Swelling fluids allow design engineers the chance to develop cutting-edge tubing systems while meeting safety protocols and environmental responsibilities.
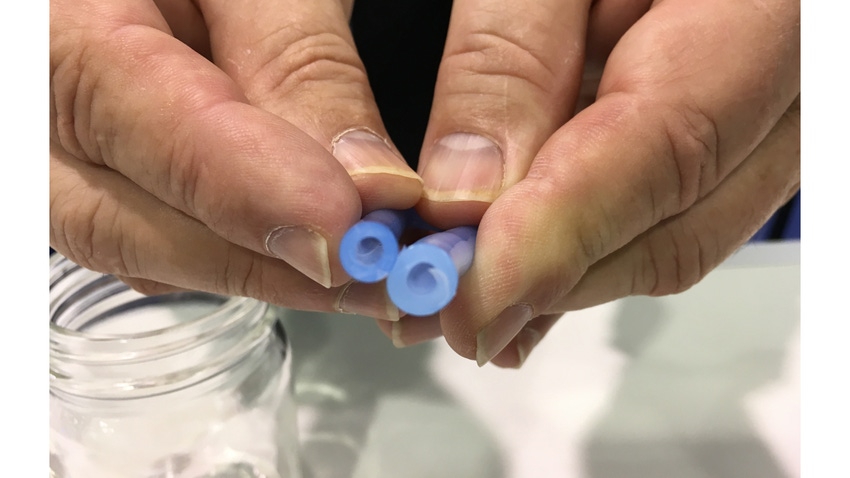
Every development drives progress in the rapidly advancing engineering world, where precision designs must align with tight manufacturing schedules. Among the advancing solutions shaping assembly processes, engineered swelling fluids have emerged as a cutting-edge technology, revolutionizing how design engineers approach their work.
Engineered swelling fluids are designed, formulated, and produced specifically for swelling tubing. These innovative fluids offer a combination of efficiency, effectiveness, and environmental consciousness, facilitating seamless connections between diverse materials such as silicone, polyurethane, and thermoelastic tubing to fittings and molded parts. By utilizing engineered swelling fluids, engineers have a higher level of flexibility that expands design possibilities across diverse industries.
Assembly Challenges
Connecting tubing and hoses made from silicone elastomers to rigid parts and textured fittings has historically challenged engineers. While silicone is flexible, it will not easily expand or stretch without assistance. It also has a high coefficient of friction (tacky surface) that makes sliding a silicone tube onto a fitting difficult.
Traditional press-fit assembly methods are slow and labor-intensive and often difficult to achieve with today's tight tolerances and complex geometries. This issue is particularly prominent in medical technology, where innovative designs incorporate advanced tubing to enhance patient care and ease of use for healthcare providers. Specifically, multi-lumen tubing for fluid, medication, gas transfer, guide wires, and venous access devices like catheters, dialysis machines, and other critical applications faced with joining complexities.
As well as the medical sector, tubing connection challenges arise across diverse industries and applications, for example:
Automotive manufacturing: Brake lines, fuel systems
Aerospace production: Hydraulic and climate controls, engine systems
Appliance assembly: Refrigerant lines, water lines
Filtration system assembly: Water and purification systems
Robotics manufacturing: Pneumatic actuators and pumps
Swelling Methods
Fortunately, there are tube swelling methods and fluids that help expedite manufacturing and assembly. Engineers now have access to four primary joining techniques. The first method, which utilizes isopropyl alcohol (IPA), is easy to obtain and has proven to be an effective method in lubricating and swelling tubing during assembly. However, IPA’s slow drying time and limitations with thin-wall tubing have rendered it less versatile for certain applications. Moreover, complications may arise later in the device's lifecycle if the assembly isn't completely dry.
An alternative approach is the use of silicone oils, which boast excellent compatibility with silicone tubing. While effective, these oils can be messy, can migrate through production facilities, and can even trap surrounding dirt, raising contamination concerns.
The third option is hexane. Hexane swells silicone tubing effectively, but with its volatile nature and potential for material damage, it proves less favorable for many applications. Additionally, hexane requires precautions during use given its intense odor and hazardous properties. Proper ventilation or personal protective equipment is essential to mitigate risks of exposure. Furthermore, hexane is classified as a hazardous air pollutant and may negatively impact air quality if emissions are not controlled, making it less suitable for some applications.
The fourth option, engineered silicone-based swelling fluid, stands out as the most efficient and innovative approach. It temporarily enlarges tubing diameters, enabling quick yet robust fitting of connectors that were previously difficult or impossible with traditional assembly processes.
Engineered swelling fluid technology works by immersing one end of a silicone tube in the solution. This causes the tubing wall to expand rapidly yet evenly. Soaking time can be finely controlled, with exposure for less than a minute typically sufficient when 1-2% enlargement is needed for insertion into textured connectors and barbed fittings. The quick, controlled swelling action enables smooth and simple assembly. The fluid's composition leaves the tubing's chemical structure and fitting's physical properties untouched, ensuring a reliable and secure connection. Once the tubing is attached to the fitting, the swelling fluid quickly evaporates, leaving no residue, and the tubing returns to its original size and durometer.
