Linear Bearing Misconceptions
February 16, 2009
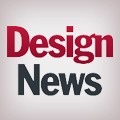
Achieving the highest levels of performance with linear motion systems requires careful attention to detail, engineering know-how and applications' experience. Below are 10 areas where proper understanding of materials, lubrication, surface finish and other variables can make the difference in the performance of linear systems.
All Steel Shafts Are the Same
The most commonly used material for linear motion bearing shafts is moderate high-carbon steel. Engineers should verify that the carbon content of the steel used, straightness, roundness, surface finish, hardness and case depth are adequate for the application. Contaminants can result in premature failures due to high Hertzian contact stresses.
Chemistry and lack of uniformity can affect the machinability of shafting, particularly the ability to minimize asperities or high spots. It is better for the surface to consist of plateaus with some valleys than peaks and valleys. Hardness and case depth has to be adequate to support the Hertzian stresses under high bearing loads.
Linear Bearings Cannot Be Used in Adverse Environments
Attention to detail, design configuration, proper sealing and selection of materials are important factors when using linear bearings in cryogenic or marine environments. One trap to avoid is forgetting the thermal effects of sizing for significant temperature swings because gaps are affected in the axial and radial fit-up. Special sealing and lubrication options with scrapers may be required. When selecting coatings and materials, salt spray testing may not definitively measure corrosion resistance for your specific application.
Thin Dense Chrome (TDC) has better wear characteristics for rolling contact bearings than Thin Dense Nickel (TDN) because of its hardness rather than improved frictional characteristics. TDN is better than TDC in a standard salt spray test, but doesn't perform as well against bearing contact stresses.
The More Osculation the Bearing Race Has with the Rolling Element, the Better the Load Capacity
A common misconception is that the higher the load capacity, the better the bearing. With rolling element bearings, the ratio of the groove radius to rolling element radius is the osculation factor. For a given stress capacity as limited by the material properties, an increase in geometric conformity (osculation) increases the contact surface area, increasing the load capacity of the bearing.
There is a limit, however, as the osculation becomes too high. Performance starts to degrade and the load capacity goes down partly due to the increase in the differential tangential shear as a function of relative surface velocities. Compound this with the reduction in tolerance allowance and higher osculation factors manifesting higher frictional characteristics, and too much osculation is a bad thing.
Lubrication Is No Big Deal
While medium weight lithium grease may be suitable for bearing applications, it's not true that lubrication is lubrication, or that grease is better than oil as a bearing lubricant. The choice of proper lubrication is a function of the linear bearing application and can be the difference between full or inadequate performance.
The film layer that exists between the rolling element and the bearing race is the Elasto-Hydrodynamic Layer (EHL). This lubricant layer supports extremely high stresses and is subjected to both physical and chemical attacks that could break down the lubricant that serves as the primary protection of the bearing surfaces.
Lubricants range from high viscosity greases with EP additives for high load applications to low viscosity oils with preservatives for chemical protection, from synthetics for reduced viscosity breakdown or resistance to evaporative loss, to natural or organic for low friction characteristics or compatibility considerations. Special lubricants are designed for noise damping, or to withstand oxygen-rich environments or extreme temperature conditions.
Running a Linear Bearing Faster Will Shorten the Bearing's Travel Life
Plain contact bearings, and to a lesser extent radial bearings and fluid film bearings, can be highly sensitive to speed as a factor in bearing travel life. But interestingly, rolling contact linear bearings' travel life is only affected in as much as speeds and accelerations may affect system loading. As long as the movement profile is accounted for with respect to affect on loading, linear bearings are not pressure velocity (PV) dependent, sensitive to heat rejection issues, nor subject to macro-film layer support issues.
Rolling Contact Elements Do Not Wear
While rolling contact elements do not wear as much as sliding contact bearings, there is wear on a micro-scale. In bearings with significant osculation geometry, there is a difference in the relative tangential surface velocity between the rolling element and the bearing race. The surfaces are effectively not traveling at the same speed. This differential can result in shearing of the lubricant that would break down the viscosity of the lubricant film and the EHL that would lead to premature failure. Depending on the loads and environmental conditions, this would mean higher frequency re-lubrication cycles may be required.
Surface Finish Is No Big Deal
Not all surface finish callouts mean the same thing. Sometimes looks can be deceiving. The surface finish can be called out as Ra, Rrms or Rpk, etc. Some surface finishes are based on average readings, some on peak to valley or peak to peak readings. When it comes to bearing load life performance, surface finish is a big deal. Typically the designer has to be careful of the high spots. For the same surface finish value, a surface finish with plateaus, rather than peaks, in combination with the low spots or valleys in the material is preferred.
Too rough a surface finish usually means more asperities (spikes or high spots) that would harm bearing performance. Too fine a surface finish could affect the ability of the lubricant to form a proper film layer on the bearing surface, also negatively affecting bearing performance. For most cases, one would not want a surface finish below a 2 Ra for this reason.
By Using a Lower Profile Bearing, the Height of the System Will Be Lower
There is trap many designers can fall into when specifying a linear bearing in search of more compactness and lower profiles. That trap is the oversight of some other parameter or component aside from the linear bearing that actually determines the overall system height. Often the drive system, mount, motor or gearbox can limit how low a profile is practical for the system. This oversight sometimes requires the designer to put in spacers or risers under the compact low profile linear bearing to properly mate up with the drives, motors or mounts.
When a Shaft Grooves, the Shaft Is Failed
Counter to intuitive belief, shaft grooving is not necessarily bad. Linear bearings running at high loads sometimes groove the shaft after the first few passes, a phenomenon called "shakedown." When bearings are run at high loads, the Hertzian contact stresses are quite high enough to yield even hardened high carbon bearing steel. Because this is a compressive condition, the yielded material doesn't not move or shift to cause a subsurface dislocation sufficient for material failure or fracture. It stabilizes at a level where the actual contact stress is now below the equivalent stress due to the increased contact area achieved by the grooving. If this phenomenon occurs, where the shaft initially grooves and then stabilizes, the engineer should not rotate the shaft or replace the shaft. The bearing would be subjected to another shakedown and the balls could have its limits if they are not sufficiently hard.
Higher Material Hardness Means Better Bearing Performance
Higher material hardness means a higher yield stress limit, but this is not necessarily a good thing. Higher hardness can also mean increased brittleness. This would mean the material toughness would be compromised. It would break before it bends and sometimes bending is a good thing.
There is also the aspect of balance. Proper hardness for the proper bearing component optimizes bearing performance. The standard linear bearing has fundamentally three primary load bearing components: the inner race, the rolling element and the outer race. If the ball is much harder than the inner race, it could yield the inner race due to the high contact stresses. If the ball is much softer, then it could be yielded, resulting in flat spots on the ball. Typically the outer race sees more cycles than the inner race. A slightly higher or lower hardness relative to the rolling element is more desirable to optimize bearing performance.
Author Information |
Al Ng is director of engineering, rails, guides & components for Thomson Industries, Div. of Danaher Motion. |
About the Author(s)
You May Also Like