Aluminum Catches Up to Carbon Composites
April 1, 2011
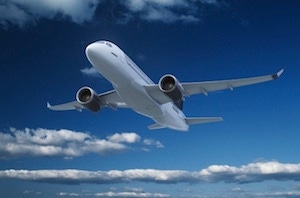
The race tocarbon composites in aircraft structures is anything but a sure bet, says a topexecutive at Alcoa, America's leading aluminum producer.
"Industryperceptions have changed very dramatically over the last three to five yearsfrom favoring composites to being fundamentally a dead heat," says BillChristopher, executive vice president at the Pittsburgh-based company. "Toparaphrase Mark Twain, we believe that the rumors of the demise of the aluminumstructure are greatly exaggerated."
He based hisstatements on research conducted recently by Alcoa and pointed to three recentaircraft designs as proof.
Aluminum Catches Up to Carbon Composites_A |
Designed forthe 100- to 149-seat market category, The Bombardier C Series uses largeamounts of composites like the Boeing Dreamliner and the Airbus A350. But itsairframe makes intensive use of new lighter weight aluminum lithium alloysdeveloped by Alcoa. The first flight of the Canadian aircraft is expected nextyear.
Anotherregional jet, the Chinese-built ARJ21 also has analuminum-intensive airframe.
The initialdesign of the Japanese MitsubishiRegional Jet called for composite wings but engineers shifted to aluminum"for a lot of very good reasons," says Christopher.
Officials atthe OEM said that use of an aluminum wing box will allow for a shorterlead-time to make structural changes. The wings, for example, can be optimizedto match the attributes of each member of the MRJ airplane family. First flightis expected next year.
"The nextbattle ground will be a single-aisle aircraft," says Christopher. "For shorterroutes, weight reductions (from carbon composites) don't translate into as muchsavings." Another issue is that regional, single-aisle aircraft take off andland more frequently than large planes such as the Dreamliner and A350. Theytake more punishment.
Christophersays that aluminum has more damage tolerance than carbon composites. "Also, youcan see damage in aluminum much easier and repair on aluminum is much easier,"he adds.
One big advantageof carbon composite structures is a requirement for less frequent Inspection intervalcycles. Alcoa has developed new aluminum alloys that have improved corrosionresistant and are 5 to 10 percent lighter than the alloys that were availablewhen design decisions were made from the Dreamliner. And more gains are comingwith aluminum-lithium alloys under development, advanced structural conceptsand other new technologies being developed by Alcoa researchers, according toChristopher.
One newstructural concept is called selective reinforcement. Aluminum-lithium sheetreinforced with glass fibers is placed in specific areas that need to be strengthened.
Christophersays that Alcoa's next-generation structural technology will be less risky and30 percent less-expensive to manufacture, operate and repair than currentgeneration carbon composite structures. In his opinion, aluminum will also catch up tocarbon composites on passenger comfort areas such as large windows, higherhumidity, and higher cabin pressure.
However, improvements,of course, are also coming in carbon composite systems.
About the Author(s)
You May Also Like