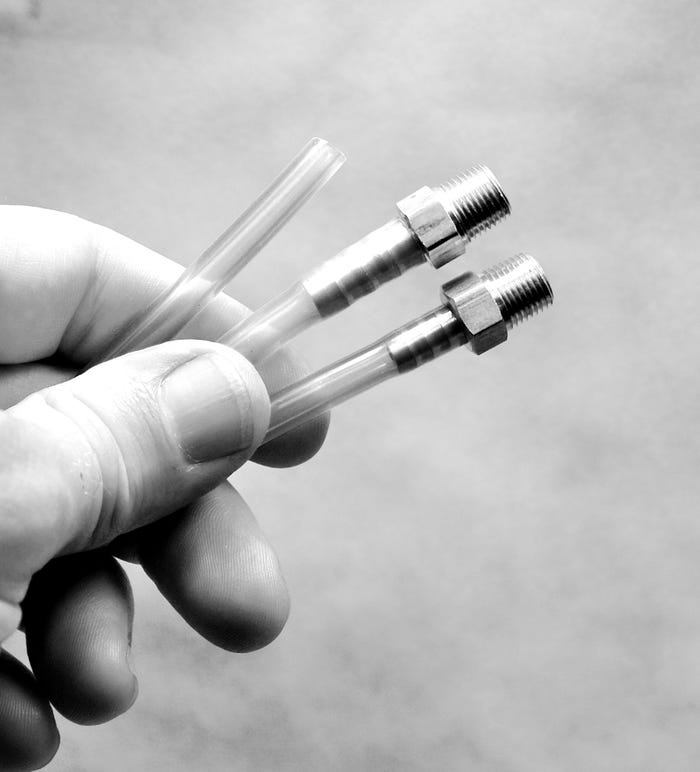
Swelling fluid allows tubing forms a robust, completely sealed connection over the fitting regardless of geometric complexity. MICROCARE LLC
The Benefits of Swelling Technology
Several key benefits of using engineered swelling fluids enable the next generation of optimized and integrated tubing systems.
Stronger Connections. When used with swelling fluid, tubing forms a robust, completely sealed connection over the fitting regardless of geometric complexity. Unlike bonding or welding, the swelling process does not permanently fuse the tubing and fitting, enabling simpler disassembly when needed and easy re-design.
Design Flexibility. Swelling fluids readily accommodate the newest material innovations like thin-wall tubing and multi-lumen profiles. They also enable more freedom when designing complex geometries that are difficult to seal with hardware or sealants.
Efficient Processing. Application of swelling fluids takes less than a minute in most cases. The rapid swelling action makes inserting tubes onto fittings much easier compared with manual pressing and twisting. This prevents damage to fragile components while increasing production throughput. Clean-up is also fast since the fluids fully evaporate after assembly. The consistent swelling performance also minimizes rework versus mechanical joints that depend heavily on installer skill.
Worker Safety. The smooth, low-force assembly with swelling fluids reduces repetitive motion injuries. Workers avoid the strains of forcibly pressing and twisting tubing connections. Unlike hexane, engineered swelling fluids demonstrate lower toxicity and reduced potential for skin and eye irritation, contributing to a safer work environment.
Environmentally Responsible. While some swelling fluids use solvents like hexane, engineered solutions are safer and more sustainable. The newest swelling agents utilize ingredients like methyl siloxane that are non-toxic, non-flammable, and not hazardous air pollutants. Their low global warming potential meet stringent environmental standards. With no ozone-depleting potential and zero hazardous air pollutant classification, they provide a responsible swelling solution for manufacturers.
Design Freedom. Swelling fluids remove traditional barriers, allowing product designers to experiment with complex geometries and multi-component assemblies. This enables the integration of shapes and profiles that drive the development of highly engineered, cutting-edge products. Swelling fluid options are also available for the many tubing materials used in today’s designs, including neoprene, EDPM, polyethylene, polypropylene, polyimide, and other molded thermoelastomers.
Waste Reduction. Swelling fluids prevent damage during manufacturing by simplifying the insertion process and eliminating the high forces that cause tubing failure. This minimizes discarded materials, defective products, and associated expenses. Reduced waste by using swelling fluids promotes environmentally and economically sustainable manufacturing practices.
Simplified Validation. Engineered silicone swelling fluids selectively target silicone tubing, leaving other materials like polycarbonate, polyurethane, and metal components unaffected. Minimal fluid absorption enables lower product weight gain, faster tubing recovery, and reduced swelling agent usage. With no heat, adhesives, or other additions introduced in the assembly process, swelling fluids simplify qualification and validation protocols. Their residue-free operation also maintains cleanroom integrity for medical device manufacturing. By avoiding changes to material properties, swelling fluids streamline regulatory approval.
Transforming Design
Swelling fluid technology is enabling design engineers to push boundaries and create integrated tubing systems of the future. Using engineered swelling agents, tubing can be easily joined to complex geometries and diverse materials. This technology provides stronger connections, increased production efficiency, and simplified validation protocols—allowing designers to experiment with cutting-edge tubing systems while meeting safety protocols and environmental responsibilities.
About the Author(s)
You May Also Like