says. "The surface hardness is by HRC 1-6 higher and the core hardness is by HRC 1-3 lower than those obtained after conventional heat treatment, which contributes to the improvement of service characteristics."
In practice, the new process has proven effective for producing tools that experience high-impact loads, such as small-sized tools and tools used in rough machining. Currently, about 10 companies in Belarus and Russia are producing high-speed steel tools with the new process. Small lots of hardened end mills were tested in the Czech Republic, Slovakia, China, and Germany. "The process gives an opportunity to use the tools in machining regimes with the feed and cutting speed increased by 10 to 30%," Shmatov adds. "What's more, the process uses conventional heat treatment equipment and does not require additional hardware."
Perhaps the hottest new metal-forming process is metal-injection molding (MIM). Kinetics Inc. (Wilsonville, OR) points out the metal-injection-molding industry in the United States is only a decade old. Nevertheless, North American industry sales are reported to be near $60 million, and growing at more than 30% per year. The company, which is the fourth largest MIM vendor in the U.S., attributes the growing popularity of the technique to the level of design freedom it offers for metal components--on par with the flexibility of plastic injection molding for the plastics industry.
Kinetics claims the technology produces very-high-density parts with mechanical properties superior to powder metallurgy, and comparable to wrought materials. The MIM process starts by combining fine metal powders with a polymer binder to create a feedstock suitable for injection molding. After the feedstock is compounded, the material is injected into standard plastic injection molds that have been designed about 20% larger than the desired final product.
An oversized mold is required due to the presence of the binder, which is subsequently vaporized from the molded part in a furnace. The resulting part is sintered at temperatures above 2,200F, which fuses the fine metal particles together, shrinking the part to the final shape and size in a predictable manner.
Many of the same design principles used for designing plastic parts apply to designing MIM parts. They will exhibit features characteristic to the molding process, such as parting lines, gate, and ejector pin marks.
Stainless steels take a powder
According to Louis Desrosiers, president, Precitech, Inc. (Quebec, PQ, Canada), there are many reasons for choosing stainless steel. These can range from the aesthetic (color and surface appearance) to those based on technical considerations, such as corrosion and oxidation resistance, good ductility and wear resistance, elevated temperature and impact strength, and machinability.
"However, the corrosion resistance of PM stainless materials was never close to that of wrought materials," Desrosiers notes. "The inherent porosity of PM parts increases crevice corrosion." Precitech is exploring a number of approaches to improve the corrosion resistance of stainless PM parts. In particular, the sintering process shows the most cost-effective promise.
Desrosiers says Precitech researchers have found that corrosion resistance of PM parts increases as the sintering temperature is raised. Sintering stainless steel parts at 2,350F (1,288C) promotes the deoxidation/reduction of oxides that inhibit metal-to-metal bonding of powder particles. In addition, controlling the sintering atmosphere to optimize nitrogen absorption results in significant improvements in mechanical properties and corrosion resistance.
Traditionally, sintering is performed at a temperature of 2,050F (1,121C), since the metal belts used to transport the product through the furnace have a significantly reduced life above this temperature. High temperature sintering--processing at more than 2,100F (1,150C)--can be performed in a pusher, walking beam, or vacuum furnace, eliminating the limitations imposed by the belt.
The growing demand for PM stainless steel parts has led to new formulations aimed at overcoming some of its drawbacks. Hoeganaes Corp. (Riverton, NJ) is improving green (pre-sintered) strength of stainless metal powders with its Ancor GS-6000 family of PM premixes. Parts produced with stainless-steel powders traditionally have had inherently low green strength. This enabled corrosion-forming gaps to develop during sintering. Adding a premix of Ancor-6000 improves the green strength of powder stainless steel parts, resulting in better corrosion resistance.
MIM advantages
Tolerances of plus or minus 0.003 inch per inch or better.
Parts that would normally require four or more machine tool set-ups or cutter tool paths to produce.
Wall thickness to 0.5 inch.
Weights up to 100 grams.
Lengths up to six inches.
Annual quantities of 20,000 pieces and up.
Material density at 97% of theoretical.
Material strength near that of wrought materials.
Surface finish of 16 to 32 RMS.
Source: Kinetics Inc.
About the Author(s)
You May Also Like